to flooding. Aveng Grinaker-LTA commenced on-site on 26 August 2015 and the current targeted completion date for all phases is scheduled for 8 October 2018, explains Bradley Crawford, contracts manager: Civil Engineering, Aveng Grinaker-LTA. “We started with the southern route first and expect to complete this by June 2017,” he explains. This greenfield section is being constructed on previously agricultural land acquired by Sanral.
North and south surfacing
On both sections, the final wearing course will comprise an Ultra-Thin Friction Course (UTFC) surface. Core benefits include improved skid resistance andreduced noise. The northbound route will be resurfaced with a 40% recycled asphalt (RA) mix, in accordance with Sanral specifications. Aveng Grinaker-LTA recently acquired a Comar asphalt plant to meet its RA requirements. After milling the existing northern surface, the next step will be to rip up and stockpile the in situ base. This will then form the new sub-base. (The excess RA will go into the new
selected layer.)
Bridges and culverts
There are five major structures along the new north-south route, the most significant being the Holfontein interchange (B322) with its distinctive clover design. This is a post-stressed bridge that interconnects to the S166 road. B328 is a new precast beam bridge (an original overpass that was demolished and which will now be reconstructed) while B341 and B342 are new overpasses. Then there’s structure 326, which comprises a five-barrel culvert. In addition to routine traffic flows, these bridges are also intended for the requirements of the agricultural industry, where individual farming operations take place on both sides of the N1 and need access in terms of equipment and personnel.Cement stabilisation with Roadstab
On the southern section, the layer works are a minimum of 900 mm deep, with a number of undercuts required to remove unsuitable material. Imported material has been sourced from designated Sanral borrow pits. In terms of the road design, the sub-base layers are being cement stabilised using AfriSam’s Roadstab product.
On the southbound section, some 15 000 tonnes of Roadstab is being supplied with an in situ cement mix design composition of around 2.75%. The moisture content ranges between 3% to 4%.
this requirement.
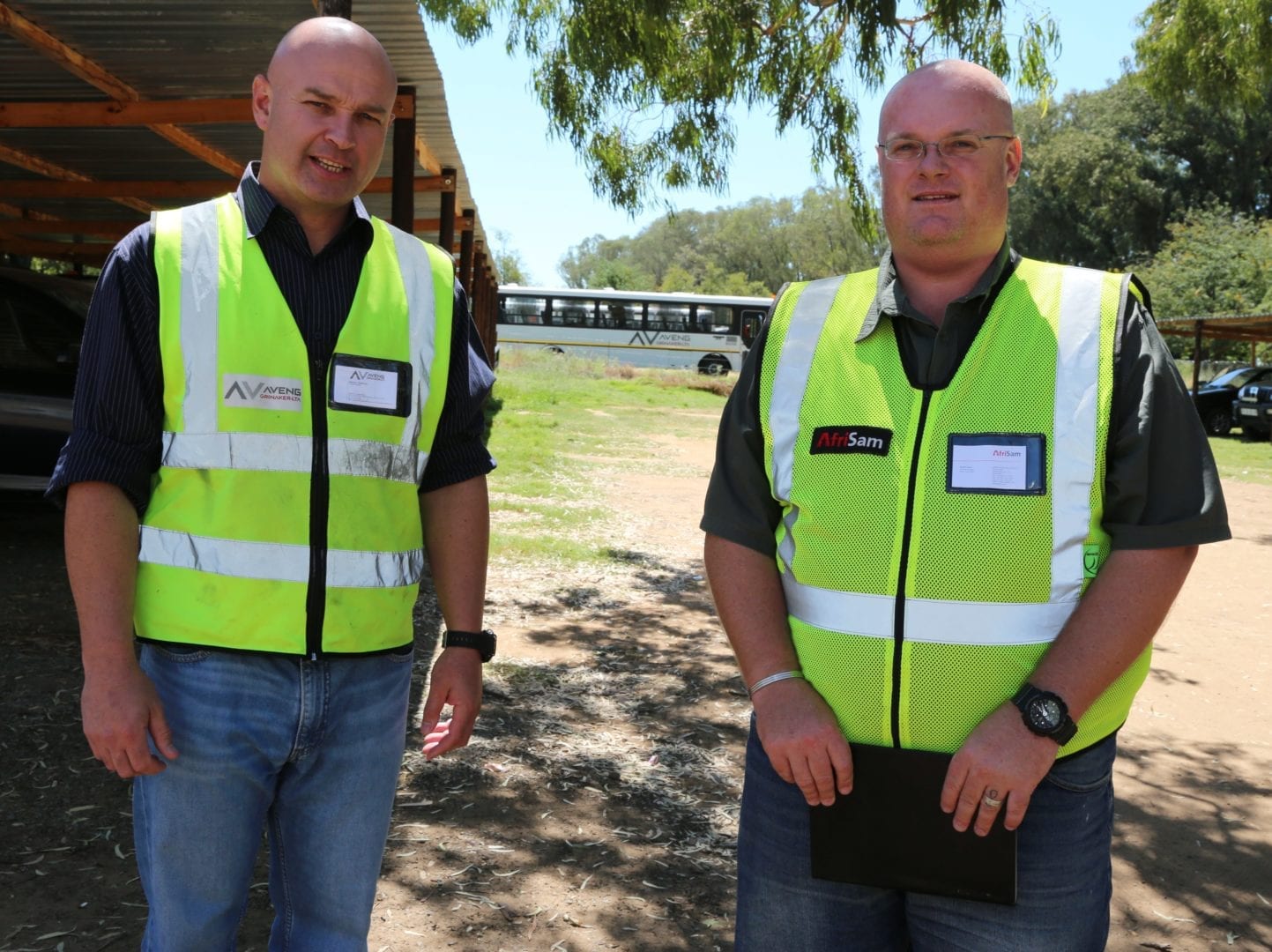
Bradley Crawford, contracts manager: Aveng Grinaker-LTA (left), and Stefan Roos, territory manager: BCM Free State, AfriSam.
Bulk spreading
During the course of the project, Roadstab is being supplied via tankers operated by AfriSam’s sub-contractor, Ezethu Carriers. Each AfriSam bulk tanker has an approximately 34 tonne payload. Normally, two to three tankers are required for each section, which averages around 300 m per day. “Discharging with a tanker is faster and more efficient than the alternative approach of manually spreading via cement bags placed at intervals, so we opted for this approach,” Crawford continues. AfriSam has strict quality-control procedures in place to ensure that the spread rates are correct. Released under pressure, approximately 21.5 kg of Roadstab is deposited per square metre. Each tanker makes two passes depositing around11 kg/m2 on the first layer, and a further 11 kg/m2 on the second pass. Every tanker has a batch number for each section so that it correlates with the soil lab analysis and verification. Once the cement is spread, Aveng Grinaker-LTA uses a
Cat RM300 recycler to work the 350 mm deep sub-base (comprising a 150 mm upper and 200 mm lower layer) in one go. The alternative would have been to mix the Roadstab composition into each separate layer using graders, followed by compaction. This would have been a far more time-consuming approach since the lower sub-base layer would need to be completed first before starting on the upper sub-base. Aveng Grinaker-LTA’s graders are equipped with Trimble guidance systems to ensure a precise final cut. “Like any project, we’ve had our on-site challenges, particularly in terms of extreme weather. For example, the site has experienced around 600 mm of rainfall since October 2016, but prior to this severe drought conditions. Since the onset of the project, we have recorded around 1 157 mm of rainfall to date. It’s a situation you just need to work around and we’re on track and looking forward to opening the southern route in June,” explains Crawford. In terms of the Comprehensive Procurement Guidelines, approximately 6% of the contract value is being spent on employing and upskilling local labour and 12% on empowered SMMEs. Approximately 114 local members have been recruited from the surrounding Ventersburg community, which forms part of the Lejweleputswa District Municipality.