AfriSam’s just-in-time readymix solutions are helping to accelerate delivery on a range of single- and multistorey residential projects.
On the frontline of supplying quality, affordable housing to South Africa’s growing urban population, construction materials leader AfriSam is working closely with Raubex Building on a new Valumax development in the Clayville Ext 45, Tembisa, area in Midrand, Gauteng. The substantial development comprises bonded properties for private sale, plus government-funded RDP flats built in blocks of different sizes. A member of the JSE-listed Raubex Group, Raubex Building – formed in 2012 by Barend Badenhorst, Gert van der Werff and Werner Muller – started life as Raubex Housing. After expanding beyond housing into commercial developments, the company changed its name to Raubex Building in early 2016. “We have been working with AfriSam since at least 2013, and have always been impressed by the reliability of service and quality of product,” says Renier Rossouw, quantity surveyor, Raubex Building. “Our projects are always constrained by budget and time, so we need partners that deliver on their promises, so that we can deliver on ours.”
Private sales
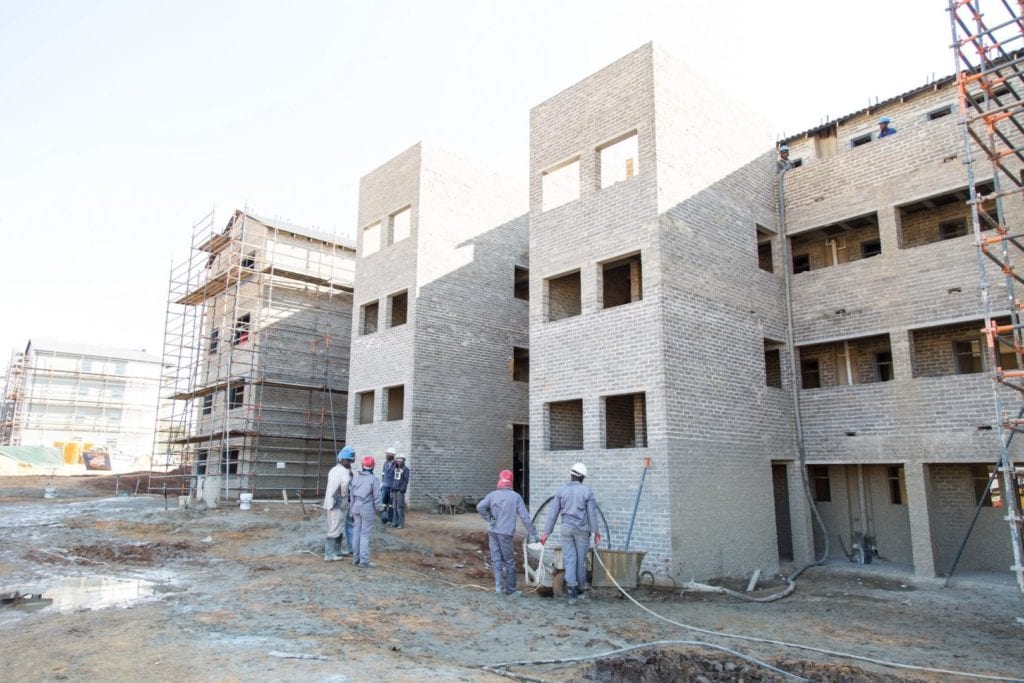
AfriSam supplied concrete for the 11 blocks as part of Phase 1 of the RDP flats
On the residential units for private sale at the Clayville development, work has been ongoing since the beginning of 2015, with 822 houses constructed by June 2017. The designs detail three size configurations of 45 m
2, 52 m
2 or 56 m
2 each. The main demand for readymix on this project was for the raft foundations, with each house taking between 8 m
3 and 9 m
3 of 20 MPa concrete – depending on the size of the house. With four foundations being poured daily, AfriSam was delivering about 36 m
3/day, according to Adele Wentzel, sales
manager, AfriSam. “We delivered a total of some 7 000 m
3 of readymix from our Olifantsfontein plant, which is only about 11 km from site,” says Wentzel. “This allowed us to keep costs to the customer at a minimum while meeting delivery deadlines. Our extensive footprint in the region allows us to coordinate alternative supply from another plant, if the need arises.”
First phase of RDP flats
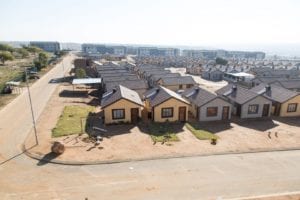
The new Valumax development in Clayville-Thembisa consists of both bonded properties for sale and government-funded RDP flats
Not far up the slope from these houses are the first and second phases of a government-funded project to provide RDP flats for residents. According to Rossouw, the first phase started in January 2016 and was handed over to the client in February 2017. This comprised 11 three-storey blocks making up a total of 237 flats, each with an approximately 40 m
2 floor area accommodating two bedrooms, a bathroom and an open-plan kitchen. Raft foundations for this phase required AfriSam to supply about 1 100 m
3 of 20 MPa readymix concrete, while the rib and block slabs between the levels of the flats used about
500 m
3 of the stronger, 25 MPa concrete. On the ground floor, the concrete was manually power-floated to obtain a smooth finish, while a 15 mm to 20 mm screed was put down on the upper floors to get the required finish on the rib and block slabs.
Second phase
Just 700 m down the road is the second phase of the RDP housing project, which will run until March 2018. Initially, Raubex was contracted to tackle 264 living units – a contract that was then expanded to 484 units. This time, the contract called for four-storey blocks, and a total of 18 will be built. The units in these blocks are also 40 m
2 in size, and there are 20, 28, 32 or 36 units in each different-shaped block. About 1 800 m
3 of 20 MPa readymix concrete will be delivered by AfriSam for the raft foundations by the end of this phase, as well as another 1 200 m
3 for the rib and block slabs between levels.
Secure supply
“Contracts like these demand a reliable supply of readymix, as our work is highly structured and planned in detail,” says Rossouw. “AfriSam’s capacity is, therefore, important to us. If anything affects its production at one plant, it can ensure we get what we need from another of its operations.” He says it is also vital that the concrete is compliant with a range of quality requirements, as each pour must be tested and sent to independent laboratories – as part of company policy and contract requirements. Wentzel says AfriSam’s depth of expertise in cement and concrete technology allows the company to offer support to customers regarding testing and quality issues. “If requested, we can even offer skills training to customers’ employees on the processes for testing on-site and the various procedures to be followed,” she says. “AfriSam also conducts tests on-site for pours of over 50 m
3 if the customer requires it.” She also highlights the importance of good systems and constant communication on both sides of this partnership, ensuring that each party knows what to expect, and when. Rossouw says Raubex Building appreciates the quick response from AfriSam’s control centre, which provides monitoring of all readymix trucks and operations so that any queries from customers can be answered efficiently and the required action taken.
Concrete innovation
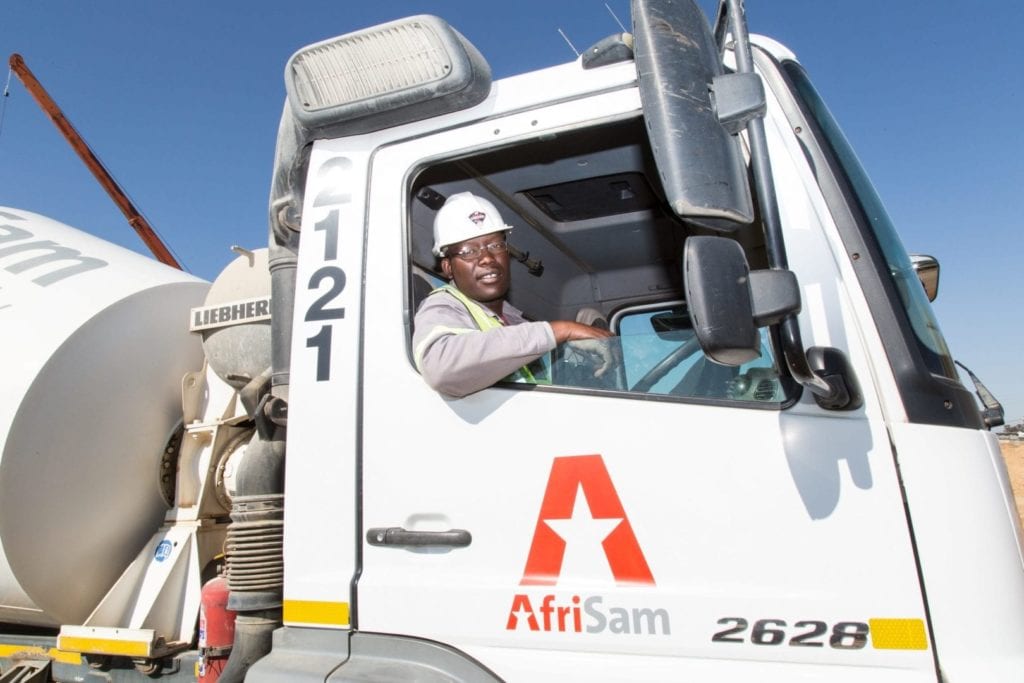
The adoption of the waffle raft foundation design on this project has been an important innovation to leverage the versatility of concrete, while also enhancing the job creation capacity of the work. Developed by civil engineer Terry Pidgeon, this design provides load-bearing capacity in the foundation, even where the soils are expansive, rocky or hydro-collapsible. The foundation is created by excavating a series of pod forms to create a grid of ribs. A continuous concrete pour creates concrete beams running throughout the footprint and perimeter of the foundation (with voids between) in one operation. The completed slab then sits on the ground, bearing on the ribs created between the forms, while the void areas underneath the slab allow for soil movement. Strengthened with reinforcing bar, the waffle slab foundation is very stiff and can resist the impact of ground swelling due to surface drainage or flooding from any source.
Skills for growth
There are about 260 workers on-site during this phase of the project – mostly locals who are engaged and trained by Raubex Building. “Our construction method is deliberately labour intensive to allow a high level of job creation and skills development,” says Rossouw. “Once delivered by the AfriSam readymix trucks, the concrete for the raft foundations is moved mainly with the use of wheelbarrows; for the same reason, the smooth surface is obtained with a manually operated power-float.” He says the company believes in employing local labour, wherever possible, to ensure the spreading of economic benefits and skills to the local area. These workers are trained by Raubex Building’s core team, which makes up only about 20% of the staff on-site at any given project. “We also engage subcontractors from the local area, mainly to handle the electrical installations in each residential unit, as well as the plumbing, glazing and ceilings,” he says. Skills are developed through the Raubex philosophy of ‘Bafana Teams’, where Raubex staff help locally based employees to work effectively together in teams, building their own skills while ensuring that project targets are met.