Setting the standard for Blue and Green Drop certification compliance, Tecroveer has led the market with integrated turnkey solutions, backed by patented processes and technologies, for close to five decades.
IMIESA talks to Izak Cronje, CEO of Tecroveer, about their expertise in water and wastewater optimisation. When the South African government’s National Water and Sanitation Masterplan (Volume 1: Call to Action, Version 10) was released in 2018, statistics quoted indicated that some 56% of wastewater treatment works and 44% of water treatment works were in a poor or critical condition. Plus, 11% were dysfunctional. Fast-forward to 2022 and the situation remains dire, with ongoing interventions required within the municipal arena, as well as private industry, to protect South Africa’s water quality and water security. “However, with an innovative approach, the upside is that most if not all treatment works can be brought back to compliance standards. Plus, it’s clearly cheaper to reinstate than replace,” points out Cronje, adding that one of Tecroveer’s core specialisations is the turnkey refurbishment and upgrading of municipal water and wastewater treatment plants, optimising the use of existing infrastructure by incorporating innovative technologies. In many cases, these are also operated and maintained by Tecroveer. “On all sites where we’re called in to do a condition assessment of the current plant health, we conduct an in-depth analysis and submit a detailed report, which includes a comprehensive budget to meet immediate and future priorities,” he explains. “As with all our projects, proposals are fit for purpose and, wherever practical, we integrate the existing infrastructure and equipment into our design to save on capex and opex costs. Essentially, we don’t only repair existing equipment, but do an in-depth investigation to diagnose the problem and address any process and/or equipment shortcomings.” Tecroveer’s competitive advantage is the group’s turnkey design and contracting approach, with vastly experienced process, civil, electrical and mechanical engineers employed in-house. Plant designs are supported by ongoing research and development, and Tecroveer’s comprehensive range of mechanical and electrical equipment, which is manufactured, sourced and supported in South Africa. “The starting point for optimum plant performance is predictive and preventative maintenance. Since many municipalities are financially constrained, it makes sense for them to outsource operations and maintenance to skilled contractors who provide performance guarantees and incur the cost of any budget overruns,” Cronje continues. Within the private sector, there’s also been a growing trend to outsource non-core functions, with Tecroveer providing design-build-operate-maintain effluent treatment services for industrial clients that include AB InBev and Distell.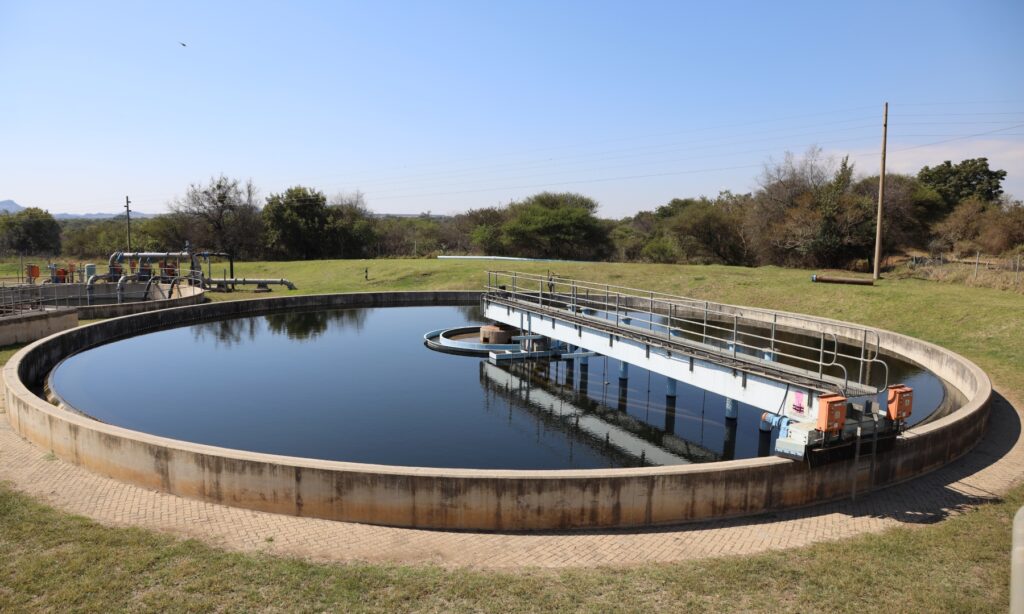
Process excellence at Marikana
Historically, the mining sector has always been a key focus area for Tecroveer – a prime example being its long-term operations contracts for Lonmin’s, and subsequently, Sibanye-Stillwater’s numerous wastewater treatment plants at the Marikana PMG mining complex in the North West. (Sibanye-Stillwater acquired the Marikana shafts as part of the Lonmin acquisition in June 2019.) Some 15 years ago, Tecroveer was invited to submit a design and build proposal for a new 4.5 Mℓ/day facility alongside an existing Tecroveer plant originally commissioned in the 1980s at Lonmin’s Karee operation. This new plant would support the mine’s need for additional water beyond its capped Rand Water allocation. The new wastewater plant would also serve the requirements of the surrounding Marikana community, which at that stage didn’t have a waterborne sanitation system. Given the go-ahead, Tecroveer proceeded with its design and subsequent commissioning of the new Karee plant. As part of the contract, Tecroveer also upgraded an existing pump station, with the local municipality installing the pipeline connections to the new treatment works. Additionally, Tecroveer designed a stormwater catchment network at Karee to capture run-off from the mine’s contaminated areas and channel it through to the effluent storage dams to increase the amount of water that could be reused. “Although the mine’s initial plan included the upgrading of the old works, the Tecroveer plant at Karee has performed so optimally that this hasn’t been necessary,” says Cronje. “Aside from the process efficiencies, another contributing factor is that our plant designs are conservative and can actually handle much higher loads when needed.”Wonderkop
The success of this project led to Tecroveer being awarded the turnkey contract for the design and operation of a new 9 Mℓ/day plant for Lonmin at its Wonderkop site within the Marikana complex. Commissioned in 2010, Wonderkop provides the dual benefit of treating the mine’s wastewater as well as sewage effluent from the local community. This single Tecroveer plant was built to replace five redundant treatment works within the Wonderkop area. It currently treats around 6 Mℓ/day, with clean water recycled back to the mine’s reuse dams for downstream industrial and irrigation applications. All operations are fully automated, monitored and controlled via Scada systems.Unique technologies
Common across its designs, Wonderkop and Karee have standby systems that enable around 50% of the plant to continue operating during maintenance interventions. Generators provide backup power in the event of load-shedding. A distinctive feature on these plants is that Tecroveer’s treatment processes employ biological reactors that operate without internal pumps. Internal transfer is performed by Tecroveer’s patented Transfer Mixer technology. “The Tecroveer Transfer Mixer has been applied on more than 20 project sites since 2002, and revolutionises process performance by combining mixing and high-volume, low-pressure pumping. The advantages include the elimination of pumps for recycle flows, lower power consumption, a non-clog design, higher return rates, as well as improved process performance resulting from the low-speed, non-shear and anoxic pumping,” Cronje explains. The plug-flow design of Tecroveer’s vertical aerators allows for the control of the anoxic and aerobic zone through variable-speed drives. Aeration is proportional to organic loading into the plant, further improving overall energy efficiency. In turn, Tecroveer’s patented Petro process is designed to reduce the energy and reactor volume requirements of the activated sludge system. These systems, in combination, ensure stringent effluent discharge standards.Sludge
Handling the resulting sludge by-product is then the final phase in the process, with Wonderkop serving as the central facility for all the mine’s treatment plants. “The composting methods employed, with or without bulking agents, have a number of potential beneficial applications,” says Cronje. Waste-activated sludge is dewatered using Tecroveer’s Multi-disc screw press for dewatering and then mixed with garden waste to produce compost. The reliability and operational cost-effectiveness are far superior to conventional dewatering technologies, as the equipment has no wearing/tearing belts and moving parts. This final product is then used by the mine to promote vegetation growth during the rehabilitation of its tailing dams.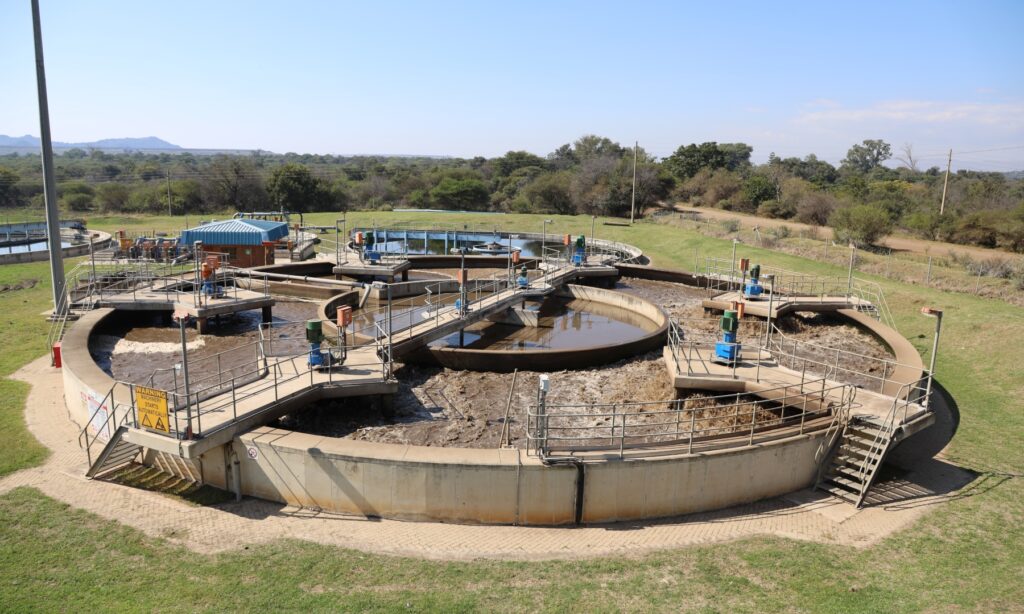
Package plants
Alongside Sibanye-Stillwater’s large-scale treatment works is a Becon Watertech package plant (with a capacity of 30-100 kℓ/day) installed at the mining group’s nearby game farm, which also serves as a conference and training centre. A sister company to Tecroveer, Becon Watertech’s Be-Pac range (from around 15-500 kℓ) is locally produced and meets smaller-scale wastewater treatment requirements for a wide spectrum of users – from schools to housing developments. A notable feature of these units, which are modular and scalable, is their Rotating Biological Contactor (RBC) filter system, based on a proven technology developed in Germany in the late 1800s. These RBC units need minimal operational input and control, with a single gearbox driving the rotor. “In the past 12 years, we’ve achieved close to a 99% compliance record for all eight treatment plants previously owned by Lonmin and now forming part of Sibanye-Stillwater’s Marikana operations,” says Cronje. “And, during this period, there have been no additions or changes to the original Tecroveer processes, and no downtime, which underscores the success of our design methodology. “We’re especially proud of our Green Drop and Blue Drop performance across every site where we operate in South Africa and our role in delivering the highest process standards for our private and public sector clients,” adds Cronje. “Given the right technology and experience, close to 100% compliance is definitely achievable,” Cronje concludes.