A concrete reservoir can last 100 years – provided the concrete is durable and there is best practice in terms of construction; quality control; structural design; and detailing.
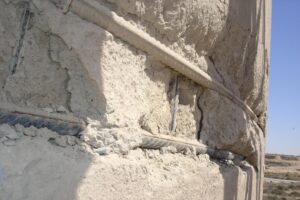
“When we design and build new reservoirs, it should be done so well that they last as long as possible, which is at least a century. This is not unusual for an appropriately maintained concrete reservoir that has been delivered to the highest possible quality standard,” says Dr Rod Rankine, materials specialist and owner of Rod Rankine Engineering Solutions.
He adds that there is a rapid decline in the quality of the design and construction of concrete water retaining structures in municipal jurisdictions. “In some instances, concrete construction design and application can be so poor that these partially completed and final structures are often demolished and rebuilt entirely. Others require large concrete repairs which is costly and disruptive to service delivery. This places additional strain on already-stretched municipal resources, exacerbating the serious water crisis with which the country currently grapples.”
Appropriate concrete design and construction, which includes adequate measures to prevent concrete corrosion, can save asset owners significantly in major repairs further down the line.
According to De Sitter’s
Rule of Five, R1 invested during the design and construction of reservoirs is equivalent to:
- R5 after the structure has been built, but corrosion is not yet evident
- R25 when corrosion has started at some areas
- R125 when corrosion has become widespread, and rehabilitation is required
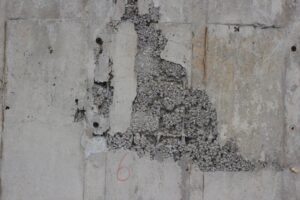
“For example, a concrete reservoir that has been built with reinforcing steel that has been hot dip galvanised according to the SANS 121 specification will last three times longer than a similar water-retaining structure that has been constructed with black rebars. This justifies the additional expenditure in hot dip galvanising. There is currently no other method that safeguards against reinforcement corrosion, the leading cause of failure of reinforced concrete structures, than hot-dip galvanising,” states Dr Rankine.
Despite the availability of such state-of-the-art technologies that improve the performance of concrete and the already many proven benefits of concrete, defective reservoirs are still being constructed on behalf of South Africa’s municipalities.
Joints Reservoirs mainly leak through cold-joint lifts, which is the weakest link in concrete water-retaining infrastructure and where reinforcing bar starts to corrode first.
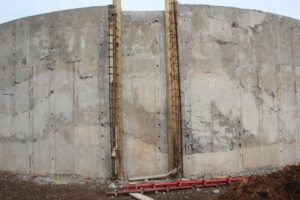
Cold-joint lifts are a necessity, but they are inevitably a weak point because the concrete at the top of the previous lift is of inferior quality as a result of bleeding. Honeycombing at the bottom of walls, adjacent to joints between form panels and at cold joints is a problem is a common cause of inherent weakness and deficiency which continues to bedevil this industry. It can all be attributed to a poor understanding of concrete technology and poor site practice.
Many of the vertical cold joints that were analysed by Dr Rankine were as result of working in one direction on closed-circuit structures. The best practice is to place concrete by starting with two teams at one position and then working in opposite directions so that when they meet, they can join fresh concrete to fresh concrete, when constructing a reservoir wall to avoid this problem.
Compaction
Appearing as cracks, honeycombing and areas with exposed aggregate and reinforcing of various sizes, they prevent a strong, water-tight bond between the two layers in the reservoir wall.
The large areas of honeycombing that Dr Ranken have observed time and again are as a result of poor compaction practices and incomplete placement of concrete in formwork.
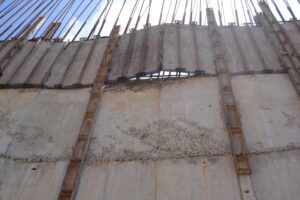
Sound concrete compaction practice is often largely ignored by contractors appointed to work on these projects. However, onus also lies with resident engineers supervising the works. “There are some inconvenient truths when it comes to proper concrete placement that need to be heard by the companies that were appointed to build these reservoirs. Firstly, there is no such thing as self-levelling concrete and pumped concrete is certainly not self-compacting. Secondly, there are limits to the amount of concrete that a single concrete vibrator can vibrate in an hour and at least three workers are required to operate a single poker vibrator (one to hold the poker, one to manage the engine while the third is sitting on the toilet),” adds Dr Ranken.
“Because the natural packing density is interrupted by the flat floor and struck-off top, porosity near the top and bottom of the reservoir walls that I have surveyed are 0.30
pu. Near the surface, porosity is less than 0.48 due to interruption of the natural packing density by the flat shutter. In the centre portion of the reservoir walls where natural packing density is optimal, porosity is 0.26
pu. Thus, the paste requirement near defined edges is aways higher. This would not have occurred if greater care had been practiced when placing the pumped concrete in the deep forms by using an elephant truck or hydrovalve,” he continues.
Another cause of honeycombing is grout loss between adjacent shutters. A lot of grout can be lost due to a lot of grout was being lost due to “leaky formwork”. Contractors can ensure tight joints and sometimes use self-adhesive compressible foam gaskets to successfully retain the grout between the adjacent shutters.
Other causes of failures “Considering the very large part that concrete cover plays in concrete durability, it is concerning that there are high incidences of inadequate concrete cover,” noted Dr Rankine.
He adds that the incorrect application of and, in some instances, over reliance on hydrophilic waterstops as a recurring problem. “Installed across concrete joints, they also often become misaligned and are damaged when casting adjacent concrete panels. For a hydrophilic waterstop to work as intended, it has to be coaxially confined. Many contractors have been coerced into using these just because they exist, whereas an excellent watertight joint can be achieved without a hydrophilic strip.”
Failures can also occur due to the incorrect design and installation of bearing pads, which play a critical role in transferring loads to the foundation of the structure and facilitating movement. A case in point was the severe load- and movement-related cracking of a reservoir wall founded on a Kilcher-type polytetrafluoroethylene bearing with bandage seal between the inside wall and floor.
“The Romans used lime concrete that has stood for centuries and is doubtless better today than when it was first made. However, concrete made with hydraulic lime or Roman cement, was nothing like so strong and serviceable as Portland Cement concrete. We refer to it merely because it shows the remarkable resistance and life possessed by concrete. If lime concrete has stood unharmed throughout the ages, Portland Cement concrete, which is infinitely superior, must be imperishable,” Dr Rankine concludes.