The Coegakop Biofiltration Plant is nearing completion and is designed to treat groundwater rich in dissolved iron and manganese. The plant is designed with a capacity to treat up to 20 Mℓ/day of potable water for Nelson Mandela Bay Municipality (NMBM).
By Kirsten Kelly
This is the fourth and final phase of the Coegakop Wellfield project – part of the NMBM Water Master Plan to augment municipal water supply. “Groundwater is being used in the fight against the worst drought in Nelson Mandela Bay’s recorded history. NMBM conducted groundwater investigations during the 2010/11 Eastern Cape drought, and it was found that some properties owned by NMBM had a high groundwater potential. One of the most favourable areas for developing a wellfield was located at the foot of Coegakop. The wellfield site was therefore named the Coegakop Wellfield,” says Matthew Hills, civil engineer: Water & Sanitation Subdirectorate, NMBM.Phases | Description of work | Timeframe | Estimated cost | Drought funding | Status |
One | Groundwater source identification | 2010 – 2013 | R11 500 000 | R0 | Complete |
Two | Drilling of exploration and probe boreholes | 2013 – 2015 | R23 000 000 | R0 | Complete |
Three | Drilling of production boreholes and pipelines | 2015 – 2018 | R55 500 000 | MDG R19 998 483.85 | Complete |
Four | Construction of treatment works | 2017 – 2023 | R309 700 000 | MDRG R23 444 064.63 | Construction |
TOTAL | R399 700 000 | R43 432 548 |
Biofiltration
Biofiltration refers to the process whereby organic bacteria grown in the filter beds aid in the removal of dissolved minerals. “The Coegakop WTW uses biofiltration technology because it is an affordable, efficient, sustainable and reliable treatment solution with low maintenance costs. The normal filtration process requires the use of more chemicals, so this approach reduces our operational cost and is also better for the environment,” explains Hills. Preekstoel Plant in Hermanus is the only other filtration plant of this kind in the country, but it treats 10 Mℓ/day, as opposed to the 20 Mℓ/day treatment capacity of the Coegekop WTW. Once complete, the Coegakop WTW will be the largest biofiltration plant of its kind in South Africa, and possibly the most ambitious biological manganese removal plant in the world (treating high concentrations up to 2.5 mg/ℓ). Hills adds that the cost per kilolitre of water is less than other treated water within NMBM because it is being sourced straight out of the ground. “The numbers still need to be verified. However, once the plant is fully operational, NMBM is confident that Coegakop will supply the lowest cost per kilolitre of water within the NMBM water supply system. Aside from the iron and manganese elements, the water is pristine and characterised by low levels of salinity.” Besides the water purification, there are no additional bulk transfer costs, since the treated water goes straight to the existing Coegakop reservoir approximately 650 m away. From there, distribution pipelines supply Motherwell, the Coega SEZ and an expanding consumer zone. “Having a second source of water supplying the Coega SEZ is essential for investor confidence and will unlock the potential for further development and job creation,” says Matthews.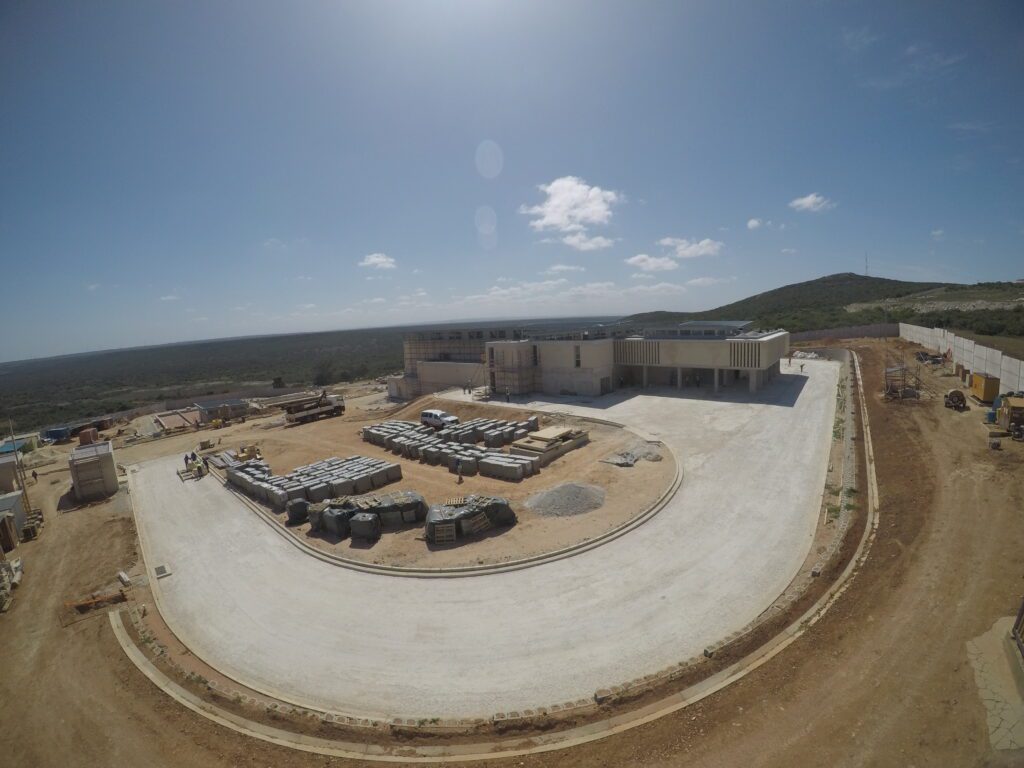
Digitalisation
Automated control and instrumentation systems will ensure that the treatment process operates effectively and that the process controllers can monitor all activities centrally. Automated reporting will be generated, assisting with compliance reporting. This is primarily done through a SCADA system. “NMBM is refining its ability to operate plants remotely as well as record, view and manage data. With the drought, the balance between water demand versus available supply is precarious and we need to react rapidly to any changes within this system. Adopting a modern SCADA system is a huge step in the right direction towards achieving an optimised, efficient and reliable water supply system,” explains Hills.He adds that digitising an entire water supply system (let alone a WTW) is a lengthy process.
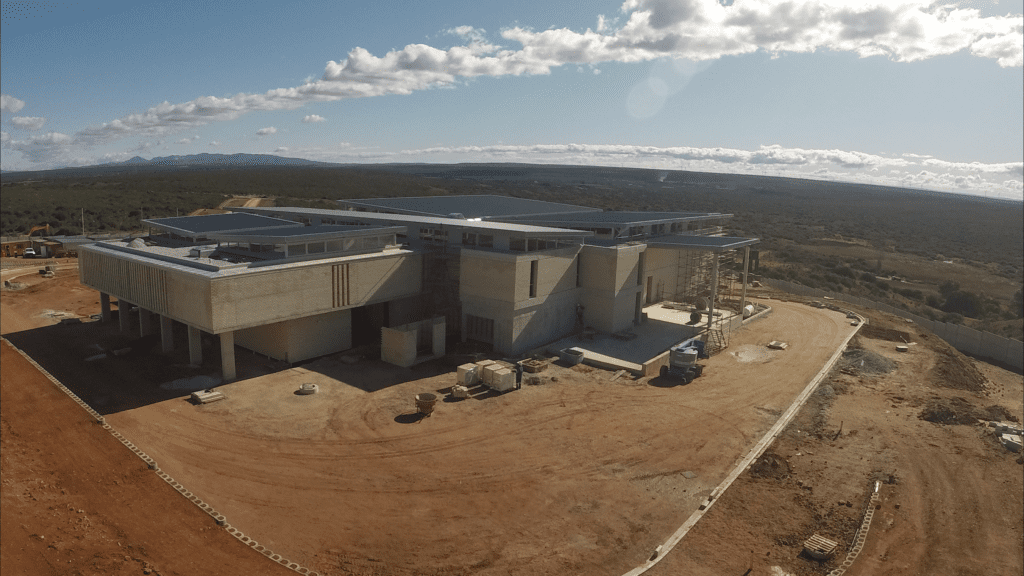
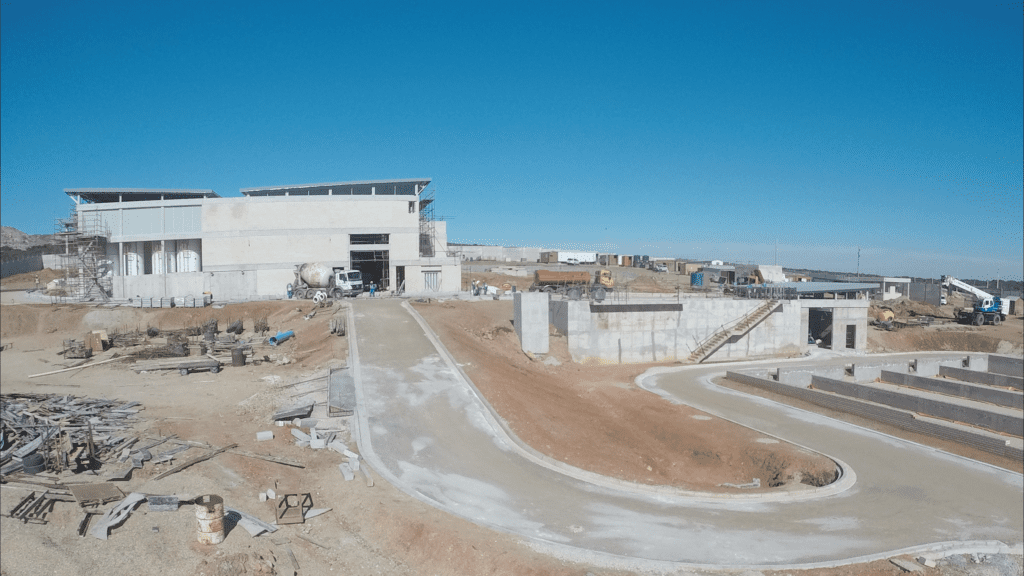
Operator-centric design
Architecturally, the design of the Coegakop WTW revolves around ease of circulation, putting the people who operate the works at the centre of the design concept. The WTW building was also designed to prioritise the security, safety, comfort, ergonomics, accessibility and work experience of the operators. “First, most of the treatment processes and equipment, as well as the control room, laboratory, offices and operators’ facilities were in a single building. The operators could view all major equipment from a single, easily accessible position, right outside the control room,” says Smit. He goes on the state that this created a challenge, as it is easier for designers and the construction team to be able to work on components individually. “The operator-centric approach resulted in a complex, integrated and dense design that combined interrelated treatment processes and equipment, sophisticated control systems, multiple foundation platforms, multistorey/water-retaining structures, all in a single building under one roof.” It drove the development of a special layout with the aim to assist process controllers by configuring equipment in a logical way, enabling effective control of each system. This was achieved by locating related equipment close together and ensuring clear visibility for processes that require monitoring. For instance, the upper filter gallery is visible from the control room, while the machine room is visible from both levels of the filter gallery. The design also facilitated simple circulation for normal routes taken by process controllers by minimising level changes, providing multiple routes within the building and limiting the need for exposure to wind or rain. This plant is a good example of human-centric design, valuing personnel.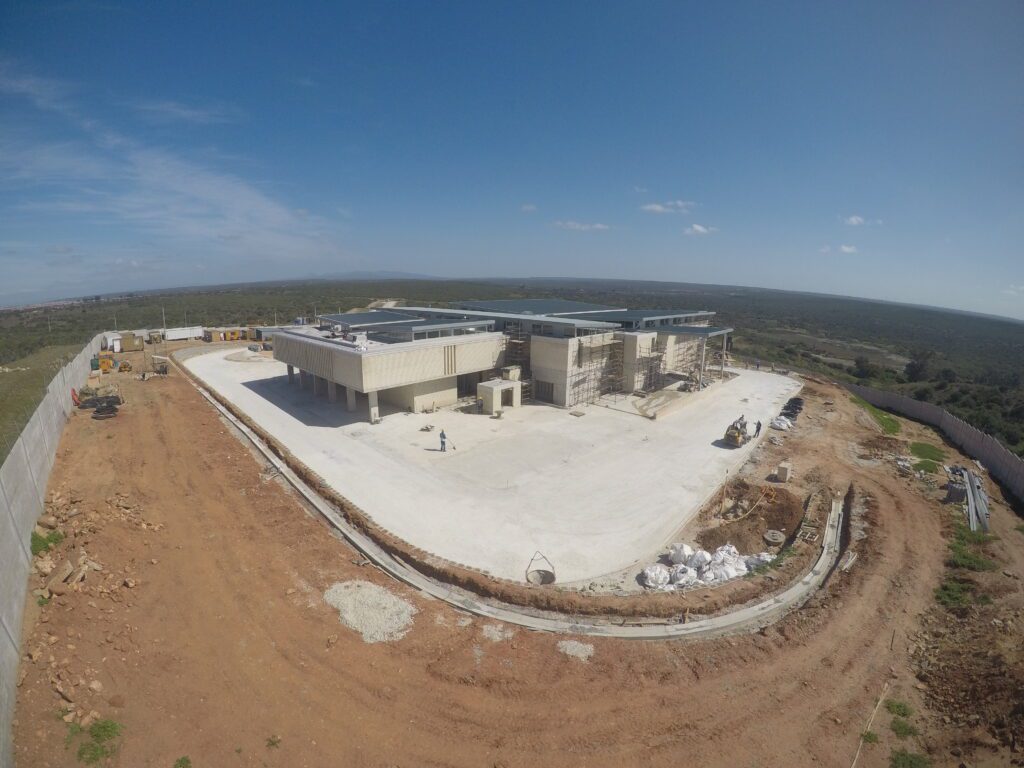
Virtual reality
3D modelling was used as a design collaboration tool for the various engineering and architectural disciplines, which was later built into the virtual reality (VR) and augmented reality (AR) software. “We used VR to serve three main functions on this project:- It instils confidence in the client regarding the design of the WTW. They get a personal sense of the plant, which is difficult to achieve from looking at 2D drawings, or a scaled model.
- It helps a lot to detect design clashes (civil, mechanical, electrical, services) and to optimise the spatial layout. The spatial design becomes tangible and instinctive, allowing the designers to grasp the relative size and positioning of equipment at a human scale. This helps us simulate the operator’s everyday working experience (Will pipes be in the way? Will they be able to reach certain valves? Does a room really need to be so big?).
- It develops a virtual operation and maintenance/training simulator for future plant operators who can practice various operating scenarios or protocols in a safe, offline environment,” states Smit.
- ensure adequate allowance for maintenance, dismantling, access, overhead lifting
- allow for improvements in constructability considerations
- aid the construction team in their planning and envisaging of the required product
- present the project to those providing funding.