The use of membrane technology for water treatment is beginning to pick up in the Southern African region. WASA speaks to Henk Smit, managing director, Vovani Water Products, about the options available to the local market.
There are various membrane technologies available for water and wastewater treatment, ranging from microfiltration through to reverse osmosis. Worldwide, these technologies have become readily available and easy to implement, says Smit. Locally, there has been a big uptake in reverse osmosis as Cape Town has moved to implement three temporary desalination plants to address the drought crisis; but the applications for membrane technology are far broader than this. “From surface water to wastewater and mine water, there is no water that can’t be treated with membranes,” he says.Membrane technologies
Membranes are manufactured from polymers or thin film composites to perform a specific function. There are four main membrane technologies:- Microfiltration (MF): This is largely used for the removal of microorganisms, commonly in the food and beverage industry.
- Ultrafiltration (UF): In addition to removing suspended solids and microorganisms, UF also removes certain viruses down to 0.01 µm.
- Nanofiltration (NF): Referred to as a softening membrane, NF removes monovalent ions from about 50% to 90% and is good for process technologies, particularly in the dairy market.
- Reverse osmosis (RO): This removes up to 90% of monovalent ions in brackish water and seawater applications.
Benefits
One of the biggest advantages of membranes is their ability to provide consistent output quality, regardless of feedwater quality. “South Africa’s treatment plants often experience fluctuations in the quality of the feedwater, which can create problems in traditional treatment plants where treatment needs to be adjusted accordingly. Membranes will always provide a consistent output based on their design,” explains Smit. He believes membrane technologies lend themselves to the South African environment, where space, costs and skills are becoming increasingly inhibitory. Conventional treatment plants require more civil works, a larger footprint, and more manpower and technical skills to operate. Membrane technologies can be built into small buildings or even containerised mobile systems. They can be assembled off-site and installed at a much faster rate than traditional plants. Membrane plants are also becoming increasingly automated and, therefore, require fewer operators and less technical skills, as the plants largely run themselves and mainly require only monitoring and oversight. “South Africa is facing a skills shortage and membrane technologies essentially replace these skills. This is leading to a bigger move towards membrane technologies in the region,” says Smit. “Importantly, many of these systems can now be monitored and run off-site at the operator’s premises and even remotely via a smartphone or tablet. You can start or stop a pump, or even start up the entire plant remotely without anyone doing anything at the plant itself.” The ability to build membrane treatment systems into containerised, remotely operated systems also lends itself to decentralised solutions needed for South Africa’s rural settings. Vovani supplies a UF gravity-fed system that requires no electricity, as well as a UF system that can operate via solar power. Removing solids down to 0.04 µm, these off-grid systems are ideal for providing clean drinking water to small, rural communities.
Pre-screening and treatment
One of the best ways to improve the lifespan of your membranes is with good screenings and prefiltration. “Membranes can be very sensitive, so you do need to pre-screen to 100 µm and pretreat to protect your membranes. You have to look at the whole application to determine whether you need self-cleaning strainers or sand filters, or potentially UF and MF,” says Smit.Vovani supplies UF membranes that remove all suspended solids from feedwater and serve as prefiltration to RO membranes, to protect and increase membrane lifespan. These UF membranes, supplied by SUEZ Water Technologies and Solutions, are also used for surface water, wastewater and water reuse filtration.
The company also represents Muhr, which manufactures screening systems used for desalination and wastewater treatment plants. These systems are imperative to remove seagrass, seaweed, shells and other large solids from the desalination plant’s feed stream that can damage any of the upstream filtration processes. Energy and cost savings Membrane technologies can be energy intensive, particularly when it comes to RO treatment of brackish water and seawater. However, technologies are available to drive down energy use, as Vovani has demonstrated at Cape Town’s desalination plants. Vovani has been involved in all three of Cape Town’s emergency desalination plants, supplying flexible pipe couplings, high-pressure pumps, energy-recovery devices, FRP pressure vessels, and RO membranes to the plants at the V&A Waterfront, Strandfontein and Monwabisi. Vovani supplies Fedco high-pressure pumps for desalination projects, as well as various Fedco energy-recovery devices. These devices can be used in areas where water flow and pressure can be utilised for saving on power consumption, or turned into electricity. By using these high-pressure boosters, along with low-pressure hydraulic energy management integration and low-pressure drive conversion of brine hydraulic energy into electricity systems, energy demands can be reduced, explains Smit.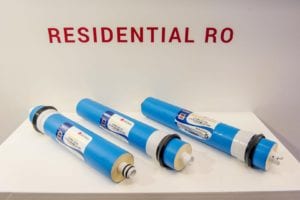