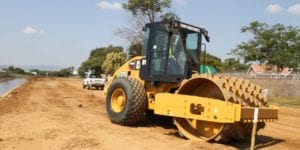
Tshipi Investments’ latest generation Cat CS533E vibratory soil compactor, equipped with a padfoot shell kit, operating next to the irrigation canal
Recurring stormwater damage to an asphalt route bordering an irrigation canal in Groblersdal is being countered with a concrete riding surface that provides a lasting solution. A Cat CS533E vibratory soil compactor is a vital component of the earthworks mix. A major farming town situated some 32 km north of the Loskop Dam (with its estimated 178 million m³ capacity), Groblersdal is situated in Limpopo province’s Sekhukhune District and is South Africa’s second largest irrigation settlement, receiving healthy downpours during the summer season. While rainfalls are welcomed by farmers, their potential toll on road infrastructure and drainage is another factor, and needs to be countered by upfront design interventions, plus scheduled maintenance. Within the town of Groblersdal, one section was under constant pressure, namely the Kanaal Road that links to the industrial centre and acts a strategic bus route. Kanaal Road borders an irrigation canal, which, during the rainy season, is prone to significant flooding, making it virtually impassable and resulting in the structural deterioration of the road prim, aggravated by heavy truck traffic.
Reconstructing Kanaal Road
In response, Limpopo’s Elias Motsoaledi Local Municipality approved the reconstruction of this route, to be managed by consulting engineers Tumber Fourie. The firm has a three-year contract with the municipality and forms part of its engineer panel. Two previous asphalt rehabilitation projects could not withstand the flood pressures, so the design alternative chosen was a concrete surface with an 8 m road width, running over a 1.1 km section and reconstructed at a contract value of approximately R14 million. Construction work began in November 2015 with completion of all phases scheduled for July 2016. The contractors employed on the Kanaal Road are Tshipi Investments and Big Rock Construction, working in joint venture on this phase. Both are 7CE PE contractors in terms of the Construction Industry Development Board (CIDB) grading system, and they form part of an Elias Motsoaledi Local Municipality two-year contractors panel. Tshego Mashabela, owner, Tshipi Investments, expands on his entry into the construction industry: “We’re a young company, based in Limpopo and established in 2012. Our goal is to be mentored by South Africa’s leading construction companies, helping us evolve our current business model. The medium- to longer-term plan is to tender on projects nationally. This growth will be spurred by the potential to climb to a 9CE grading – the highest in the CIDB ranking.” Tshipi Investments’ focus is on civil engineering and infrastructure projects, which includes underground services for affordable housing developments, as well as RDP toilets. In terms of roads, to date, the company has successfully completed a number of asphalt projects, as well as a bridge, but the Kanaal contract is the first concrete road they have tackled. The specification of a concrete road will promote good water runoff and the design makes provision for a 30-year life.
To prepare the road, the contractors have excavated down to approximately 600 mm in the form of a box-cut, which gives a clear indication of the extent of the remediation required. “Once compacted, this natural layer is being overlain with a high-strength, woven, UV-stabilised polypropylene geotextile,” explains Jerry Stevenson, resident engineer, Tumber Fourie. “This geotexile provides a tensile strength of approximately 83 kN per metre in both directions, and promotes good subsoil drainage.”
The 150 mm sub-base is being stabilised with a 2.5% cement composition, while the final 150 mm readymix concrete layer will incorporate 943 reinforcement mesh. A concrete trial section was established during April 2016.
Padfoot compaction
Supporting Tshipi Investments’ earthmoving fleet on the Kanaal project is a latest-generation Cat CS533E smooth-drum, vibratory soil compactor, acquired in April 2016, together with a padfoot shell kit. “The latter is an interchangeable solution that expands the application range of the CS533E, enabling the machine to work in either cohesive or semi-cohesive material,” explains Bradley Page, sales professional: Polokwane Cat Sales, Barloworld Equipment. (Barloworld Equipment is the Cat dealer for Southern Africa.) The two-piece padfoot shell kit bolts on to the smooth drum and features 90 mm high pads. These shell halves can be installed or removed in about an hour with the use of an approved lifting device. Weighing in at around 10 840 kg in standard smooth-drum configuration (with ROPS / FOPS cab), the Cat CS533E is powered by a Cat 3054C engine generating a gross power of 97 kW. Maximum and minimum centrifugal forces are 234 kN and 133 kN respectively, with a nominal amplitude – high and low – of 1.8 mm and 0.85 mm, at a standard vibratory frequency of 31 Hz/34 Hz. The maximum amplitude with the shell kit installed is 1.2 mm. At Kanaal Road, the Cat CS533E is set up in padfoot configuration for all layer works phases, working in tandem with a pneumatic tyre roller for final compaction. For these and other tasks, the Cat CS533E’s exclusive dual-pump propel system provides a separate, balanced hydraulic flow to both the rear-drive axle and the front-drum drive motor. This unique dual-pump propel system provides good grade climbing, machine control and tractive power. Dual pumps also minimise drum and wheel spin-out in low-traction conditions, while high working speeds increase productivity. For each 200 m section on Kanaal Road, the Cat padfoot makes approximately 10 passes, and the pneumatic four to six. Tshipi Investments says that the Cat CS533E has performed exceptionally well in helping to achieve the designed compaction densities for the road bed (90%), lower selected (93%), upper selected (95%) and sub-base (95%) layers, confirmed by an on-site test laboratory. The end result will be a world-class, “weatherproof” road built to last generations.