Regional Manager of Victaulic South Africa, Marcel Ley explains how the technology of mechanical pipe joining solutions is enabling the water industry
The first quarter of 2020 has not only highlighted the importance of good hygiene, but it has also reinforced the message that societies are unable to maintain their health and safety without an uninterrupted supply of clean water. The simple instruction: wash your hands, reminds us how easy it is to take the necessary precautions. But this is easier said than done in many severely water deprived communities. Ongoing shortages as a result of drought, insufficient and ageing infrastructure and a lack of proper maintenance in South Africa and Africa, has made the simple task of washing hands a challenge. A Lesson in Water Management In January 2018, Cape Town officials announced that the city of 4 million people was only three months away from running out of municipal water. The country, and the watching world, were dumbfounded. Swiftly described as “Day Zero” and brought on by three consecutive years of lackluster rainfall, April 12, 2018, was to be the date of the largest drought-induced municipal water failure in modern history. In order to dodge this bullet, the city undertook a smart combination of technical fixes, regulatory controls and an aggressive province-wide awareness campaign. By the end of March 2018, these massive efforts provided a small additional buffer in the city’s water reserves, allowing city officials to push back Day Zero beyond the upcoming rainy season. In June 2018, the region saw average rainfall for the first time in four years. With the rain, dam levels rose, and officials were able to call off Day Zero indefinitely. What Can We Do Differently? As a predominantly semi-arid country, South Africa boasts approximately 2500kms of coastline. A wide expanse of glistening ocean that shouts out a solution to the ongoing water crisis – desalination. Santa Barbara, California, provides a solid proof point for the transformative capability of desalination.In 2015, California was in the throes of a devastating four-year drought when the decision was taken to reactivate the long-dormant Charles E. Meyer Desalination Facility, situated in Santa Barbara.
One of the first issues the city officials encountered when they kicked off the reactivation was a section of missing pipe. Eight feet of a 36-inch subsea intake line had been removed when the plant was placed in standby mode. Before the plant could be brought back online, the intake pipe needed to be repaired. Initially, engineers considered running an unrestrained coupling which would require anchoring the coupling to the ocean floor to restrain the pulling forces created by the 80 PSI underwater pumps.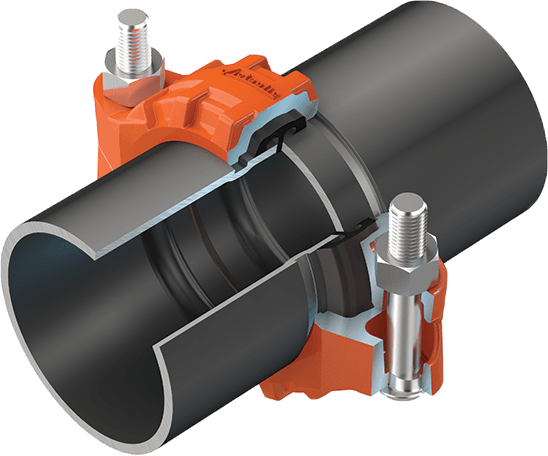
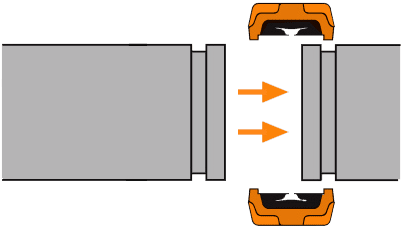
Latest News Stories