A steady supply of quality aggregates from AfriSam is playing a key role in ensuring unhindered progress on one of government’s Strategic Integrated Projects (SIPs) – the N3 national route upgrade between Durban and Pietermaritzburg.
That the sheer scale of the project places immense pressure on local aggregates suppliers is no overstatement but, with two strategically located quarries in the area, AfriSam is rising to the challenge. Part of the 62 SIPs gazetted as part of the Infrastructure Investment Plan approved by Cabinet in 2020, the N3 national route upgrade – which focuses on an 80 km section from Durban to Pietermaritzburg – comprises 14 packages estimated to be in excess of R20 billion. Aimed at strengthening the logistics and transport corridor between South Africa’s main industrial hubs, Johannesburg and Durban, the project will also improve access to Durban’s export and import facilities and raise efficiency along the corridor.Dardanelles Interchange to Lynnfield Park Interchange
Work on the very first package of the project, the stretch between the Dardanelles Interchange and the Lynnfield Park Interchange, is continuing apace. The project entails upgrading of the existing four-lane dual carriageway to an eight-lane dual carriageway by widening to the median and outer shoulders over a 6.4 km distance, as well as the construction of associated bridges and interchanges. The massive scale of the project presents both opportunities and challenges for local aggregates producers. AfriSam’s Umlaas Road Quarry, located right at the doorstep of the current project, has seen a massive sales boom in the past two years. Kovid Singh, works manager: Umlaas Quarry, AfriSam, confirms that the operation more than doubled its pre-Covid volumes in 2021, maintaining the same volumes in 2022. Despite being located some 30 km away from the current project, AfriSam’s Pietermaritzburg Quarry – providing backup supply to Umlaas Road Quarry – has had a fair share of the project volumes, largely supplying sub-base material such as G2, G4 and G5. Consequently, the operation has enjoyed a welcome increase in sales over and above the base load normally supplied into the Pietermaritzburg market, confirms Ernest Sebeelo, works manager: Pietermaritzburg Quarry, AfriSam.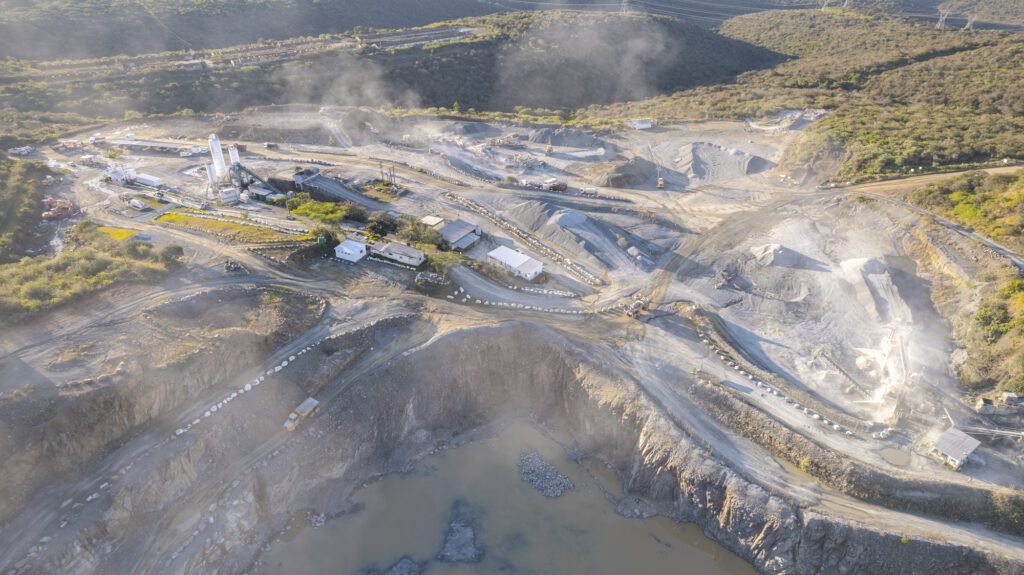
Responding to a surge in demand
However, supplying aggregates to a project of this magnitude is not without its challenges. From the onset, explains Theolan Govender, regional manager: Construction Materials KZN, AfriSam, production planning was a challenge due to the uncertainty related to the commencement of the projects and the associated volumes. “When we initially provided our tender proposals for the various road packages, we had to work on indicative production volumes and timing for supply. Once the volumes materialised, we had to progressively ramp up, thus changing strategy to balance production and maintenance,” Govender explains. AfriSam had to make use of its existing infrastructure within the group. To more than double capacity at its Umlaas operation, the company mobilised two existing trains of mobile crushers and screens to site, one from Johannesburg and the other from its KZN-based Verulam Quarry.The AfriSam Umlaas Quarry team had to strategically produce and maintain both the mobile and fixed plants, running extended shifts to meet supply demands. Plant availability, stresses Singh, is key to meeting the project’s aggregates requirements.
Given the nature of the mobile machines, AfriSam had equipped the mobiles with the necessary internal and external resources to cater for maintenance and the availability of the equipment. As a result, the team has managed to drastically improve the mobile plant’s availability, providing increased uptime and volumes.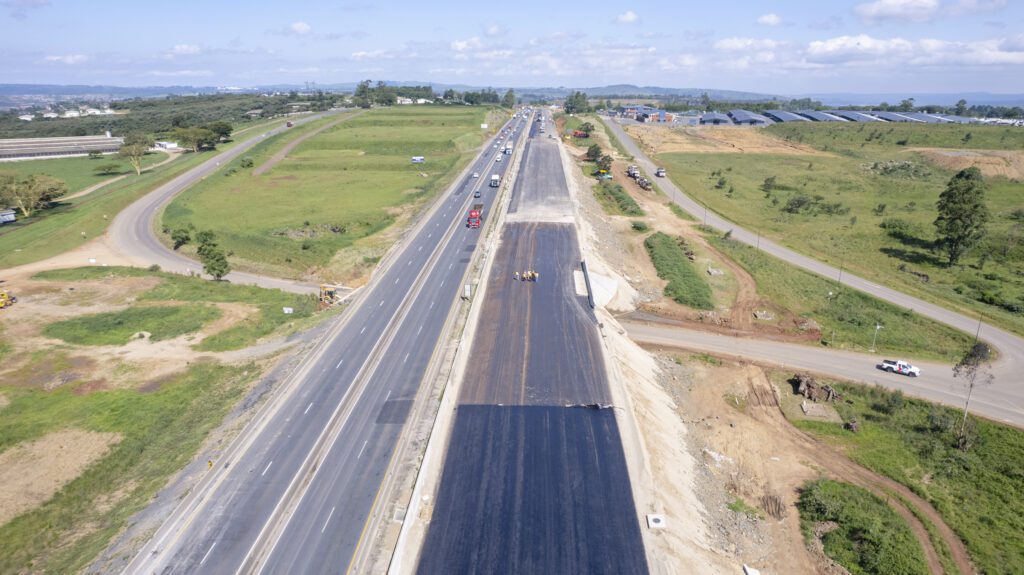
Mobile plants key to countering load-shedding impacts
Having a mobile plant on-site has not only helped boost production capacity, but also allows the team at the AfriSam Umlaas Quarry to keep producing during load-shedding, which is a challenge in Mkhambathini Local Municipality, says Singh. “Load-shedding is a big setback for us in this area,” says Singh. “We have between four and six hours of power blackouts per day, which puts us on the back foot in terms of production. To minimise downtime on our fixed plant, we now switch it off just before load-shedding to avoid crusher blockages. Bringing a mobile plant has also helped us minimise the impact of load-shedding on our ability to meet our project requirements.” AfriSam takes pride and care in producing quality aggregates to its customers timeously. “We have a laboratory on-site to ensure that we produce quality products within the required specification with the right consistency, which is key to the success of the road contractors,” says Govender.New Class 1 specification
Producing the new Class 1 specification products, says Sebeelo, has come with the challenge of setting the operational processes to produce at lower tonnages as opposed to the more common specification materials. However, the AfriSam Pietermaritzburg Quarry team has managed to effectively plan and change modes to optimise on uptime. Some of the new Class 1 spec products include the 7.1 mm concrete stone and the 5.1 mm unwashed sand, which are not easy to produce, explains Sebeelo.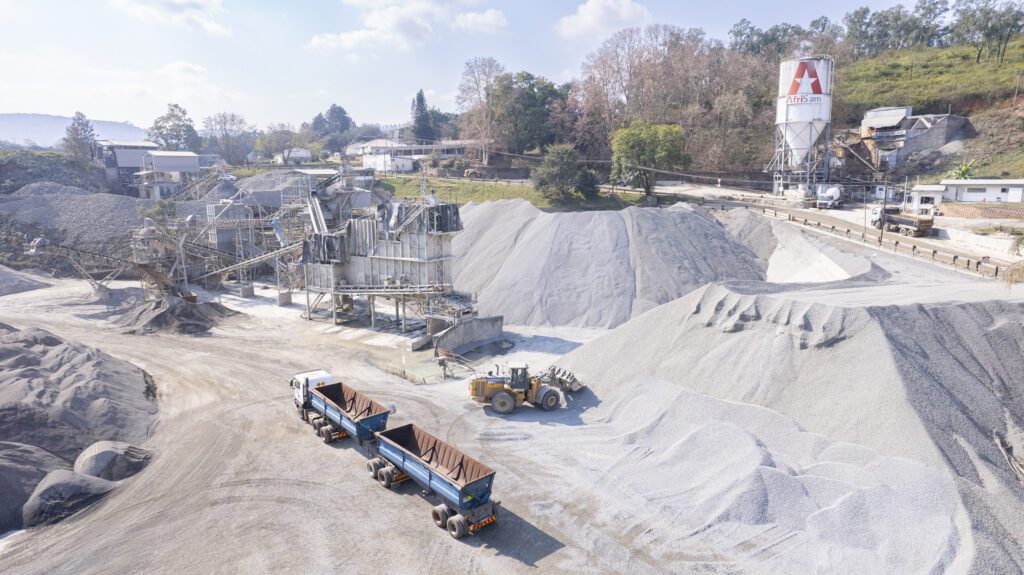