Constructed in the mid-1960s as a pump station, with the addition of biofilters in the 1970s and biological processes in the 1990s, Darvill’s wastewater treatment works (WWTW)has always been an engineering feat. The fourth upgrade is nearly complete and has continued the tradition of embracing innovation.
By Kirsten Kelly The Darvill WWTW is owned and operated by Umgeni Water and serves the Msunduzi Municipality, receiving and treating both domestic and industrial wastewater from the city of Pietermaritzburg in KwaZulu-Natal. Its original design capacity was 65 Mℓ/day, and has been upgraded to treat 100 Mℓ/day, with plans for a further 20 Mℓ/day extension in future.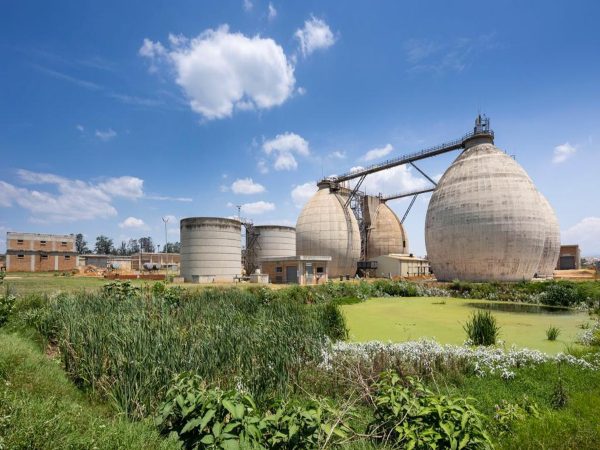
- Methane generated by the anaerobic digesters (currently as boiler fuel) may be directed to a gas-to-electricity cogeneration plant. The project is at feasibility stage.
- A 2 Mℓ/day direct reuse plant that is in the final stages of commission.
Water reuse demonstration plant
Additionally, a new 2 Mℓ/day water reuse demonstration plant was designed, which will treat the final effluent to potable standards. The plant incorporates several advanced technologies – such as advanced oxidation and biologically activated filters and ultrafiltration membranes – thereby providing multiple barriers against contaminants of emerging concern such as nanomaterials, pharmaceuticals and endocrine-disruptor breakthrough. Initially, it will be used as process water and will provide opportunities for further research into complexity, efficiency, life-cycle costs and adaptability of water reuse in the South African context. It will be a valuable example of reclamation in practice to stakeholders. Bubble diffused aeration system The biological treatment system has been changed from a modified Johannesburg system to a 3 stage Phoredox biological nutrient removal system. This treatment process has been optimised by adding a bubble diffused aeration system that is more energy efficient than surface aerators. The fine-bubble diffused aeration system supplies oxygen to the metabolising microorganisms. “The seven-metre-deep aerobic reactor is used (owing to space constraints) which has resulted in an increase in the oxygen transfer efficiency for the treatment process. This system allows for smaller air bubbles to be introduced into the reactor, creating a larger surface area for the mass transfer of oxygen into liquid. This reduces power use while increasing efficiency,” says Schalkwyk. Challenges One of the main challenges with this upgrade was phasing in and out of unit processes and deciding what to decommission first. The plant was already under strain due to capacity issues so this meant reduced capacity in that period. “At times, we had to make decisions to forgo compliance for a while, in order to allow the contractor to shutdown existing infrastructure, while at the same time the inherent challenges of operating Darvill continued, such as Trade effluent illegal discharges and unreliable power supply,” says Mulalo Murigwathoho, Systems Manager. The rainy season was worse, as it meant delays on constructions, guaranteed process failures, and complaints from the Canoeing community. A number of directives were issued during the course of the upgrade, because of some of these failures. Later on, the main Contractor abandoned the contract and work stopped for approximately two years while processes to appoint another contractor where in progress. That caused the Employer to take on operation and maintenance of incomplete processes and operations, and remaining with infrastructure that no longer had warranty and guarantees. Some of these equipment has never performed and UW had to take on the risk to rehabilitate later on. The project suffered a significant setback when the main contractor filed for business rescue. “In order to ensure work continuity, Umgeni Water applied for consent from National Treasury to negotiate with sub-contractors on the project to complete the remaining works. Consent was granted and was later partially implemented in favour of competitive bidders to control costs for the new main contractor. The new main contractor resumed construction work in August 2020and is expected to complete by end of October 2022.” states Lindelani Sibiya. Covid-19 was another challenge that caused delays and financially impacted smaller subcontractors, making it difficult for them to complete work. There were additional challenges faced by the project due to complexities on the designs, integration of the old and the new units, adverse climatic conditions and their implications on the ground to mention but a few. “Despite these challenges, Umgeni Water is extremely proud of this project. It is proof of our commitment to our environmental sustainability policy that aligns with circular economy principles. This project also affirmed Umgeni Water’s strength and resiliency in bulk water infrastructure development. It also changed many lives for the better. Small, medium and micro enterprises were also contracted to perform on the project. The contractors tried to use as much local labour as possible and empowered them with new skills and experience. A number of graduates were trained through this project as well,” concludes Sibiya.