Roads are the backbone of every country’s economy, with South Africa’s ranked 10th in the world in size, with an approximately 750 000 km network – of which close to 160 000 km is currently paved.
IMIESA talks to Robson Francis, technical manager at National Asphalt, about his company’s role in providing sustainable road surfacing solutions.What is National Asphalt’s niche market focus and operating philosophy?
RF Since inception in 1988, National Asphalt has been a market leader in the manufacture and supply of hot and cold mix asphalt products for the South African market. Our growth has been driven by an investment in technical expertise in conjunction with ongoing research and development (R&D) to provide sustainable solutions for any flexible pavement requirement, from low-volume roads to national highways. Product excellence is a given; however, service excellence is even more important and is central to all we do. As testimony to this, over the years, we’ve retained and grown a loyal customer base.What is National Asphalt’s current production capability and what types of fixed and mobile plants are employed?
We’re equipped to support customers nationally in South Africa. Our static commercial plants are based at Rustenburg, Laezonia, Bon Accord, Middelburg, Nelspruit, Vanderbijlpark and Portland. In turn, our mobile plants have the flexibility to support projects locally and cross-border, where we also have a commercial plant operation in Gaborone, Botswana. Currently, our mobile plants are stationed at Aliwal North, Pienaarsrivier and Tzaneen in South Africa, as well as in Ondangwa, Namibia. In terms of combined capacity, our static and mobile plants are geared up to supply the market with at least 7 000 tonnes of asphalt per day.How important is quality control and certification?
It’s essential and the foundation for excellence. National Asphalt is ISO 9001 certified, and we are currently preparing the groundwork for Sanas accreditation in terms of ISO 17025:2017. The latter standard covers the general requirements for the competence of testing and calibration laboratories and aligns with our strict adherence to quality control and ongoing R&D programmes. Having these accreditations provides peace of mind for the client, knowing that the test results submitted for each batch of asphalt manufactured are exactly within specification. From our perspective, that’s equally important since some clients require a minimum five-year performance guarantee on hot mix asphalt formulations. We also encourage and extensively participate in correlation testing with accredited laboratories to measure ourselves against industry benchmarks.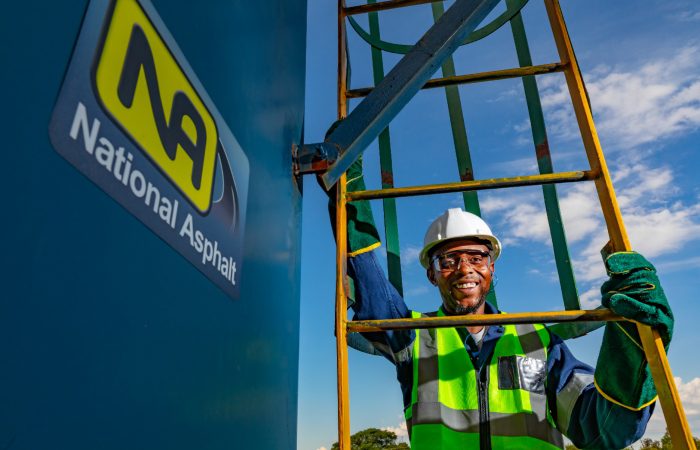
How will Sabita 35/TRH 8 influence future mixes?
The introduction of the Sabita 35/TRH 8 – Design and Use of Asphalt in Road Pavements manual advances the move towards performance grade (PG) specifications for hot mix asphalt in line with global best practice. The key focus is on ensuring asphalt longevity to maximise the return on investment for asset owners. Sabita 35/TRH 8 has already been implemented for Sanral projects, as well as by South Africa’s three toll road concessionaires. We are currently preparing our commercial sites to be Sabita 35/TRH 8 ready by running mix designs that we anticipate may be requested by the market. Each of these mix formulations takes upwards of 12 weeks to finalise, so perfecting the process up front enables more immediate delivery to market. Each of our commercial and mobile sites has a dedicated laboratory. All laboratories are equipped with basic Marshall testing equipment, while most of our commercial plants already have the latest industry-specific equipment to test according to Sabita 35/TRH 8.What are some of the challenges in implementing Sabita 35/TRH 8?
Now that Sabita 35/TRH 8 has been introduced for current and future pavement mix designs, the industry will need to transition from the current Marshall stability method first introduced in the USA around 1939.In the interim, the South African roads industry has these dual-specification parameters, each of which requires different and specific test methodologies. However, the Sabita 35/TRH 8 test method is far more precise and uses the latest technologies.
PG is the future. Therefore, concerted training is required for universal adoption of Sabita 35/TRH 8 by all roads authoritiesand municipalities.
Are there any new developments in National Asphalt’s hot mix line?
The production of hot mix asphalt represents the bulk of our business activity. Most often, mix designs are contract specific, since each project has its own unique characteristics in terms of aggregate source, binder type and overall design. So, the client or engineer specifies the type of mix required. Sometimes, we’ll work on a custom solution depending on the project complexity. However, to meet most project requirements, facilities like our Portland commercial plant have more than 40 off-the-shelf mix designs ready to go. An exciting new R&D project is the development of our own proprietary PG specified UTFC (ultrathin friction course) brand, NATGrip®, which is currently in the certification process by Agrément South Africa. NATGrip passes on key benefits in terms of skid resistance and drainage, and has been developed based on our more than 24 years of applied experience. NATGrip is open-end, area and traffic specific. For a high-trafficked road, we may recommend a modified binder and for a low-volume road, an alternative binder that’s more affordable and suitable. So, there’s great design flexibility. In the meantime, NATGrip performance trials are being carried out on various high-volume roads, and the test results to date are very promising. Our R&D team is also currently conducting in-depth laboratory studies on how compaction, asphalt type and binder type affects rutting and/or stripping for hot and cold mix asphalt.Where do you see the growth for cold mix asphalt?
Historically, the demand for cold mix asphalt – especially in the northern part of South Africa – has occurred during the summer rainfall season. However, evidence has shown that cold mix can be applied as an all-year solution forpothole repairs. Given the extent of South Africa’s maintenance backlog, there’s huge demand for cold mix, from both contractors as well as roads authorities and municipalities. This is also being escalated by public pressure to address our pothole pandemic. In response, we’ve developed our own unique product, NATPatch®, which is designed for high-quality repairs to bituminous and concrete surfaces and one of our best-selling products in this segment. Certified by Agrément South Africa, NATPatch can be supplied in bulk loads, or in 25 kg and 30 kg bags, and is ideal for labour-intensive construction. From an R&D perspective, we’ve benchmarked NATPatch against similar products available globally and believe that our solution provides best-in-class performance and durability. Simply put, NATPatch is designed to meet three
key criteria, namely ease of workability, a significant reduction in the degree of permeability, and longevity. Furthermore, NATPatch is continuously graded and has been rigorously tested in terms of rutting and stripping performance. Once installed, we guarantee a minimum working life of two years. Clearly, the less time between repair intervals,
the more cost-effective for municipalities, freeing up resources for other pressing social infrastructure priorities.
Is recycled asphalt (RA) a workable and sustainable solution?
Most definitely. The majority of our plants are RA capable and we’re in the process of upgrading the remainder. Going forward, the use of RA in asphalt should become the norm. RA passes on cost savings and – more importantly – is eco-friendly. From a sustainability perspective, RA helps to increase the longevity of available aggregate resources and lowers the bitumen requirement. While some might argue that a fresh virgin mix delivers the best results, it’s been proven that an RA mix can achieve the same or better performance thanks to innovations likebinder rejuvenators.
And in closing?
National Asphalt is on a rebranding mission under the slogan, ‘Excellence is not a skill. It’s an attitude.’ We continually strive for excellence throughout the business and are committed to being at the forefront of quality – engineering the best mixes for South African roads. Our focus to become even more agile through improved mobility remains at the forefront of our business strategy. Our employees are proud to be part of the National Asphalt family and to play an integral role in the future of South African roads. On that note, let’s hope the project pipeline increases exponentially going into 2023 and beyond.