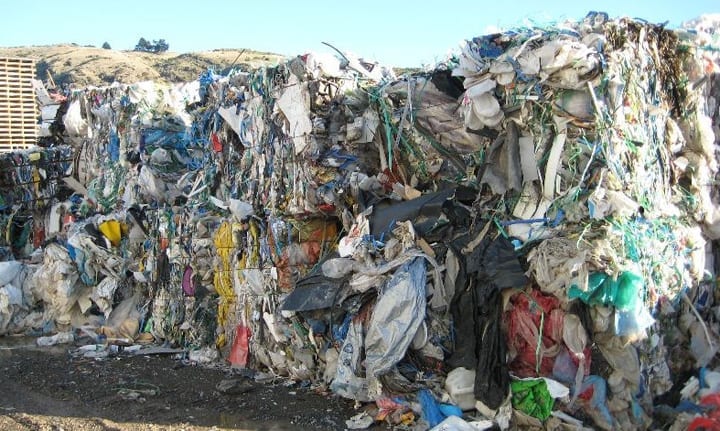
A system using anaerobic digestion to turn plastic into energy is being developed. Picture: Sustainable Initiatives Fund Trust.
Waste-to-energy facilities are fast gaining momentum in South Africa with one already operating in the Western Cape and more for other provinces. The R400 million plant, which is being run by Afrox and New Horizons Energy, is based in Athlone, just outside the City of Cape Town. This facility focuses on converting organic waste into useable biomethane which can be used to create products such as liquid carbon dioxide, organic fertiliser and compressed biomethane.
South Africa and many other African countries like Ethiopia and Nigeria look to leading countries in the waste-to-energy space, to learn about best practices and adapt to a greener lifestyle.
Turning plastic waste into energy and fertiliser
In South Australia, the first systems to use anaerobic digestion technology to turn waste plastics into energy and fertiliser are being developed.
Polymer Organic Energy Treatment (POET) Systems expects to have its first two machines – each capable of processing 20 tonnes of plastic a week – operating commercially in about 12 months.
More than one million tonnes of contaminated plastic deemed unfit for recycling is sent to landfill in Australia each year. In the United States the figure is almost 10 million tonnes.
Inventor David Thompson said his plastic to energy technology had so far successfully been applied to polyethylene, polypropylene, polystyrene and expanded polystyrene.
He said the anaerobic digestion process varied upon disposal feedstock and depended also upon temperature and system set up.
Technology gets attention
“The POET system prepares waste plastic in a way that microbial digestion can take place quickly and I think that’s really the key to making it a commercial opportunity,” Thompson said.
“I have already got inquiries from overseas including a large consortium in South America that is really quite interested to get involved and take the technology over there.”
POET Systems is a 2017 semi-finalist in the
Australian Technologies Competition, which assesses, mentors and promotes companies providing a uniquely Australian take on the future and is open to technologies that have global potential in a range of industries.
Construction
The first two POET machines will be built at wastewater treatment plants in regional areas of the Australian state of Victoria.
The same microbes will treat the plastic and the water simultaneously. The microbes then die and leave behind liquid and solid biomass, which can be used as fertiliser and biogas, and can be separated into methane and carbon dioxide.
Thompson, who is based in the South Australian capital Adelaide, said the methane could be used to create heat and energy, possibly to power the wastewater plant, while there was also potential for the carbon dioxide to be captured and reused.
“So basically the plastics go into an anaerobic situation in wastewater where the microbes digest the plastic and create energy,” he said.
“This client in Victoria is big on wastewater treatment plants and after thinking about his methodology – there’s over 550 wastewater treatment plants in Australia and at least half of those would have anaerobic digestion facilities attached so it’s a good opportunity to go down that path.”
Thompson plans to lodge provisional patent documents for the technology in the coming weeks.
He said the system did not impact on existing recycling practices as it targeted plastics destined for landfill and would add a new revenue stream for companies in the waste industry.
“People in the waste industry have already invested heavily in infrastructure so they know how to do the business,” he said.
“If this gives them an additional opportunity to make money and take on a segment which hasn’t been handled before then I’m happy with that.
“We’ve had a look at a number of scenarios and where it actually works as a business model is at a starting point of 20 tonnes a week.
“So everything I’ve designed ready for manufacture here in Australia is based on 20 tonnes a week and I can scale it up larger from there.”
*Parts of this article were sourced from The Lead.