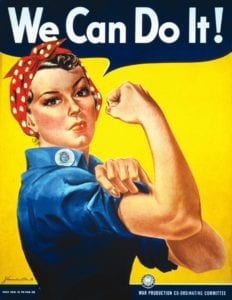
BubbleLock is a proprietary South African technology, developed by Sally Hall (nee Hyson) in the 1980s
Submitted by Hyson Cells
After about thirty years the concrete structures that we assumed as being unbreakable suddenly disintegrate and collapse as a result of corrosion of the reinforcing steel. We have solutions for this problem that can be applied to water storage structures, to canals, and to roads with crawler lanes and side drains combined. We present an opportunity to move away from reinforced concrete with its high cost and specialised personnel to a more cost effective solution utilising cast in-situ articulated block mats and pavers that do not need reinforcing steel.Why they reinforce concrete
Concrete is often reinforced with steel. A steel supporting framework is made by joining steel bars (rebar) and this is then usually surrounded by shuttering. Concrete is poured into the shuttering, where it fills the gaps in the steel support. It is poker vibrated and sets hard. The work is very skilled and the shuttering and rebar are expensive. Huge problems arise if rain stops the pour and a joint must be cut and filled with expansion jointing material. Reinforced concrete is an example of a composite material. This composite material is a better construction material than concrete alone because:- concrete is hard and strong under compression, but weak when stretched under tension
- steel is flexible and strong under tension
Corrosion – “Sick Concrete Syndrome”
Corrosion of the steel rebar causes it to swell as rust is formed. Rust has a lower density than metal, so it expands as it forms creating tensile stresses. This tensile stress leads to cracking, spalling and potential failure of structures. There are two types of steel reinforcement corrosion:- Chloride-induced – for example, from acid mine drainage and wastewater
- Carbonation – induced by exposure to air and salt water and mist
Some disadvantages of reinforced concrete
There are two main disadvantages:- Cost of materials
- Time to construct, which also translates to higher expenses on site
Cost of materials
There is a lot of steel in a RCC water tank. A tank only 5m high will have a base of 8mm rebar spaced at 180mm centre to centre, the lower reinforcing hoops will be 12 mm at 150 c/c and the upper hoops 12mm at 300 c/c. That quantity of rebar makes the tank expensive. And if the hoops become exposed and begin corroding the whole structure is likely to burst. Many engineers design in micro cracking in round structures to prevent larger contraction and expansion cracking.Cost and time to construct
We have seen that a high quality of concrete is needed for RCC. The main steps of using reinforced concrete are mixing, casting, and curing. All of this affects the final strength. A problem is that stone and “free “ crusher dust are added to cheapen the mix but this makes the mix “sticky” and causes it not to flow and hinders workability. So water is sometimes added on site to improve the flow characteristics. But excess water weakens the concrete and the stone can begin to settle out. It takes 28 days for ordinary Portland cement (OPC) to cure and 56 days if fly ash is added. The strength of the concrete can only be determined by taking cores and by then it is too late. Consequently the taking of cores is too often neglected and the weak concrete is only detected when the bridge collapses. Poor quality concrete with a high porosity can lead to early corrosion. This can be noticed in down town motor way where the upper deck is leaking calcification and brown rust down the columns The cost of the forms used for casting is relatively higher. Erection of the embedded steelwork is a skilled and therefore expensive process. Curing shrinkage causes crack development. Cracks can enable the reinforcing steel to begin a corrosion process – especially in harsh environments such as a water treatment (WWT) plant and Acid Mine Drainage (AMD) works Concrete must be of very high quality and must not be porous because of the danger of corrosion. The daily expansion and contraction of concrete can open up the pores and allow the penetration of air and especially water containing chlorides such as seawater and WWT and AMD plant effluents.Hyson Cells BubbleLock – An alternative to RCC slabs
Hyson Cells cast in-situ pavers present an alternative to RCC construction for industrial paving, drain and canal liners and dam liners. This system has no steel and uses a pumpable self-levelling sand groutHyson Cells BubbleLock
Hyson Cells BubbleLock will be seen in the Bill of Materials as a “geocell” but it is really quite a different product to conventional geocells. Geocells originated in 1979 where the US Army Corp of Engineers did research in reinforcing sandy beaches to allow them to be trafficked by wheeled vehicles. They arrived at a honeycomb-like structure that lent strength to the sand by confinement and suggested that the honeycomb could be made of plastic. In the USA this led to the development of a product known as Geoweb made by ultra-sonically joining of 2mm thick plastic sheeting. This material and technology made the product expensive. Its robustness also made it cumbersome to install. The SADF was at that time fighting in Angola and approached the South African plastics industry to see if they could develop a product that the US Army had envisaged. Companies such as Metal Box each came up with other suggestions of plastic vending cups, but Sally Hall (née Hyson) developed her own manufacturing method and Hyson Cells was born. Research showed that it was the geometry of the confinement that lent the strength more than the hoop strength of the cells and Hyson Cells introduced their own product that used only 200 micron film instead of the 2mm thick sheeting that has used by Presto Geoweb in the USA. This had the added benefit that it made the product affordable. Each of the two companies, working at opposite ends of the earth, independently came up with the idea of incorporating a tendon and patented the idea in their countries. (Hyson actually pre-dated Presto but when this fact was discovered we lacked the funding to challenge their patent on the grounds of prior art – but our South African patent prevented Presto from introducing Geoweb to South Africa). Originally intended as an inexpensive road-making system geocells are now used worldwide with granular material for erosion control, soil stabilisation on steep slopes, channel protection, and structural reinforcement for load support and earth retention. Geocells reinforce granular material by confining it whereas Hyson Cells concentrated on applications using a Pumpable grout infill. Hyson Cells supplies mats in plus-200 m² packs. These large packs allow for more area covered and if pre-cut to the site they do not normally fit into the earth works. It is used as sacrificial formwork to cast articulated block paving with the formwork being left embedded in the paving to serve as perfectly fitted jointing. The Hyson product has evolved by incorporating an approximately hemispherical dimple in each face of the cast concrete block. The hemispherical “bubble” suggested the trade name of BubbleLock. This gives a rounded keyway joint that improves the 3D mechanical interlock that has been found to improve load transfer to neighbouring blocks by up to 10 times as compared to the plane-walled cells. The patented laced tendons (which we term “rigging”) are critical in supporting the lightweight cell matrix for filling with “concrete” (we prefer a sand-cement grout with no coarse aggregate). They are also used to help peg the formwork mat snugly onto the supporting surface and prevent the formwork from “floating” on a pool of grout that will set as an unjointed slab. We also use a high slump mix which we advise achieving by use of a super plasticiser supplier in each bag of Hyson Cells to better control shrinkage as the grout sets.Load bearing and load transfer
Prof A.T. Visser has done eight papers on Hyson Cells and won the Princess Ann award for best paper and the Best paper of the millinium in Tokyo. Research has always been top of our agenda and new ideas all are progressing at one time The Hyson Cells rounded keyway joint exhibits a 3D lockup mechanism. This lockup provides shear transfer for wheel loads moving across joints and load transfer to prevent differential faulting of adjacent cast blocks. The interlock therefore gives:- Load distribution
- Cast mat and pavement flexibility
- Shear strength
Controlled cracking
All concrete cracks – the most common cause being loss of excess water during drying known as drying shrinkage. Even with very fluid concrete this cracking is unlikely to exceed 500 micro strain (parts per million). With an unjointed concrete slab this degree of cracking would amount to about 1.5 mm cracks every 3m or so. With a cast Hyson Cells block of side 150mm the drying shrinkage amounts to less than 75 micron – a human hair is 10 microns. So the Hyson Cells cast-in-situ paving has “controlled cracking” less than a human hair in width every 150mm in both X and Y directions. This is truly “micro” width and allows for capillary action that allows for the release of hydrostatic pressure of trapped water and air but traps any fines and does not allow fines to be transported from beneath the paving.Hence, Hyson canal linings can be seen to weep when the water table rises and increases pore pressure but are still rated as comparable to conventional canals with panels and rubber jointing with respect to water proofing. This only works with ultra-smooth plastic walls and not woven or ribbed plastic walls
Conventional geocells do not work the same as Hyson Cells when filled with concrete. With Hyson we take particular care that discrete blocks are cast so that the shrinkage cracks are evenly distributed by each block. Woven and non-woven geocells will get saturated by the cement paste as they are wet-table and used for drainage applications. The cement paste will therefore bond the individual blocks together to form a bonded mass that will crack in a wide crack at its weakest point and allow the ingress of water and consequent pumping of fines through the crack. Geocells made from 2mm thick HDPE or other compounds are stiff and will tend to bridge surface depressions allowing the formation of a pool of concrete below the geocell mat structure. Geocells such as Geoweb and Neoweb are seen to now incorporate drainage holes in the cell walls. This will again encourage the blocks to bond with each other and limit the flexibility of the cast articulated structure these bonded “rods” shear and cause failure with high loads.Waterproofing
Hyson Cells linings are approved by the Department of Water and Sanitation (DWS) for use for irrigation canal linings. Water only penetrates the articulated liner under high pressure such as hydrostatic pressure or excess pore pressures. Should no seepage at all be allowable, e.g. when lining a toxic pond or landfill, then Hyson Cells can be installed as pumpable grout armouring to an impermeable liner such as a geomembrane. This method causes the wall to be less steep than would be with the Hyson Cells Double Liner See separate section for the Hyson Cells 100% waterproof bitumen “double liner” which is trafficable for cleaning and is the subject of international patents. This allows for a smaller foot print higher movement of sub layers and still be cleaned with heavy equipment if the pumpable grout is over 20MPa on the top layerRelease of hydrostatic pressure
Water and air may be trapped beneath a cast concrete slab and conventional empty concrete canals or swimming pools may rupture when the water table rises. Empty Hyson Cells canal liners in irrigated lands are however observed to weep back into the canal as they release these pressures through the jointing by capillary action. Excess pore pressure, generated by the applied surcharge to Hyson Cells paving, can be sufficiently high to be relieved by upward dissipation through the cell joints.Maintenance
The maintenance cost of reinforced concrete is lower than plain concrete but very expensive to remove to replace if it does get sick concrete syndrome and has to be cut out with diamond or tungsten blades and jack hammers. Maintenance of our paving is quick, easy and inexpensive. The area to be repaired is excavated with a pick and there is no obstructing steel. A replacement patch of the formwork is pinned in position and filled with poured grout. If a quick set is required calcium chloride can be used as an additive.Especially suitable applications
Industrial paving:- where wheel loading is ultra-heavy 200 tons axels and wheel slewing and turning is frequent
- where heavy static point loads are expected Container yards
- where soil pore pressures are high
- where oil or chemical spills can be expected
- That must be waterproof and must be periodically cleaned of silts.
- where water tables fluctuate due to irrigation
- where labour-based construction is intended
- or high speed 1st world r/mix trucks and pumps
- Where the project is expected to employ the unskilled
- That can be excavated and reinstated using hand tools to lay extra services
The Hyson Cells application case studies
Industrial paving
Santa Clara installation
Santa Clara is a huge container depot on the Namibia Angola border with 350 000 m² of paving for truck parking. The ground conditions are very sandy and the consultant realised that asphalt paving would not survive. He consulted with Professor A T Visser of the University of Pretoria who recommended Hyson Cells 150mm deep constructed on a dump rock foundation. The contractor was the first to use pumped concrete on a grand scale and achieved 6000 m² a day then reduced to 3000 m² per day production due to factory constraints.Storm-water drains
Large Stormwater drains are our most frequent business especially for remote areas. The local river sand can frequently be used for the grout fill which cuts costs dramatically and the lightweight nature of the Hyson Cells formwork cuts down on freight costs. 75 kg for 200 m² The formwork determines the thickness of the liner and controls costs. Due to the ability of the liner to “breathe” high velocities of up to 18 metres per sec have been handled for the past twenty or so years with no need to maintain them (e.g. Daggafontein tailings dam)Canals
Unless extra precautionary measures are introduced to include under drainage for conventional canal lining, hydraulic pressures from ground water (from below or lateral) will cause damage to the lined concrete construction panels as a result of their movement. These measures require extra time and materials adding to the overall construction costs including jointing materials and dowels. Rounded 600 mm radius between floors and walls allow for better flow than normal trapezoidal designsPongola canal constructed by DWAF
Hyson Cells used in Pongola proved that this alternative construction method can successfully be employed under all circumstances, but especially under wet conditions and to withstand unforeseen flooding. The Republic of South Africa’s Department of Water Affairs and Forestry’s Directorate Civil Design approved during 1995 that Hyson Cells can on an experimental basis be used as supportive construction material for the lining of earth wall canals, water conveying as well as drainage, under extreme clay soil conditions, on the Pongola Irrigation Scheme, Pongola, Kwa Zulu-Natal, Republic of South Africa. During 1995 a section of the Transvaal canal, main feeder of the left bank irrigation as well as domestic supply to Pongola Town Council was used to test Hyson Cells as alternative to conventional concrete canal lining panels. At the same time, permission was granted to line a two-kilometre drainage canal at the airfield to solve serious overland flooding problems during rainstorms of the past This was no fines concrete to drain the sugar cane fields, the reeds took over and were cleared with balls of barb wire then WAF coated the non-fines to stop the reeds but still allow the water to drain into the canal. Apart from draining water logged irrigated sugar fields identified by the Department of Agriculture, drains were also constructed to serve as points of discharge on the canal systems to protect betterment works as well as that demanded by the damages caused during the tropical storm Demoina. Inspected in 2005, by Mr H. Bosman, (retired Direct of Water Affairs) after ten years, (Pongola Irrigation confirm still ok in 2017 — i.e. after 22 years ).- no movement of the canal was observed (S27º25’30.6″; E31º36’30.1″;
296m MSL). - no cracks developed along the polyethylene matrix walls (Hyson Cells).
- the canal surface showed no weathering and appeared smooth as the day of construction
Labour intensive rehabilitation of 35km canal in Groblersdal
The main contractor was Group Five Construction. Group Five undertook the following tasks themselves- Earthworks –Excavation -Survey pegs for finished levels of canal lining
- Cement -River-sand -Water tank (moved and filled daily)-Hyson Cells packs from store
The Hyson Cells 100% waterproof “double liner”
Pollution control dams
Based on experience with canals Hyson Cells can be used to construct dam liners that are reasonably waterproof. However there are occasions where 100% waterproofing is required. A standard solution is to use a geomembrane plastic liner and protect it by armouring it with concrete in Hyson Cells. This is a difficult and slow task as the concrete wants to slip down the slopes when wet and we have found that we need to use stronger rigging. A better solution is to use a 4mm layer of bitumen sandwiched between two 75mm layers of concrete filled Hyson Cells. References are:- 570,000 m³ off channel storage dam and five smaller dams of 11 000 m³ to 28 000 m³ for the Lebalelo Water Scheme designed by SRK and constructed in 2001 and now owned by DWA
- If going to be trafficked with 5 cu m FEL and 32 ton Bell trucks the top layer must be 20 Mpa not 5Mpa
- Relocation of Raw & Potable Water Reservoirs for Phalaborwa Mining Company designed by Knight Piesold
- Pollution control dams for the platinum mines designed by SRK
- the walls can be as steep as 1:1 and this reduces the land use footprint and also the lined area
- the dams can be trafficked by machinery for scraping silts