With trenchless construction, a pipe, duct or cable can be installed underground without disturbing service structures such as roads, pavements, driveways, buildings or ecologically sensitive areas. IMIESA speaks to Rocky Herrmann, MD of Rolkon Trenchless Construction, about his company’s unique offering for the underground infrastructure industry.
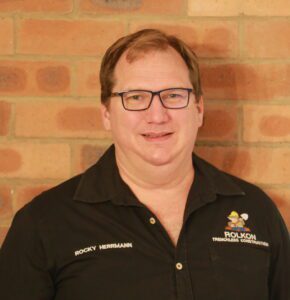
HDD is used to install underground pipelines for gas, sewer, water and stormwater, fibre-optic sleeving and electrical sleeving. We own five machines – a D6, two D9s, a D20 and a D36 – as well as moling machines, ground-penetrating radars and magnetic scanners, along with support equipment like a truck, trailer, water carts and tooling.
Are there any common misconceptions that you encounter regarding trenchless technologies? Quite a few municipalities and engineers have successfully adopted this technology, but other municipalities and engineers have little understanding of it. I think it’s important to educate and remind everyone of what is possible with trenchless technologies. Furthermore, trenchless construction is often viewed as a costly option and the pricing of these projects can be problematic. Cost savings across the entire trenchless construction project must be calculated.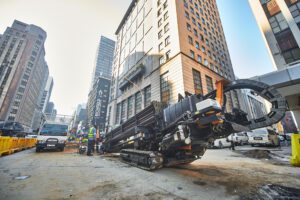
- Environmental sensitivity: By using specialised equipment, underground infrastructure is installed, repaired or replaced with minimum disturbance to the ecology. This approach means that infrastructure can be fitted under buildings, forests, wetlands and bodies of water. No plants or trees need to be removed, which results in less environmental impact. Due to its non-invasive manner, very little rehabilitation is required after using trenchless construction methods.
- Minimal disruption: With open-cut excavation methods, the excavation site must be isolated and may require blocking off entire roads and rerouting the traffic. This significantly disrupts day-to-day activities and leads to traffic jams, people running late for work, or delayed medical and other emergency assistance. With trenchless technology, little or no excavation takes place. This means fewer street closures and traffic disruption.
- Saves time: With decreased disturbance, projects using trenchless methods take less time to complete. Less time means less inconvenience associated with a construction project.
- Added value: Studies on HDD projects have shown that trenchless construction can result in 30% more value for money on a given project.
- Less cost: The cost savings resulting from the application of this technology can be significant. Trenchless technologies minimise damage done to surrounding areas. Money is also saved by avoiding the relocation of utilities and the slowing down of traffic (commerce).
- Skill development and labour: In South Africa, trenching is viewed as a job creator when, in truth, more trenches are dug mechanically than by hand; where labour is used, it is predominantly unskilled. Trenchless technology uses skilled labour and thus growing the trenchless industry will positively increase the resource pool of skilled labour, which, in turn, results in higher wages.
- Safety – there is no risk of the trench collapsing.

- Basement drilling job (Durban Town Centre): Despite building rubble in the confined space in the building, a drill was piloted from the ground floor into the basement, welded a 160 mm diameter pipe and a pulled in a new sleeve.
- Water main (Empuluzi): Rolkon worked for Bloc Contractors where several water main sleeves were installed in various locations. Ground conditions varied from hot and dry to soft and muddy.
- Fibre sleeve (Cape Town): Working with the Azile Group to pull new fibre ducting for a new fibre network in Gugulethu and Kayalitsha, Rolkon managed to pull between 100 m and 200 m of 110 mm fibre ducting per week.
- Traffic signals (Midway Mall): The Rolkon team spent the better part of the drill pounding through the rock-hard surface of the ground to find soil conditions conducive to pulling ducts for the traffic signals outside the Midway Mall in Newlands. And although the drill took longer than expected, all the crossings were completed as planned. The length of the drill was 75 m, with two 110 mm ducts pulled to ensure the effective functioning of the new traffic signals.
- Sewer sleeze (Sizela): A 400 mm sewer sleeve for a new sewer line was built by Bloc Contractors. During this 30 m drill, Rolkon had to cross the main road and navigate around and below a playground and a wetland area. Additional complexity was brought about by the soft ground conditions and clay soil.
- Water main (King Shaka International Airport): This was an unplanned but urgent job for the Rolkon team, where an 18 m long, 315 mm diameter uPVC water main had to be installed under the road at the airport. The main had to be pushed and not pulled through the drill hole, which took some extra focus in terms of guiding.