Interwaste, a Séché Environment Group company, has launched a R100-million leachate and effluent treatment plant in South Africa.
“This initiative reflects Interwaste’s commitment to providing a circular solution for South Africa. It will help companies comply with the country’s ban on liquid waste to landfills and support the national waste management strategy. Additionally, it represents another step by Interwaste to address its own leachate management impacts,” states Kate Stubbs, Interwaste’s marketing director.Leachate
Leachate is formed when rain/surface water passes through the waste body of a landfill. It becomes contaminated as it filters through the waste body, resulting in a complex mixture of organic, inorganic and potentially hazardous substances such volatile organic compounds, heavy metals or even pathogens. This can cause water pollution, soil contamination, health risks, odour problems, regulatory non-compliance and ecosystem damage. Potential components:- Organic compounds – VOCs (benzene, toluene, xylene), dissolved organic matter, phenols
- Inorganic compounds – heavy metals, salts, ammonia
- Nutrients – nitrogen compounds, phosphates
- Anions and cations – chloride, sulfate, bicarbonate, calcium, magnesium
- Pathogens – bacteria, viruses, other micro organisms
- Trace elements – copper, nickel, manganese, other trace metals
- Contaminants – pesticides, herbicides, pharmaceuticals, industrial chemicals.
Plant
She adds that this is why the development, implementation and commissioning of the Leachate and Effluent Treatment Plant is a monumental achievement in the realm of sustainable waste management. “Up until now, there has been no sustainable solutions for leachate in the country.” The plant will process various liquid waste streams and is designed to accept and treat effluent waste across two categories including: leachate produced by Interwaste’s own facilities or other waste disposal facilities and liquid waste streams from various industries such as manufacturing, mining, oil and gas. Equipped with technologies that not only effectively treat these waste streams (43 million litres of effluent a year), the plant also recovers an impressive 80-90% as clean, reusable water. The clean water produced by the plant exceeds the Department of Water and Sanitation’s safe discharge limits and will produce approximately 36 million litres of clean water per annum. After a rigorous design and development phase, the Interwaste Leachate and Effluent Treatment Plant employs a multi-stage treatment process that ensures the efficient removal of contaminants while maximising water recovery. From pre-treatment analysis, homogenisation, clarification and separation through to reverse osmosis, evaporation, stabilisation and post treatment testing, the plant achieves a high efficiency and recovery rate of 80- 90% clean water for reuse.“Our main plan is to re-use the clean water onsite for operational purposes like dust suppression, thereby reducing our use on municipal or borehole sources, but it can also be discharged to replenish the local water course,” says Stubbs.Basic steps are to test incoming leachate, pre-treat it, process and recover clean water. Key features include:
- Flexibility to treat and process a range of liquid waste types including leachate.
- Bespoke pre-treatment processes which balance pH levels and removes elements such as suspended solids, pollutants, and oils to ensure the optimal blend is created, enabling the facility to operate within safe conditions, minimising risk and ensuring maximum output.
- Refined concentration methods that separate salts from water.
- Advanced filtration systems to remove remaining constituents from the water.
- Continuous monitoring and control systems to ensure optimal performance and compliance with regulatory standards.
- Reverse osmosis is included too which demonstrates the ability to go to a high level of cleanliness (very fine filtration process).
Talbot
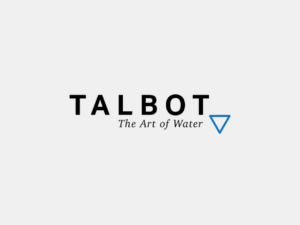
Through the design process, Talbot engaged with KMU Loft, an international market leader in mechanical vapour recompression (MVR) evaporation units. These evaporators from Germany were chosen for their robust design and energy efficient operation. Concentrating the leachate wastewater streams to up to 25% total solids, the MVR evaporators significantly reduce the liquid burden on the landfill site. The distillate generated is polished with reverse osmosis (RO) and is suitable for discharge to the environment or sale to end-users. High levels of ammonia, due to the nature of the feed, are removed from the RO brine in an SG Plastics Ammonia Stripper/Scrubber and captured as a byproduct with potential value. The stripped RO brine is returned to the feed tank, thereby avoiding any water losses and improving overall efficiency. The plant was designed and built in conjunction with a Kainos pretreatment facility, comprising an API, clarifier, and DAF units. The overall plant can accept a range of leachate and industrial effluent streams, concentrate up by a factor of nine or higher, and produce water within the legislated general discharge limits. Two years were spent researching, analysing and designing the plant and one year to build it. Interwaste is exploring the implementation of similar plants elsewhere in the country.