Standing among South Africa’s leading pump OEMs, APE Pumps and Mather+Platt have built a reputation for excellence based on product innovation spearheaded by dynamic people.
IMIESA speaks to John Montgomery, GM for APE Pumps and Mather+Platt, who introduces an up-and-coming mechanical engineer, Thorne Zurfluh, as a key member of the team. APE Pumps is 71 years old in 2023, while Mather+Platt is much older, tracing its roots back to the First Industrial Revolution from the mid-18th century, where from the dawn of industrialisation pumps have been and remain the critical interface for every aspect of fluid transfer. Both OEM bands cater for fit-for-purpose applications in key sectors that include water and wastewater, firefighting, energy, mining, agriculture and the petrochemical sector. Over the years, APE Pumps and Mather+Platt (the group) have ensured their success through succession planning, market diversification and investment in specialist technologies to support business growth. (Both sister entities form part of the multinational WPIL Limited groupof companies.) Montgomery started his career with these two leading brands some 19 years ago as a qualified draftsman. Over the years, he has been exposed to every facet of the business – from design to production, stripping and assembly, and installation. It’s a complex field. “Clearly, no pump engineer, specialist technician or artisan is born overnight. The baseline skills are essential, but the experiential, applied learning is what defines master craftsmen, engineers and project managers in all our interrelated disciplines. That’s why our business is dedicated to attracting and mentoring the best talent available, which is why we brought Thorne on board in June 2022 to be trained as one of our next-generation leaders. We like a two-way mentorship approach, where the ‘old’ teach the ‘young’ and vice versa, in modern versus tried and tested techniques,” explains Montgomery.
Evolving engineering focus
Currently studying his MBA at Wits Business School, Zurfluh joins the group at a time of unprecedented growth in production demand, as well as parallel expansion into key services that include customer service-level agreements (SLA) for operations and maintenance (O&M) on the group’s own installed systems. As a CIDB 8 ME contractor, the group is further expanding its EPC services to include turnkey design, fabrication and commissioning. This presents the need for qualified engineers as part of the group’s technical team capabilities. “I previously worked for an EPC consulting company specialising in steel construction. It opened my eyes to the intricacies of project and programme management, and how important the details are in delivering the exact solution and seeing the final structure take shape,” says Zurfluh. “That’s why I wanted to become a mechanical engineer: to experience raw metal translated into state-of-the-art functioning systems – in this case, pumps. This has always been my lifelong ambition, and now I get to do it on a daily basis. Allied to this, my structural steel EPC exposure adds valuable input on the group’s turnkey contracting projects. Pumps don’t function in insolation – they need integral installation to suit application-specific outcomes,” Zurfluh continues.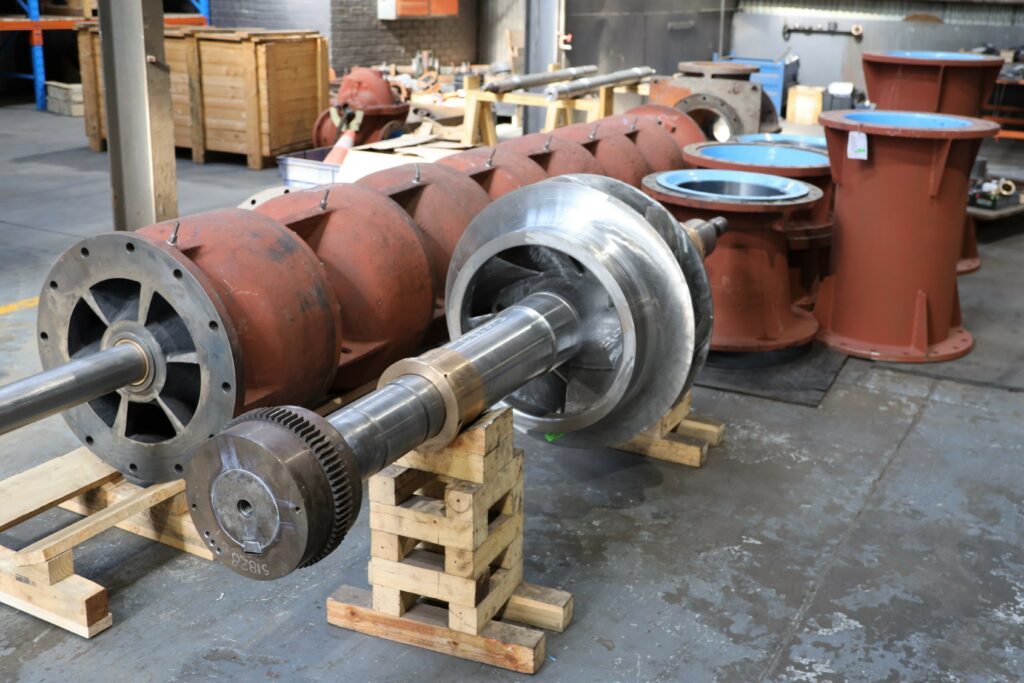
Computational fluid dynamics
Group software investments include an industry-leading CFD (computational fluid dynamics) simulation program that enables the engineering team to model and interrogate new pump designs, pump retrofits and upgrades, as well as the analysis of flow behaviour in a new or existing system. “For example, we can simulate the implications of installing new pump manifolds and determine the envisaged pressure drop, the pipe sizing requirements, etc. We can also import other 3D design data to build the working digital model,” Zurfluh explains.He also points out that adopting a holistic approach is important in achieving the best performance. For a bulk water transfer scheme, for example, any current or future network upgrade must factor in anticipated urban expansion and population growth. That means selection and optimisation are crucial in terms of return on investment and life-cycle costing.
Forecasting future plant upgrades is equally important to ensure that pump rooms have space for additional units at a later stage, or that treatment works can be expanded when they reach their current design capacity. In turn, strict condition monitoring and maintenance regimes are essential – solutions provided by the group’s O&M services. For clients, the major benefit of signing an SLA is that O&M becomes an outsourced solution undertaken by an expert OEM with full parts inventory backup. That translates into fast turnaround on scheduled maintenance, and reduced breakdown times due to predictive and preventative maintenance. Routine on-site inspections are performed using advanced vibration and laser alignment tools for ongoing condition monitoring. There’s also a growing demand from clients for energy-efficient designs. “The common request increasingly asked by utilities and municipalities is how they can lower electricity costs while still maintaining bulk demand targets. So, there’s a big shift in how we do the pump and electric motor selections since, over the years, the electricity cost to run a pump far outweighs its initial acquisition and commissioning cost,” says Zurfluh.Manufacturing investments
At the heart of the process is the group’s manufacturing capabilities, with a core specialisation in custom builds and an ongoing investment in new machines and tooling to ensure that the fabrication lines can run on a 24-hour basis, when required. As Zurfluh explains, the objective is to make sure that the group is self-sufficient in terms of production and quality control. Recent acquisitions include: an 8 m long lathe with a 1.4 m swing, specifically for circulating water pumps; a 12 t CNC horizontal boring machine; a 2.5 m vertical boring machine; and what is believed to be the second largest key slotter machine installed to date in South Africa, which will be used for large impeller fabrication. Production focuses on new pump fabrication, upgrades and complete overhauls. The group also has a pump exchange programme for mission-critical sites, like power stations, where downtime must be reduced to a minimum.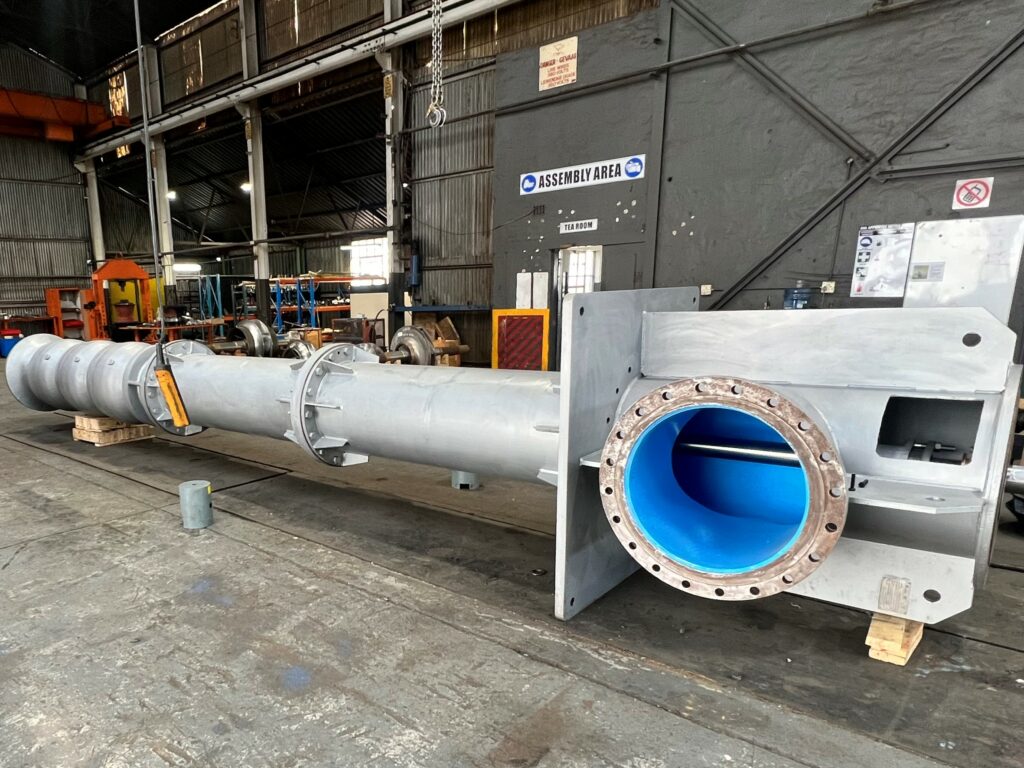