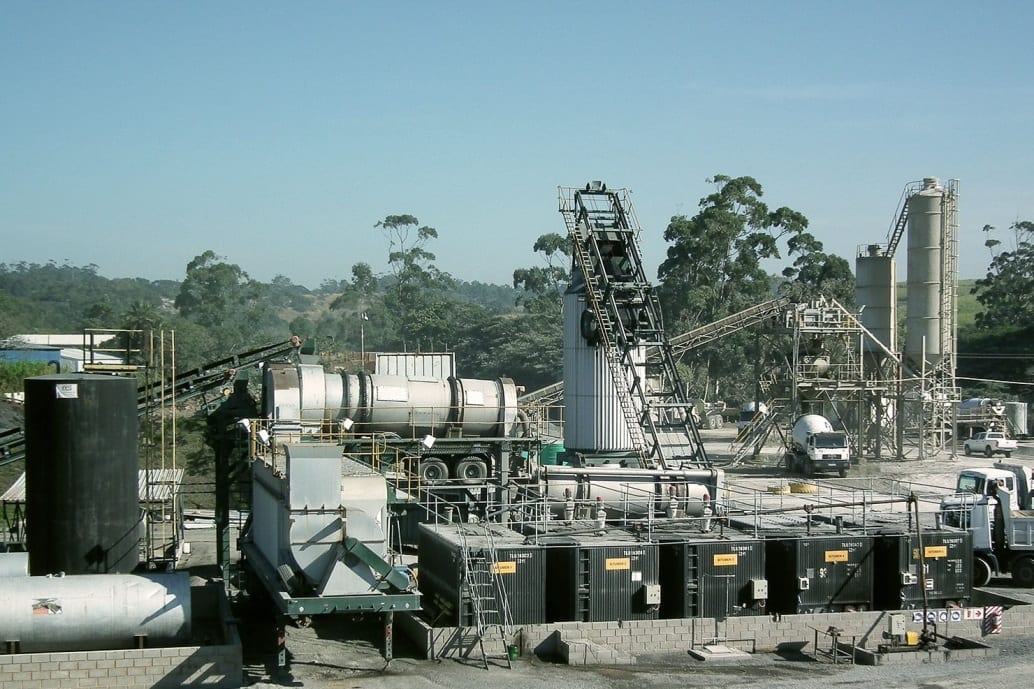
National Asphalt plant.
National Asphalt MD Sean Pretorius talks about the company’s commitment to developing optimum solutions for existing and new road construction. What is the company’s strategy for 2017? We take a leadership approach, which means we focus on continuous improvement though our research and development programmes. The 2015 period was a challenging one for South African construction – highlighted by local bitumen supply shortages – but, despite this, project awards in the roads sector showed a steady trend, improving slightly in 2016. We are bullish going into 2017 and believe that the macroeconomic prospects will improve, supported by more buoyant international trading conditions. Tendering at the lowest price has been a historical trend in South Africa. In my opinion, current government procurement legislation can be quite restrictive. It will be difficult to change this in the short term. However, we believe it needs to be addressed, as it often impacts on quality and ends up costing more to redo failed sections. That’s why tender pricing awards have to be more realistic and sustainable, especially if we want to promote SMME development.
Are there supply challenges to consider this year? Surprisingly, the availability of quality aggregate supply remains a challenge and even more so now with the introduction of the Performance Grading (PG) specifications. Bitumen supply will be under pressure again this year, with a number of the refineries shutting down for their planned maintenance programmes during 2017. Shortfalls in supply will need to be offset by supplementing with imports where needed. However, the lack of price parity between local and imported bitumen is always challenging: very often, it’s difficult to get compensated for the cost of the imported bitumen, which is higher than the local product. Add the volatility in the exchange rate and the dynamics become very challenging to manage.
What is the current status of the equipment fleet? We have a full complement of fixed and mobile asphalt plants, together with an allied paving fleet. One of our key advantages is that we are very mobile. Combined, the company has an output capacity exceeding 1,500 000 tonnes of asphalt per annum.
How important is the cross-border market? It is very important. We’ve established a company in Botswana, trading as Belabela Asphalt, which has a 51% local ownership, and we believe there’s huge potential for growth in this country. Other regions where we have a presence include Mozambique. A recent example is a hydro-cutting project completed by our subsidiary, Shisalanga Construction, at Maputo International Airport during January 2017.
Is hydro-cutting gaining ground locally? This is a rapidly growing business unit. The technique, referred to as hydro-texturising, is a cost-effective solution for repairing flushed bituminous pavements. It also cleans the voids of an open-graded mix, increasing service life and water drainage, and decreasing noise. This results in a safer runway or road surface, and extends the life of the asset. Once the excess bitumen is removed, the stone-chip matrix remains intact.
Are there plans to introduce new products this year? Since inception, National Asphalt has pioneered the introduction of a range of new products that have since become the standard in South Africa. One of the most significant of these is reclaimed asphalt (RA), which was first trialed and proven in eThekwini and thereafter gained traction on projects for Sanral and other key projects in South Africa. Every year, we usually bring in three to four proven technologies on a trial basis. We don’t always turn these into commercial products, but the R&D experience is invaluable. During 2017, we will be working on several products that could see commercial application shortly.
Some municipalities, like eThekwini, have been very receptive to new technologies. Examples include the development of warm-mix asphalt, the RA (as mentioned) and, more recently, the adoption of high-modulus asphalt (EME), which has been very successfully applied on various N3 sections in KwaZulu-Natal. These include steep gradients catering for slow-moving, heavy truck traffic. The 10/20 bitumen used is low penetration grade, resulting in the EME producing a number of high-performance characteristics, e.g. high resistance to rutting and deformation.
On another note, we fully support the decision to introduce PG specifications, as this will raise the overall industry standard. Of course that will mean a higher requirement for technical expertise, which we’ve catered for in terms of our ongoing recruitment, training and development initiatives.
Was EME specified for the GO! Durban BRT programme? Yes, EME has proved to be ideal for the GO! Durban initiative. This bus rapid transit network being established in the city will see National Asphalt supply key phases.
Is there a market for warm-mix asphalt? There definitely is, but the take-up tends to be low at present. Warm-mix asphalt has key advantages: it is produced at a lower temperature compared to hot-mix products (typically between 10°C to 30°C lower) and so is more environmentally friendly to manufacture (since there are fewer emissions). Warm mixes can also be transported over longer distances and paved at
lower temperatures.
Is porous asphalt a viable option? Definitely: it has some distinct advantages and can be utilised for managing issues such as stormwater run-off. To date, our involvement with porous asphalt has been more for the
support structure used with products such as Salphalt and in the construction of artificial turf.
What measures are being adopted to promote sustainability? Recycling has now become the norm for most industries globally, and South Africa is rapidly catching up. Some of the trends are still very experimental, such as the possibility of using glass as a composite in asphalt. Sanral now regularly specifies up to 40% RA as a component on its road rehabilitation projects. However, we believe there are opportunities to raise this percentage for certain mixes. In line with this, National Asphalt has completed its own trials where we’ve been able to attain a 100% RA mix with the use of our specialty admixtures.
Are additives like EcoNat passing on cost savings for clients? EcoNat, a National Asphalt proprietary technology, has been instrumental in our RA research programme as a bitumen rejuvenator. We have also trialled the use of EcoNat as a road spray and are investigating cold-mix applications, where we have a best-in-class solution.
Are skills gaps a concern? Asphalt construction is a highly specialised area. Presenting a further challenge is the widely acknowledged lack of general civil engineering skills in the industry. To build awareness, we run regular workshops with municipalities around the country and interface with the universities and tertiary education departments on a regular basis.
Any final thoughts? Technology has become an integral part of our daily lives, so, to stay abreast of trends, we all have to embrace innovation. At National Asphalt, that is our overriding philosophy.