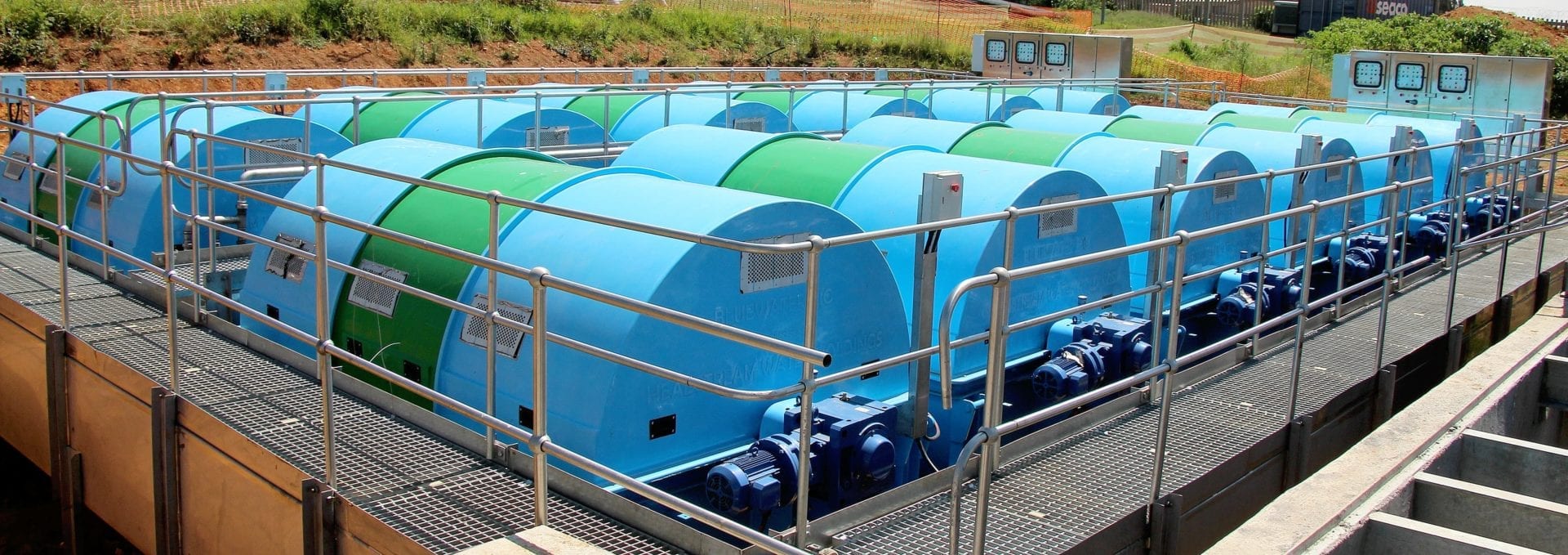
East Rand Water Care Company (ERWAT) is implementing new technologies at two of its plants that represent first-time applications for the group. Leading the way in Africa and South Africa, ERWAT is a visionary leader in the field of wastewater treatment and management. It continues to introduce new technologies that are passing on greater efficiencies for consumers in the industrial and residential markets across Gauteng’s East Rand region. A water reclamation feasibility study is also currently under way in conjunction with Ekurhuleni Metropolitan Municipality, ERWAT’s majority shareholder, to investigate the viability of supplying treated wastewater for industrial reuse, which will be dependent on the specific sector. Mining, industry and agriculture would be prime candidates. ERWAT is developing a short-term five-year infrastructure plan in order to incorporate all projects and then map the future of its plants in effectively addressing present backlogs. This dovetails with a longer-term regionalisation and 50-year master plan in conjunction with the City of Ekurhuleni. The integrated model will then form the basis for future expansion, with a key focus on maintenance and operational savings. “This could potentially result in the closure of smaller plants and the expansion of existing and larger facilities within the group,” says Emmanuel Khomela, acting executive manager: Development, ERWAT. “We also have a plan in place to install biogas-power-generation systems, which will make us more self-sufficient in terms of energy usage.” The current focus is on plant upgrades that are more efficient both in terms of engineering and energy savings across ERWAT’s 19 treatment facilities (which have a combined capacity of some 696 Mℓ of wastewater per day). They operate using conventional biological nutrient removal (BNR) technology to treat the wastewater received. The aim of the treatment is to reduce the contaminants in the wastewater to an acceptable quality prior to being discharged back into the water resources. “A key feature of BNR plants is their large-scale size in terms of concrete infrastructure, typically taking up the space of several soccer fields for bigger works. From inception, these plants were designed to be progressively upgraded with the building of addition modules that share the existing inlet and outlets works,” he explains. “Where plants are reaching their design capacity in terms of footprint, we need to find other ways to maximise their life, which means looking at retrofit options like the HYBACS (hybrid activated sludge process) technology we are installing at our Tsakane facility. This technology takes up a much smaller space and doubles the design capacity with minimal civil works.” An example of a recent large-scale conventional BNR upgrade is the project completed during 2016 at the Welgedacht plant, situated near Springs. Module 1, with a capacity of 35 Mℓ/day, was completed in 2003 and was struggling to keep pace with rapid urbanisation. Eventually, it was running at over-capacity and by 2008 the plant was already receiving 59 Mℓ/day against a design of 35 Mℓ/day. This necessitated a new Module 2 Extension of 50 Mℓ/day to cope with the increased demand for wastewater treatment from key areas that include Benoni, Boksburg, Springs, Bakerton and Daveyton. The new extension actually comprises two 25 Mℓ/day modules to improve efficiencies and maintenance. At 85 Mℓ/day, the plant is now running at full capacity. Further upgrade plans are in progress, which entail the addition of a
50 Mℓ/day module. The process technologies are already in place. Plus Welgedacht’s inlet works are designed to cope with
135 Mℓ/day.
Herbert Bickley and Tsakane
Currently, upgrades are in progress at the Tsakane operation (established circa 1973), serving the Duduza and Tsakane areas and falling within the DD5 drainage district. Tsakane is being equipped with the proprietary HYBACS solution from UK-based company, Bluewater Bio, which is supplied and supported locally by Headstream Water. This project commenced in March 2016, with targeted completion scheduled for April 2017. This HYBACS system will double the design capacity from 10.8 to 21 Mℓ/day. An optimal solution for upgrading existing activated sludge plants, Bluewater Bio states that HYBACS “can produce effluents with qualities that comply with the most stringent European nutrient-
removal standards”. “HYBACS is a standalone, compact and modularised plug-and-play technology, which allows us to retrofit an existing treatment facility and thereby significantly boost its capacity and lifespan,” explains Khomela. “Plus, the installation times are fast, typically taking less than 24 months to install compared to the much longer periods required for the construction of the heavy-duty civil works needed for new module extensions. HYBACS technology is also very energy-efficient.”
Plastic media
Alongside works at Tsakane, Herbert Bickley is the first biofilter plant within the ERWAT group to switch over from the age-old stone filtration system to plastic-media bio filtration within existing structures. Plastic media exhibit a much higher rate loading process rate and, again, there are energy savings. ERWAT’s plan is to convert other biofilter plants to plastic media in the near future. One of its major benefits is that it allows for more throughput of water inflows to the plant plus the surface area for filtration is larger. Phased installation times, which occur during the low rainfall season, typically take up to two years to complete, depending on the size of the treatment works. “Effective wastewater treatment and release is particularly critical given our present water-scarce environment. For engineering specialists and scientists in the field, this is a given, but for many there is no causal link or understanding, generally, about safe sanitation, effluent treatment, and subsequent ecosystem replenishment. These areas need constant consumer education, which starts in the first instance with responsible disposal into our sewer systems, an industrial example being heavy metals and bad chemicals, which impact on downstream process costs since more intensive chlorination treatment is required. “Our number one mandate is service delivery, which is why we’re investing in advanced technology to maintain the water quality of the receiving water resources and to help protect South Africa’s water security,” Khomela adds. ERWAT is geared to collaborate with the mining sector, the food and beverage industry and other private sector customers in operating and maintaining their wastewater treatment plants.