With extensive mining activities taking place in the area, Rustenburg Local Municipality faces numerous water challenges, where water is pumped as far as Vaalkop Dam on the Crocodile River System. Fortunately, the construction of the Mafenya Pumping Station and pipeline to Tlhabane Reservoir will assist with bulk water supply.
By Kirsten Kelly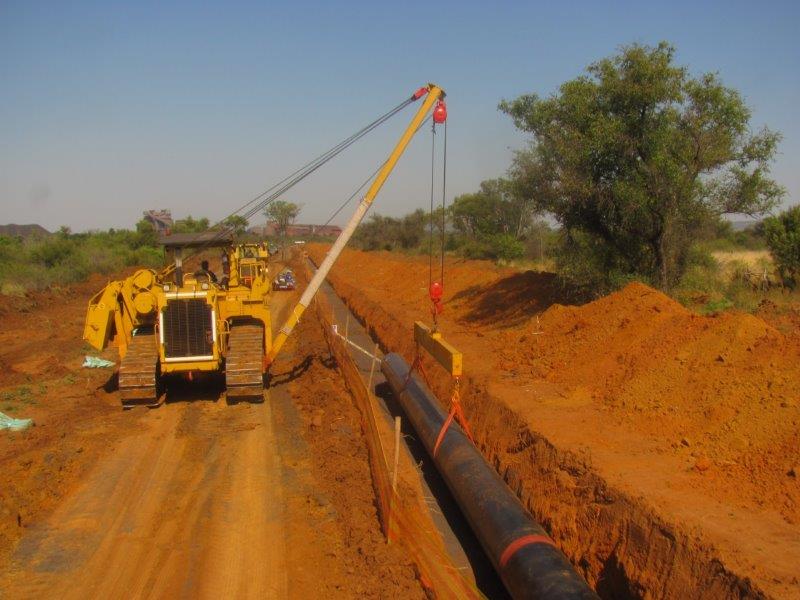
Professional team
Client | Magalies Water |
Consulting engineer | MwB |
Concrete supplier | Rustcrete |
Pipeline | Murray & Dickson Construction |
Pipe supplier | Hall Longmore |
“M&D has a core value, namely Khula Nathi – isiZulu for ‘grow with us’. As a family company, we have developed a strong, loyal and dedicated team over the years. It is via our Khula Nathi value that M&D has always been able to work well with communities located within our project footprints. This ability is becoming increasingly important and one of the reasons that we remain a preferred pipeline contractor for municipalities and waterboards,” explains Donald Davies, site agent, M&D. The project comprises 28 km of steel pipeline (914 mm in diameter). Trenches are 2.5 m deep and 1.7 m wide. There are 13 valve chambers within the first 14 km of the pipelines as well as a number of pipe-jackings under a railway line. The company is also constructing the Mafenya Pumping Station (comprising three pumps) that will pump water to Tlhabane Reservoir. All support walls and support columns are structural concrete, with the roof being precast concrete slabs. The vandal-proof door is also concrete.
Delays
Davies explains that, initially, there were some project delays with regard to gaining access to the site due community unrest. “This was problematic because steel pipe manufacturer Hall Longmore makes delivery of the pipes on an agreed-upon date. The project must therefore stay within its deadlines, as Hall Longmore is unable to store the pipes if there is a delay. As the pipes are delivered, ideally the clearing and grubbing must be completed so that a team can string them out. The handling and transport of the pipes are critical. We have taken delivery of pipes already, and have unfortunately had to stockpile them because we could not initially get access to certain areas before we gained buy-in from the local community. This means that the pipes need to be uplifted from where they are stored and transported before they can be laid in trenches, adding additional time and expense to the project.” Fortunately, M&D has been able to make up for some lost time. “This is due to, first, having an experienced, technical team. Furthermore, our pipe fittings factory enables us to accelerate the manufacture of steel pipeline bends and fittings for our projects. Notably, it was the first such facility to be certified to ISO 3834 quality standards by the South African Institute of Welding. Furthermore, my team has quick access to 180 different critical plant and equipment items via M&D’s Plant Division, including pipelayers, excavators, welding machines and a fuel dispensing machine that can monitor fuel consumption of plant equipment individually through tags,” says Davies.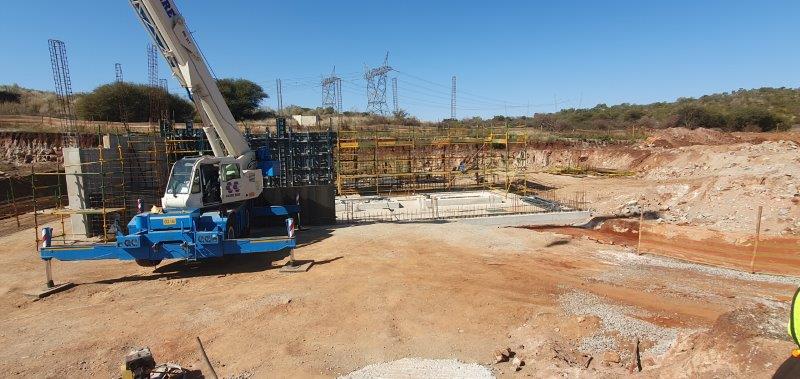
Community Engagement
Lehlohonolo Mabe, senior quantity surveyor, M&D, whose family is from the Rustenburg/Phokeng area, has been a great help in assisting with community discussions, together with the social facilitator William Nkuna from Diphororo Development. “We have also met with the area’s police commissioner for advice as to how to deal with any community members that are preventing the work from continue on-site,” states Davies. “A total of 33% of the contract work is awarded to SMMEs within the area. They have been allocated work like the bedding operations and the concrete structures for the valve chambers. M&D is also assisting two local N6 Civil Technicians with work experience and training,” he adds. Davies believes that a key factor in the success of the project is assimilating the SMMEs and local community members into the M&D team and work culture. “We even have a ‘pipeline soccer team’ and a ‘pumping station soccer team’ that play against each other – and local community members play in both teams. It helps to bring everyone together in an informal setting.” Important partnerships have also been formed with Bakubung Platinum Mine and Glencore Platinum Smelter at BosHoek. M&D utilises Bakubung’s haul road to get to the site establishment. Furthermore, a pipeline is being installed along part of the road. M&D Construction is also working closely with Glencore in implementing a cut and pull through the Boshoek to Rasimone Road. A diversion road is needed so that construction does not affect Glencore’s operations. Representatives from the mines have attended toolbox talks and have met with the M&D team where they were provided with a traffic management plan, scope of works, risk assessments and method statements. In turn, the mine representatives could also offer input regarding the volume of trucks on the road as well as any environmental and safety concerns. “We have even used a waste product from the platinum mines as bedding material. The quality is good and it is easy to compact,” explains Davies. Most of material along the pipeline route has been easily excavated, but some rock has been drilled and blasted from Mafenya Reservoir to the R565 road. Davies adds that many pipeline projects require access to privately owned land and it is vital that the pipeline contractor has a good rapport with the local community. “We need to communicate with everyone involved and acknowledge all stakeholders.”
Quality
M&D supervises all SMME work to ensure that everything meets quality standards. Its team comprises highly competent and experienced welders who are all certified by the American Petroleum Institute. Once the pipe has been lifted down into the trench, it is tack welded. Lead welders will complete the inside welds while back welders complete the outside welds. All pipe welds as well as the pipe wrapping are subjected to third-party inspections. Welding on pipelines is highly specialised; because the pipe cannot move, the welder must work around it. In the inside of the pipeline, joints are shot blasted and then coated. A holiday detector is used to find holes in the coating. Cathodic protection has been used to prevent corrosion. A considerable length of the pipeline lies parallel to a railway line, it was found that the electrical field increases whenever a train travels past the pipeline. “Quality control plays a vital role in ensuring that the pipeline passes the pressure test at the end of the project. If a weld is overlooked and not tested – and there is a pipe burst or leak during the pressure test – a significant amount of time and money must be spent on locating the source of the problem, fixing the weld, wrapping the pipe, fixing the inside coating and then using more water to do another pressure test,” says Davies.Safety and the environment
M&D has always endeavoured to complete its projects in a manner that ensures the safety of its employees as well as fellow contractors and to a quality standard that guarantees the satisfaction of the client. The company boasts ISO 9001, ISO 14001, ISO 45001, ISO 3834 and ISO 27001 certifications. This current project has a dedicated environmental officer and team of safety officers. Daily toolbox talks are held, and the environmental manager also holds talks as needed on water resources, stockpiling of topsoil, as well as managing waste and recycling. Quality managers have an opportunity to talk on maintaining high standards of construction and workmanship. For safety reasons, trenches have been barricaded. A moil from an air compressor is driven into clay with an 8 lbs hammer, then removed, and a wooden stake is placed into the hole along with high-visibility netting. “Through employing the best people that we can find and giving them the best possible resources to perform the job, we are entrusted with technically complex projects like this,” concludes Davies.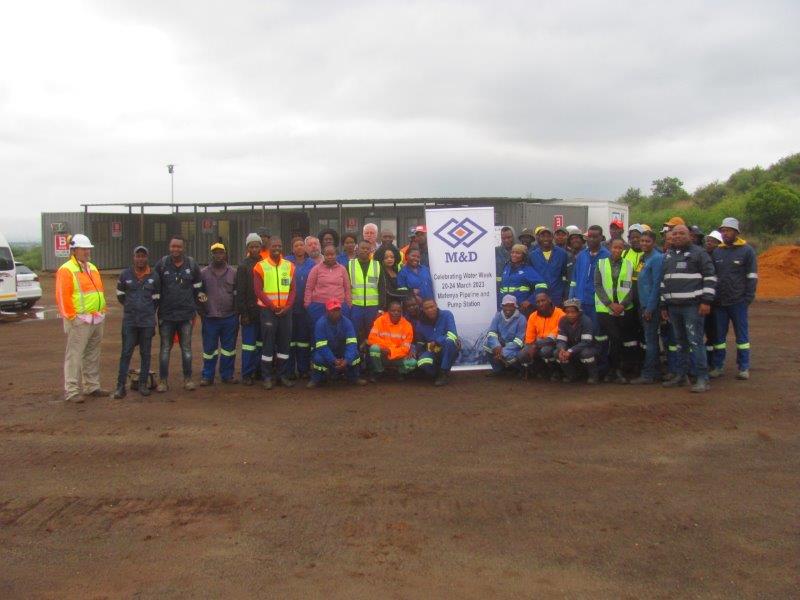
Pilanesberg Bulk Water Supply Scheme
Phase 1 | Construction of Tlhabane Reservoir |
Phase 2 | Construction of Mafenya to Tlhabane bulk water pipeline mainly of steel pipes to withstand high pressure in the system; construction of the Mafenya Pumping Station |
Phase 3 | Offtake from Phokeng to supply water to Maubu/Seron Reservoir including pump station and command reservoir |
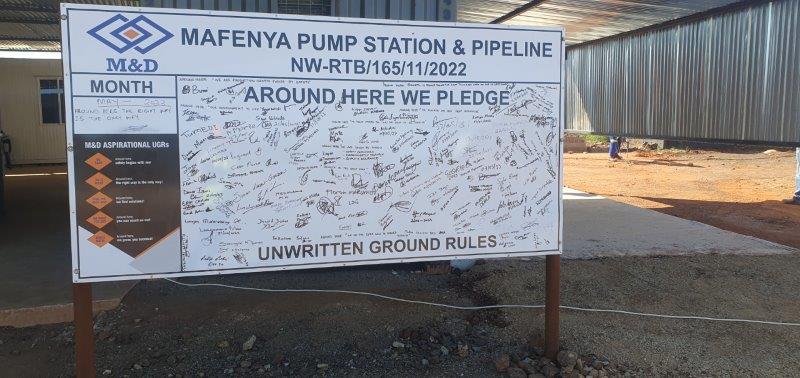
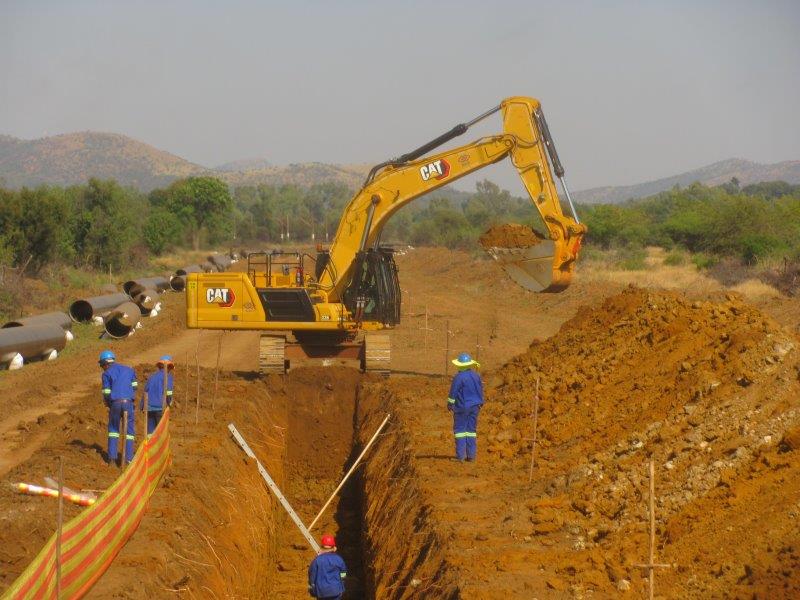
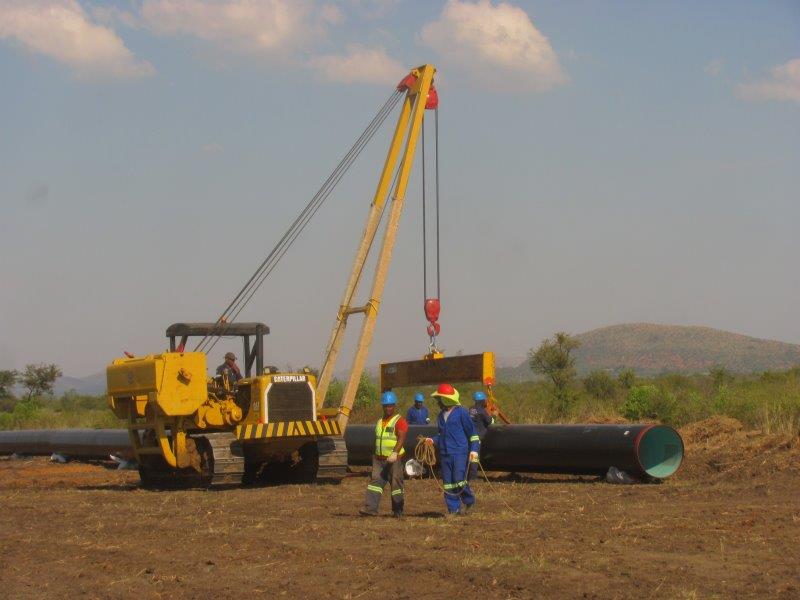
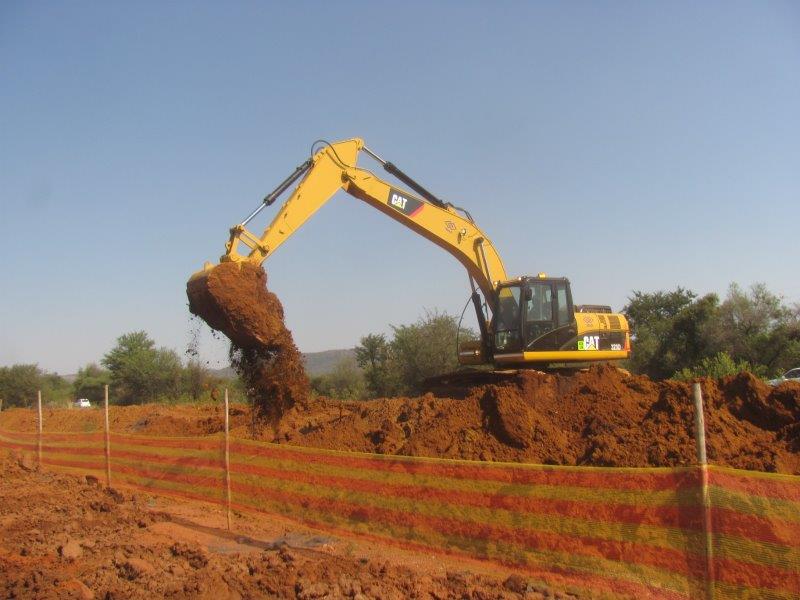
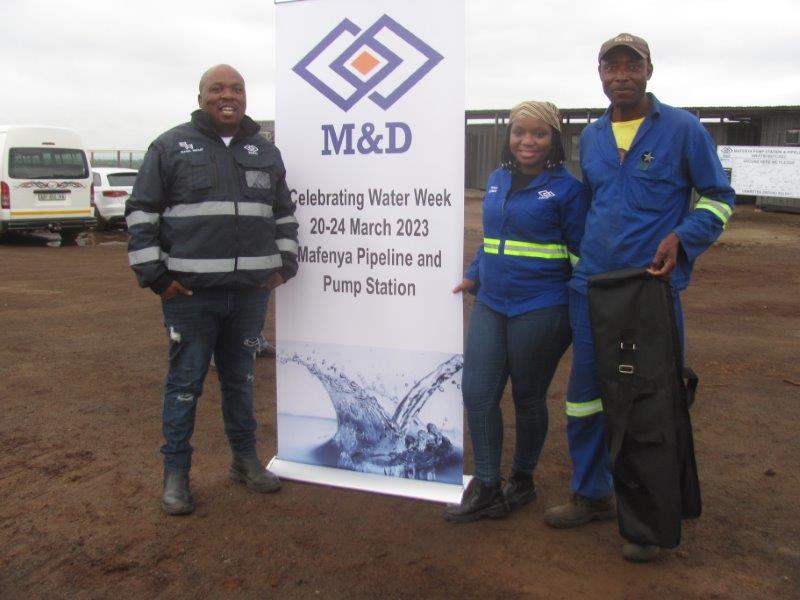
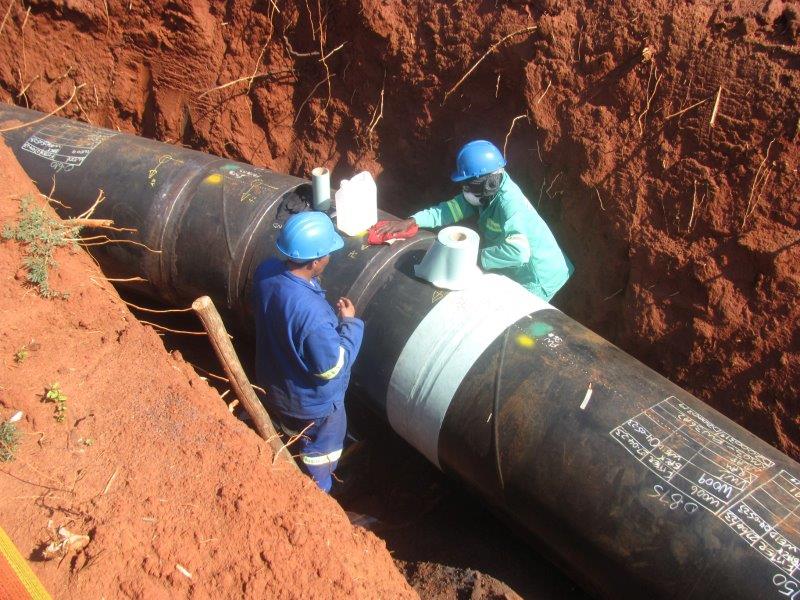
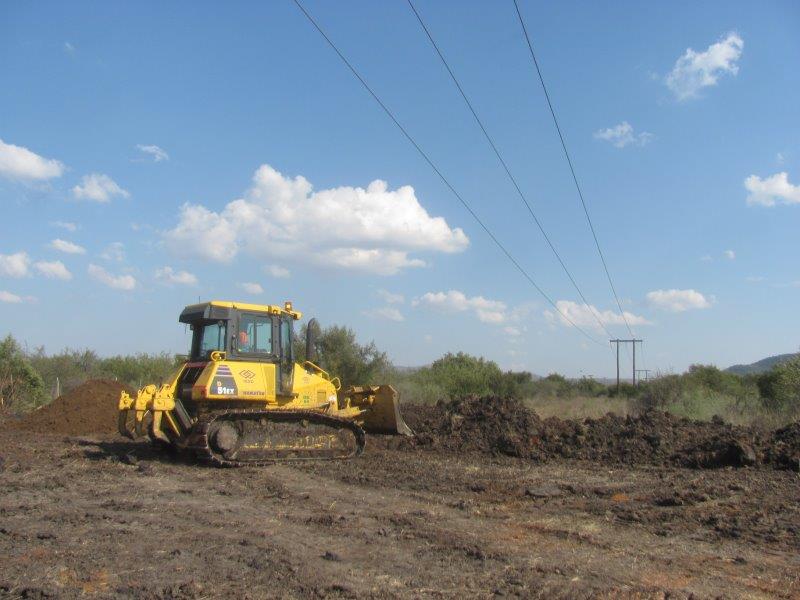
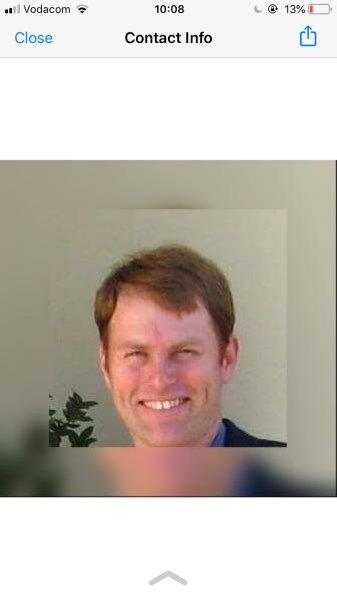
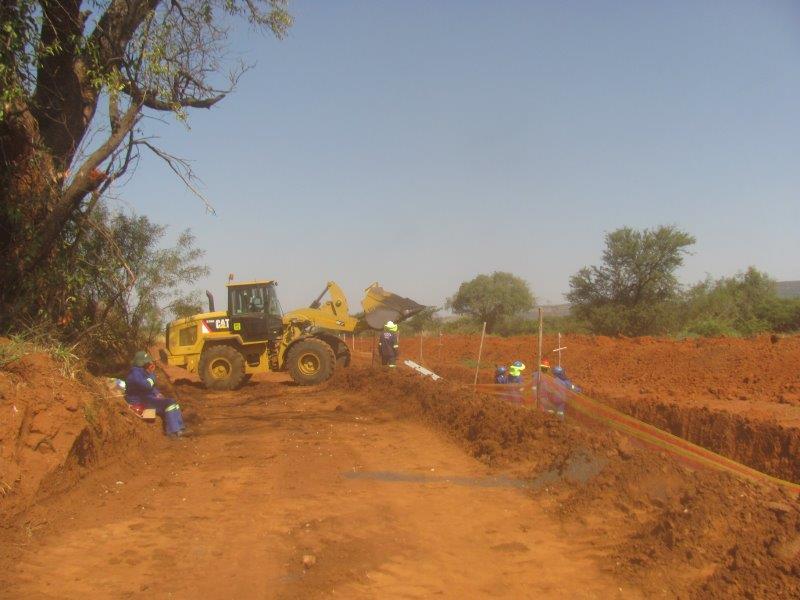
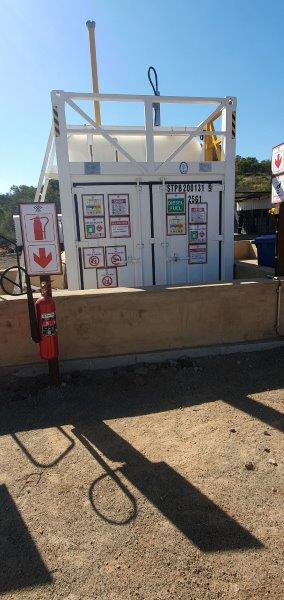
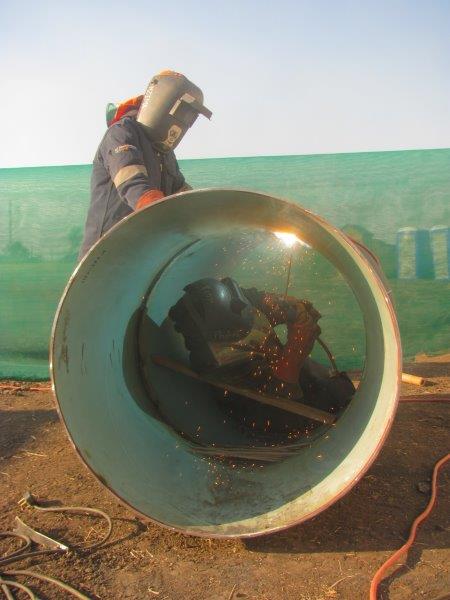
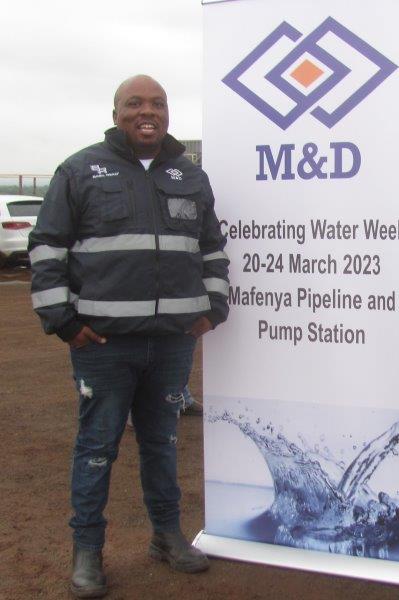