The structure comprises three sections or “rotations” consisting of columns that are connected to that portion of the spiral beam.
The City of Ekurhuleni’s (CEMM) Water and Sanitation Department successfully completed the construction of four prefabricated reservoirs using cutting-edge precast concrete technology.
In addition to these four new reservoirs, the CEMM is building a new water tower which will be completed in late 2024. This tower will be almost entirely prefabricated, excluding only the floor slab and foundation. Upon completion this tower, standing at 36m with a capacity of 2.5 Ml, will be the first pre-cast concrete water tower in Africa.Why precast
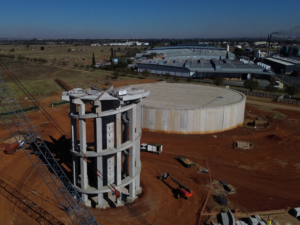
The superstructure consists of 12 tapered beams connected to the columns of the last rotation
How it all comes together
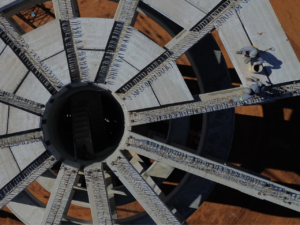
precast concrete water tower _Resting on bearing pads, the 12 tapered beams will carry and distribute the load of the precast-concrete tank and its contents
Then there are the 15 prefabricated elements that make up the 3,6m-diameter shaft, which is constructed at the same time as the outer portion of the structure. Equipped with precast concrete stairwells with balustrades, it leads to the underside of the prefabricated tank. Thereafter, the shaft connects with stacked precast concrete pipes equipped with a cat ladder. Cast into the reservoir floor slab, this top portion of the shaft will traverse through the water-retaining structure to a manhole on the roof.
The superstructure consists of 12 tapered beams connected to the columns of the last rotation. Resting on bearing pads, they will carry and distribute the load of the precast concrete tank and its contents. Installed in the triangular-shaped junctions between the tapered beams, cut-to-size and shape hollow-core slabs serve as the shutter for the in-situ foundation for the water-retaining structure. Coping panels have been installed along the perimeter providing an aesthetically pleasing finish. The floor slab has to be made on-site and is not prefabricated, so Corestuc locally sourced four sub-contractors to handle the job. The slab will be 35cm thick and use a total of 103 m3 of concrete. The slab has to withstand the heavy reinforcement of the beam junctions so the concrete has to be managed carefully to ensure it is compacted correctly, while also being watertight. An articulated boom lift has already been placed on top of the superstructure to assist with the installation, as well as the grouting of the 34 tank wall panels. This is in addition to the two buttress panels for post-tensioning, which will be undertaken in the same way as all of Corestruc’s other reservoirs. All of the wall panels will be propped during their installation. Conventionally, only the first wall panel is propped to free up space. Meanwhile, the roof structure consists of four columns and beams and 150 hollow-core slabs. The centre portion or “core” will be constructed first, and the outer section completed last. Meyer van Rooyen, a Corestruc Project Manager, who has supervised all precast-concrete work thus far, says that there is very little scope for error on this project.“We have achieved tight 15mm tolerances throughout the construction of the three rotations of the substructure, starting with the placement of the first-rotation columns on the in-situ foundation. Among other factors, this is also facilitated by our precise manufacturing processes. Each element undergoes extensive quality assurance before it is dispatched and again once it has arrived on site. Once the elements have been safely transported to the site and as the last component in Corestruc’s precast-concrete value chain, the responsibility rests with my team of riggers to maintain the highest levels of productivity, efficiency and accuracy.”His team is supported by a 150-ton mobile crane. The 12 tapered beams, for example, each weigh a staggering 18.5 tonnes and the columns for the second and third rotations slightly less. Precast concrete structures require high-accuracy construction and Corestruc has invested in robotic total stationing to achieve the levels of accuracy needed. The structure demonstrates both precast and cast-in-place techniques. “Supporting this water tower is a 1m-thick and 25m diameter foundation consisting of 500m2 of 30MPa cast-in-place reinforced concrete. It is underpinned by 200m2 of mass concrete blinding. This took 10 hours to place, starting at 5h00 and using two concrete pumps, while also isolating an entire ready-mix concrete plant just for this purpose,” says Van Rooyen. Safety is the number one concern on any construction site, and since construction jobs like this are relatively new this project had a height safety specialist on-site to assist with safety protocol as well as provide specialist training to the team.