Continuous electro deionisation (CEDI) is a water treatment process that uses a combination of ion-exchange resins, ion-exchange membranes, and direct current to continuously deionise water without the need for chemicals. This is used to produce ultrapure water.
Ionpure® modules first commercialised CEDI for water purification in 1987. Since then, the company has continued to evolve and bring out new technologies. It has undergone a number of transitions and was recently acquired by Xylem, while trading under the name Evoqua Water Technologies.Evolution of deionisation
Deionisation is typically the last process to remove any remaining dissolved solids (such as sodium chloride) in water. Previously, the only option available was chemically regenerated ion exchange resins where the mixed-bed stage was preceded by separate units for cation and anion exchange. In a bid to further improve water quality, reverse osmosis (RO) was introduced to reduce total organic carbon as well as chemical usage in water treatment systems. This was followed by the mixed bed stage. “As the cost of RO started to drop, the uptake of the technology increased. RO pulls out the majority of bulk ions and organics and prepares the water for CEDI technology,” says Patrick Buzzell, director: Product Management, Ionpure® products.What is so great about CEDI?
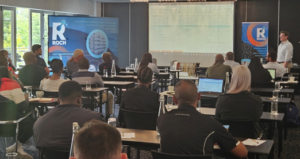
“With CEDI, there is no need to use the hazardous regeneration chemicals, making the entire treatment process intrinsically safer and environmentally friendly. There is no need to manage the pH levels all day and there is limited downtime,” states Buzzell.Ion exchange resin is a batch process, therefore there is a threshold or a minimum water quality that needs to be maintained. As the resin beds begin to exhaust, the water quality will drop. There is a breakthrough of ions at the end of the service cycle and a rinse out of regenerant at the beginning of the next service cycle. Usually, the detection of a weakly charged contaminant like silica is an early indicator that the resin bed is beginning to exhaust. At that point in time, a new resin must be used, or regeneration must take place. This interrupts the treatment process. Buzzell adds that when using CEDI technology, the water quality will remain consistent for the life of the product, creating a stable operation. “The longevity of CEDI technology largely depends on several factors, including maintenance practices, operating conditions, and the quality of the feed water. In general, CEDI systems can operate continuously, with an average lifespan of five years.”
How does CEDI work?
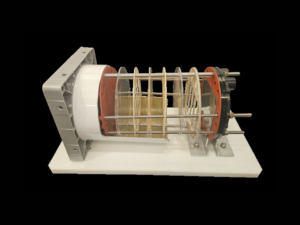
A chemical-free, self-regenerating
technology used to provide a
consistent flow of high-quality
deionised water
“It is important to remember that this is not a pressure driven process. This is very different from RO that is pressure driven. CEDI requires an electric field. Ionpure’s technologies run on DC power, providing up to 600 volts and 13 amps output. We have also developed our own power controllers through collaborating with other partners. It is the amperage that moves the ions through the membranes,” explains Buzzell.The design flow for a full sized Ionpure® VNX-MAX module is 15 m3/hour, with the minimum at 7.5 m3/hour and maximum at 22 m3/hour. “The higher the flow rate, the less time there is for the electric field to work on the ions. So generally speaking, the lower the flow rate, the better the performance. But if the flow is too low, the channels will not fill up adequately and there will be inadequate flow distribution,” he adds. Higher loads of CO2 negatively affect the ultimate quality of the water and is accounted for with Feedwater Conductivity Equivalent (FCE) or load. For example, 10 μS/cm of load will give better water quality than 40 μS/cm of load. “Most of our modules go up to 40 μS/cm of load. If the loading is greater than that, the module will continue to operate, but we cannot predict the quality of the water at the end of the process,” says Buzzell. CEDI is a compelling option for various water treatment applications, particularly in industries where water purification is critical. It is an efficient and cost-effective method for producing high-purity water with low levels of dissolved solids. It offers several advantages over traditional ion exchange processes, including high efficiency, low operating costs, low maintenance requirements, and flexibility in terms of scalability and space requirements. This makes it widely used in power production (boiler feed), science-intensive industries, pharmaceuticals, food & beverage, general industry, and production of high-purity substances. Contact Roch for more information.