Optimal fluid transfer is central to all process industries – from water and wastewater to the petrochemical and energy sectors – and pumps are the driving force that makes this possible. IMIESA speaks to John Montgomery, GM for APE Pumps and sister company Mather+Platt, about the group’s innovative approach to ensuring sustained delivery.
What defines the group’s excellence as an OEM in pump design, fabrication and execution?
JM The starting point is our rich history. Mather+Platt traces its roots back to the late 19th century as a pump manufacturer that evolved with the First Industrial Revolution in England. Since then, Mather+Platt has been a forerunner in pump system product development. The same is true for APE Pumps, founded in 1952. Both companies have led the market in terms of ongoing research and development for niche single- and multistage pump applications. Subsequently, we now also form part of multinational leader WPIL Limited.Seven decades in business is an exceptional track record. How has this been maintained and achieved?
Institutional knowledge is key. Every design drawing we’ve ever produced is on file so, irrespective of the date of manufacture, the group can either recondition or replace an APE or Mather+Platt pump from scratch. Plus, we have the in-house skills to execute this on a turnkey basis, with all materials sourced in South Africa. We invest in our people, with a major emphasis on keeping them up to date with the latest technologies, and our personnel are proud to work for APE Pumps and Mather+Platt. A high percentage have long service with the group, which reinforces our commitment to long-term customer relationships. Succession planning is another key focus, and we continue to recruit young qualified technical personnel at all levels to meet current and future requirements. This includes mechanical engineers, artisans and apprentices for specific trades that include fitters and turners,and patternmaking.
How would you define the group’s business model?
Foremost, we’re an OEM. In addition to this, we are a Grade 8 contractor in terms of the Construction Industry Development Board rating system, providing turnkey civil, electrical and mechanical engineering services for clients in South Africa and Africa. A prime example in terms of the latter are the systems upgrades we’ve completed for Malawi’s Blantyre Water Board over the years. Why is operations and maintenance (O&M) becoming a growing trend? There are various factors, but a key one is the cost optimisation benefits of outsourcing specialist skills to technology leaders that have decades of applied experience. OEMs are best equipped to enter into service level agreements (SLAs) – essentially O&M contracts – on their own systems. For industrial clients, as well as municipalities and water utilities, the advantage is that these O&M contracts are entered into on a fixed-cost basis, plus it’s an off-balance-sheet solution for the client. Our pumps are maintained optimally during the warranty period for new installations, and for their indefinite life thereafter. We conduct regular performance tests to ensure that all our pumps run 100% to specification. Currently, we have SLAs in place with leading public and private sector clients. As part of our commitment to excellence, we also provide training for our clients’ in-house technical teams.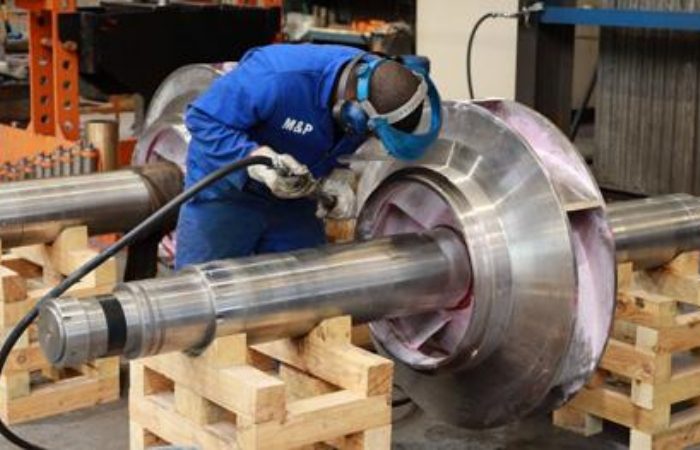
How are O&M and asset management interlinked?
Every asset must be designed with a clear indication of its projected life-cycle costing and lifespan. That’s a primary concern for any asset owner because they need to budget for predictive and preventative maintenance. Asset investments should never be allowed to run to destruction due to a lack of maintenance planning. Like any mechanically functioning system, best-in-class products need world-class service. They also require expert installation and optimisation.Physical inspections are part of our SLA but – thanks to the latest developments in telemetry, coupled with the group’s purpose-designed apps – all our pumps can be condition-monitored remotely 24 hours a day. Process elements monitored include flow rate at a given head, bearing temperatures and pump vibration. In the unlikely event of an unscheduled incident, the pump can be set up to shut down automatically or via remote intervention, with a maintenance team sent to site.
We now also employ digital twinning during installation, where we can verify the virtual model of the final design against the physical system recorded via lidar scans. This allows us to cross-check, match and verify all elements during commissioning.What’s the criteria for an SLA?
SLAs can be concluded for brand-new group installations, as well as on our older systems installed years ago. In terms of the latter, we guarantee to restore these pumps – irrespective of their current condition – to OEM specification at a saving of around 60% of the value of a new pump. We then maintain them from there on. Upgrades, like variable-speed drives, also significantly improve energy efficiency. A relatively small investment in an SLA definitely pays for itself by ensuring uninterrupted production, which is especially critical for water or wastewater utilities, or a power station. It’s all about having right the team onboard.How does your pump service exchange work?
We have an extensive inventory of new and reconditioned pumps on hand. This enables us to swop out a client’s pump when it needs an overhaul and replace it with a new one during a scheduled changeout operation. That provides major peace of mind for the client. We have also extended our facility in Germiston to house a full range of pump spares as backup for our extensive pump population and SLA clients in South Africa and Africa.Is the group investing in new fabrication machinery?
Absolutely. New capex investments include an 8 m lathe with a 1.4 m swing. We now also have what we believe is the second largest key cutter in South Africa, as well as a new CNC horizontal boring machine, plus we’re investigating the acquisition of 3D scanners to further enhance our existing qualitycontrol systems. We’re set up to do everything in-house. This extends from the design phase to the patterns, fabrication, machining, assembly, installation, alignment and commissioning.