Celebrating its 17th anniversary in June 2023, Gabion Baskets has grown its base as a specialist manufacturer and solutions provider of gabion systems to become a market leader in South Africa, alongside steady export penetration into Africa.
IMIESA speaks to managing director Louis Cheyne about this amazing success story, founded on a track record for innovation. An ancient technique perfected over the centuries for civil engineering works and military applications, the simple gabion has come a long way. Essentially rock-filled baskets, each assembled in either square, rectangular or other geometrical shapes, they come together to form an interconnected system. Typical applications include mass gravity embankment stabilisation, flood control and riverbank protection. “Early renditions dating back to the Middle Ages show that a form of gabions was used for fortification works using wickerwork as the frame. From the late 19th century, the modern age has reinterpreted this with the use of advanced wire systems designed to optimise strength and maximise longevity in environmentally engineered applications,” Cheyne explains.Engineering versus architecture
Founded in 2006 and headquartered in Johannesburg, Gabion Baskets provides holistic solutions in the multifaceted field of gabion systems. This capability encompasses manufacturing, design service recommendations, on-site installation training, project and programme management, and product development in distinct fields that encompass civil and environmental engineering, and architecture. The key distinction between the two fields is the application environment, which has a direct bearing on the wire systems employed. For engineering works, such as bridge abutment protection, mass gravity retaining walls, weirs and river works, the standard specification internationally is the employment of Class A galvanised double-twisted hexagonal mesh wire, with or without a PVC/PE coating. This is used to form box gabion, gabion mattress and allied products such as sausage gabions. Rock-filled gabions typically have an approximately 30-35% void ratio that enables a degree of permeability and inherent flexibility. In turn, architectural applications – which include building cladding, landscaping, freestanding feature walls and interior design elements – employ square welded mesh panel systems, which are supplied in a standard 3 mm or 4 mm diameter Class A wire specification. Among its distinctive features are the precise tolerances that can be achieved, with perfectly flat faces. “However, architectural trends we’ve seen in Europe include the extensive use of curved welded panel extensions and bending of mesh at corners to follow structural contours or where joining is necessary,” says Cheyne. Welded mesh, while robust, is not intended for engineered roles, being too rigid in terms of composition. This compares to hexagonal woven wire mesh systems, which have exceptionally high tensile strength and are purpose-designed for flexibility. Flexibility is especially vital in submerged riverine environments where gabion systems need to cope with varying water velocity, as well as scenarios like debris impact, pollution and abrasion. Here, a welded mesh structure would fail prematurely. “It’s never a one-size-fits-all solution. Every site has its unique design requirements based on factors like the underlying geology and hydrology,” Cheyne continues. “You must factor in the chain reaction (cause and effect) and take a systems approach. For example, a stormwater management intervention must take into account impacts on neighbouring properties, communities and structures. Without due consideration, you might fix the problem in one spot, but exacerbate it by increasing downstream flows and the potential for flood damage on adjoining properties.”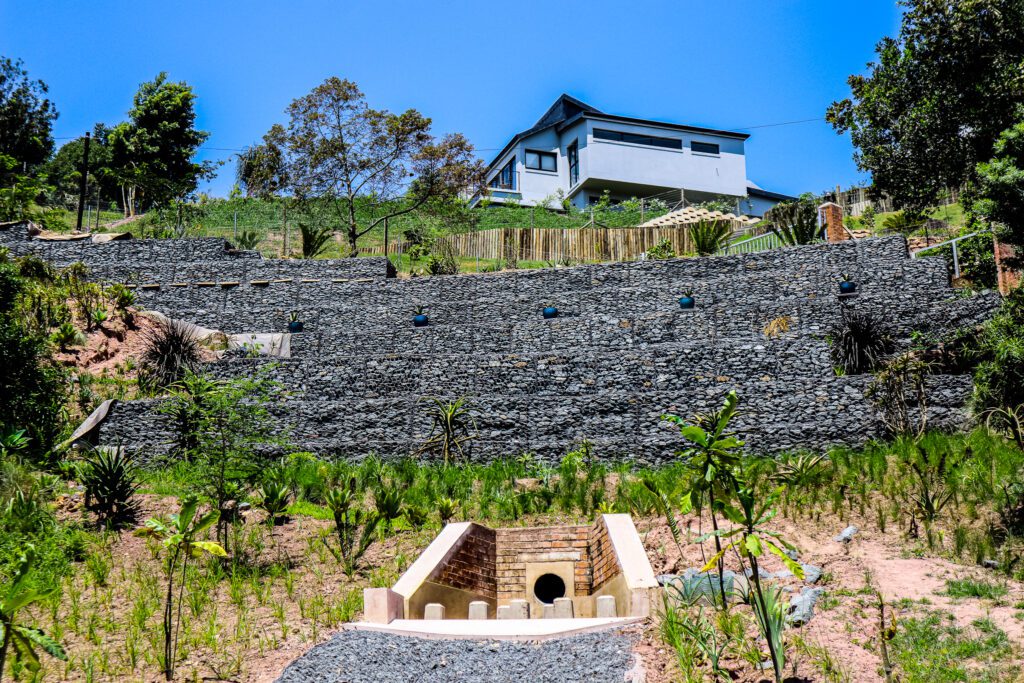
Product research and development
Gabion Baskets constantly researches market trends locally and internationally to see where it can further refine its product offering to optimise performance and durability. In this respect, during Q1 2023, Gabion Baskets will be making the shift from PVC to polyethylene (PE) coatings on its wire mesh products. These new wire coatings will be supplied by a Gabion Baskets Group company that is also responsible for the in-house production of its wire and welded mesh lines. PVC wire coatings are employed globally as an extra layer of protection in highly corrosive applications that include marine projects, such as tidal erosion countermeasures, beach protection and rivers.“PVC performs this job admirably, and can be offered in a range of colours, like tan and grey, to add an aesthetic effect. We’re now taking this level of protection a step further with the introduction of a PE coating. Latter benefits include greater resistance to cracking and hardening over time,” Cheyne explains.
From Q3 2023, Gabion Baskets will also be supplying the market with the option of Galfan-coated wire produced via its group company, as part of a local content strategy. Galfan wire features a special zinc-aluminium alloy coating that provides greater corrosion resistance. Another parallel development is the introduction of Gabion Baskets’ Associated Product Line to support SMME contractors. Examples include hog ring guns, hog ring clips, PPE and wheelbarrows. “Wheelbarrows are one of those basic, universal items on-site. However, our research showed that standard versions tended to be unsuitable for gabion works. Our version has a more robust and balanced design well suited for transporting rocks. Key features include longer guide handles for better leverage and control, and a larger front wheel to cope with varied terrain,” says Cheyne.Factory modernisation
To keep pace with increasing production volumes at its Johannesburg factory, Gabion Baskets has invested in high levels of mechanisation to streamline fabrication processes, along with ongoing skills development programmes. In the factory, traditional steel wire lacing of gabion panels has now been replaced by the use of pneumatic hog ring gun clips that speed up the manufacturing process and achieve a neater finish. The same technique is now also being used on-site for gabion basket and mattress assembly, thus achieving a much stronger panel-to-panel and basket-to-basket connection. “We now have dedicated production lines for woven mesh and welded mesh, respectively, each housed in their own dedicated buildings at our Johannesburg facility,” Cheyne explains. “This enables us to produce standard or custom products separately without affecting our main and common lines.”African growth markets
Major growth across South Africa on key projects runs in parallel with export market opportunities within Southern Africa, as well as further afield on the continent. Recent orders within the SADC region include two riverbank reinstatement and erosion protection projects for private properties bordering the Zambezi River in Zambia. These comprise the Musango Project, where a 300 m wall was constructed and completed in February 2022; and the Lolebezi Project, entailing the installation of a 500 m wall, which is currently ongoing. In both instances, Gabion Baskets provided design recommendations, on-site training, and PVC coated woven mesh river embankment systems. Gabion Baskets is also receiving a growing number of enquiries from South African contractors working across Africa. Alongside this are orders from governmental clients that include the Botswana Defense Force, where some 500 gabion barriers were manufactured and supplied for its African Union mission in northern Mozambique. The product is similar to the European Hesco bastion. These barriers are simple to assemble. Essentially, they are made up of interconnected fabric-lined welded mesh wire cages that can be filled quickly with any in situ material, like soil and rock. The concept borrows from the military fortification concept of old but takes it to a new level for ballistic protection. Another plus is that these barriers can also be rapidly deployed as flood mitigation measures.The quest for excellence
“Our success to date has been based on our people. They truly are our biggest asset. It’s the engine room that drives us to innovate and add value by constantly refining our products and processes,” adds Cheyne. “Given the environmental priorities, there’s huge demand for wire mesh systems, particularly in rivers. In parallel, our architectural clients are increasingly opting for welded mesh for interior and exterior design elements that harness the natural beauty of stone. By thinking out of the box, we continue to lead the market with fit-for-purpose solutions, in the process creating many opportunities for labour-intensive works on sites,” Cheyne concludes.