As contractor WBHO Roads and Earthworks makes good progress on the bus rapid transit (BRT) station at Watt Street in Wynberg, Johannesburg, it is being well supported with almost 9 000 m3 of readymix concrete by construction materials leader AfriSam.
The underground BRT station at the Watt Street interchange is part of the City of Johannesburg’s Rea Vaya system to integrate and improve public transport facilities. The Watt Street station will serve the Rea Vaya bus route from Sandton to Alexandra, as well as from Parktown to Alexandra. The project is driven by the Johannesburg Development Agency. According to Daniel Kwele, construction manager at WBHO Roads and Earthworks – a division of WBHO Construction – the early work from July 2018 included the demolition of the existing Watt Street bridge and the relocation of telecommunication and other existing services. “The earthworks for this project were substantial, involving over 100 000 m3 of material being moved,” says Kwele. “To limit our impact on the traffic pressure in the area, we moved most of this volume at night while concentrating on concrete structures during the day.” The earthworks allow for the bus lanes to descend between reinforced earth walls into the underground station, above which a new interchange is constructed for mixed traffic. The first concrete work included the installation of 342 lateral support piles on the southern portion of the main bridge over Pretoria Main Road, each with pile caps on which would rest 244 precast concrete beams. This section of the project also included installing 18 km of ground anchors, 10 km of soil nails and 13 000 m2 of shotcrete. A spine beam in the mid-section is fixed on one end and supports the 37 t beams all the way on to the northern bridge section.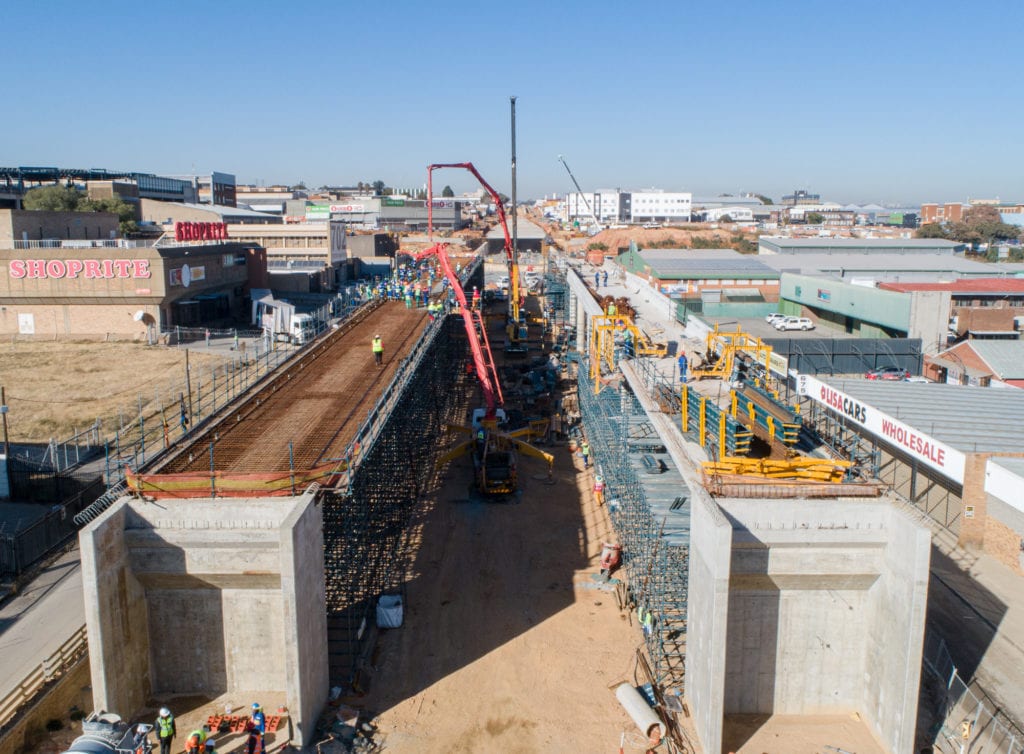
Planning and teamwork
Randal Chetty, key accounts manager, AfriSam, highlights how the experience from previous contracts with WBHO helped to strengthen the working relationship. “Our pre-contract meeting created a good foundation for everyone to know what’s expected, and from there the schedules were generated for the deliveries of the concrete itself,” says Chetty. “The big continuous pours in particular demand a huge amount of planning, so it was vital that everyone worked together to make these successful.” The site is located just a kilometre from the AfriSam Wynberg readymix plant, and AfriSam dedicated between 14 to 17 trucks to the job of servicing WBHO’s concrete pumps during the large continuous pours of around 550 m3 each.Expert mix formulation and delivery
“This was a highly specified project in terms of concrete mix designs, requiring considerable upfront collaboration with the engineers to approve the designs within the Sanral specifications,” he says. “We were also able to demonstrate our years of previous experience in the supply of durable concrete.”Kevin Naidoo, operations manager for AfriSam’s central plants, notes that the company has extensive experience in achieving special mixes and ensuring reliable concrete supply for major bridge works. These include the ambitious Allandale interchange in Midrand, and the pedestrian bridge near Grayston Drive in Sandton. In large continuous pours for this kind of application, the window period for pumping and placing the high-spec concrete tends to be limited – mainly due to the high cement content in the mix.
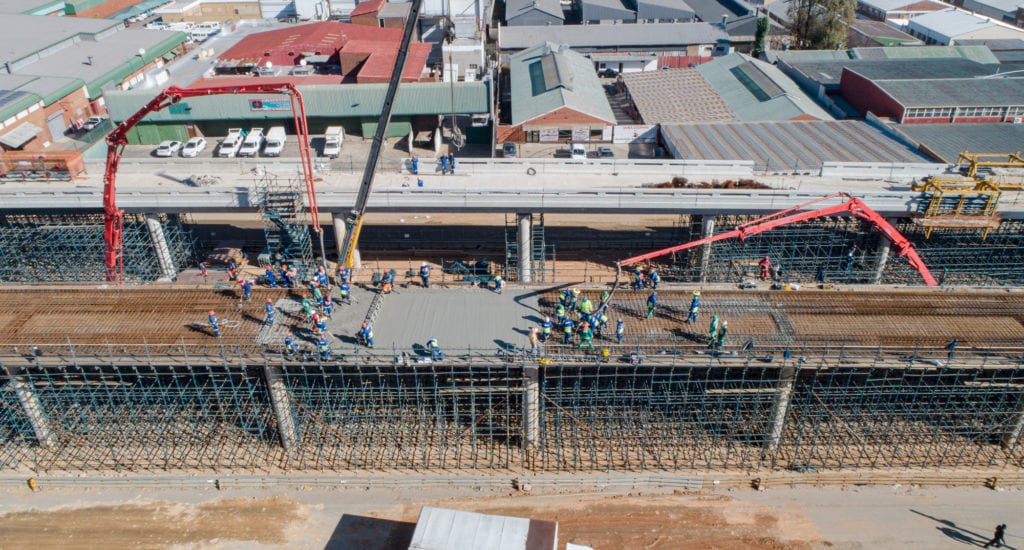
Pre-pour meetings
Kwele agrees that the pre-pour meetings between the contractor and the supplier really helped to foresee and mitigate any challenges. “The pours became a smooth process, thanks to the commitment from AfriSam’s senior management, for which they deserve much credit,” he says. Naidoo emphasises that AfriSam placed its technical experts both at the Wynberg plant and on the project site to coordinate the various elements of each pour, with slump tests being conducted on every truck leaving the plant. Considerable attention was placed on quality and testing, irrespective of the size of the pour. WBHO also had its own concrete testing procedures being conducted at the site. “To make sure that the stringent tolerances demanded by the South African National Standards were complied with, concrete samples were also taken from every truck arriving on-site and tested,”he says.
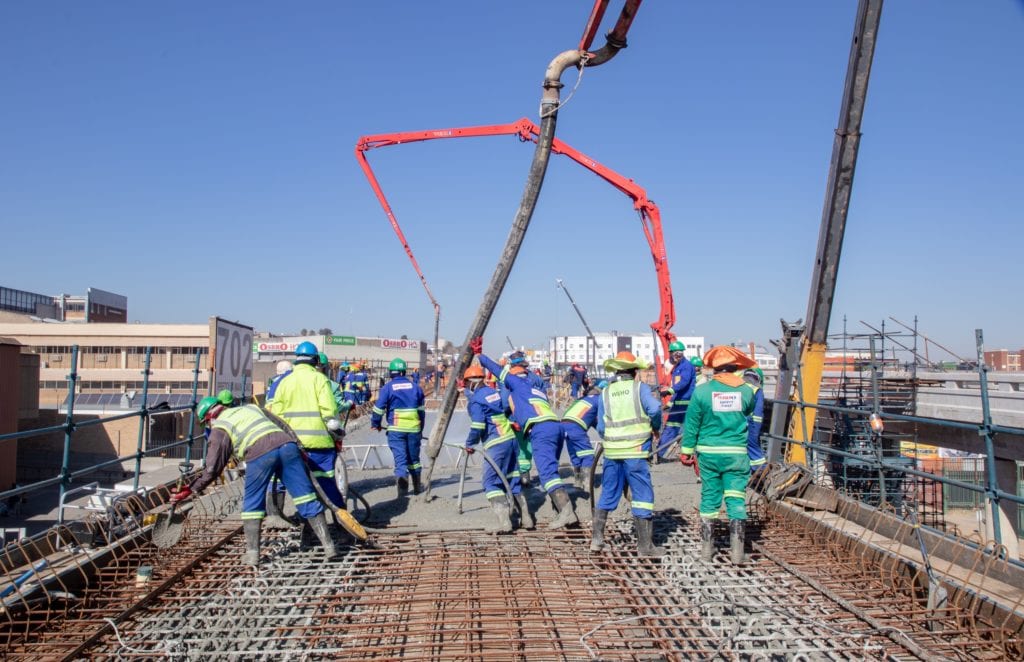
Logistics and execution
In preparation for AfriSam’s involvement, Kwele and his team also spent some time at the Wynberg plant, where AfriSam demonstrated its quality processes and logistics systems for the various construction materials. “For us as the construction team, every project presents its own technical and other challenges,” says Kwele. “On this project, we really appreciated the effort that AfriSam put into this contract, which has been vital in ensuring its success.” Chetty points out that not many concrete suppliers have the capacity to conduct the pour sizes required for this contract, within the timeframe required – while still servicing all its other customers timeously. “We are proud to say that we are one of the few who can do this reliably and professionally,” he says. Among the operational innovations that were jointly developed by WBHO and AfriSam was the implementation of ‘dry runs’ before large pours – to mitigate the risk of disruption at site. He notes that the project team had been delayed on numerous occasions by community issues and taxi disruptions, among others, so the dry runs proved a valuable strategy to ensure that the pour was not interrupted once it began. Over 30 local small business contractors have been engaged on the project.