Allied to this is the fact that demolition technology is advancing globally, which is having a positive impact on the local sector. While demolition robots and remote demolition have been available for many years, there are limitations to the technology. For example, Jet Demolition has remote-control units that can be fitted to its plant.
“This type of technology is used specifically where there is a risk of soil subsidence during sinkhole remediation. The machine operator is able to control the machine from a distance. However, there is a definite compromise on precision and reactivity,” says Kate Bester, Contracts and Project Manager at Jet Demolition.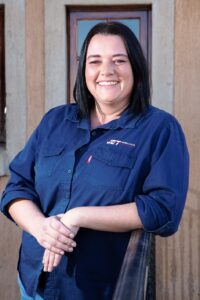
In addition, they are one of the first commercially viable service robots to tackle applications in a traditionally labour-intensive industry. The value of the overall construction robot market was anticipated to be $321 million in 2022, with a global compound annual growth rate (CAGR) of 8.7% from 2016 to 2022.
In addition to demolition robots, autonomous mobile robots (AMRs) are one of the latest and most innovative automation solutions available. AMRs differ from automated guided vehicles (AGVs) by their degree of autonomy, with AMRs far more independent and adaptable than AGVs. They can navigate complex environments and avoid obstacles without the need for external guidance systems. “Automating demolition is all about safety and efficiency,” says Bester, adding that it also has the potential to reduce cost for both demolition and construction companies. Robotic automation places human workers out of harm’s way and allows them to be more productive. While the initial capex is high due to it being a relatively new technology, the long-term return on investment and impact on health and safety more than offsets the initial cost, notes Bester. “Our main concern is for the safety of people. Our methods, resources, and approach are all aligned exactly to serve this purpose. We have been in business since 1994 and have kept our focus on the main objective of completing a project safely, on time, and to international standards,” says Bester. While Jet Demolition undertakes most types of demolition work, its preference is generally for a mechanical application as a ‘best possible’ approach. This is in accordance with international best practice of separating workers from risk. Jet Demolition has an extensive equipment fleet, giving it the flexibility to draw from within its own reserves to suit the method selected. Plant is kept in top condition by an in-house team of mechanics. It is generally traded in at low hours, generally much sooner than typical in the construction industry. Plant is ready, in good working order, and always available for the next project, concludes Bester.