Over the years, the HDGASA has evolved to the point where it plays multiple roles, acting not only as a voice and lobbyist for the industry but also as a hub of technical knowledge, advice and support.
The Hot Dip Galvanizers Association of Southern Africa (HDGASA) plays an important role in supporting the energy value chain – which spans clean, renewable and green energy – as it powers towards key sustainability targets, according to Executive Director, Robin Clarke.
After a nine year ‘teething period’, during which key energy sector stakeholders and local galvanizers found common ground, he says hot dip galvanizing is now the preferred corrosion control mechanism for this sector, enabling substantial return on investment for energy infrastructure projects and the industry as a whole.“As an Association, we support the move to renewable energy. We are pleased that the sector has embraced hot dip galvanizing. What we do prolongs the life of the most essential element – steel,” Clarke points out.
Part of the transition
According to the International Trade Administration, 85 percent – or 42,000MW – of South Africa’s electricity is generated via coal-fired power stations. Coal will continue to provide most of the country’s power for the next decade, although the share from renewables is expected to develop faster than the market. Clarke says that the HDGASA has always fostered a close, constructive relationship with Eskom: “As an association, we have advised the parastatal regarding corrosion control of transmission lines and distribution equipment – and the relevant standards – over the past several decades. We expect this to continue with the 14 000 kilometres of transmission lines due to be provided under Eskom’s strategic development programme.”The solar learning curve
This started with a rush to complete photovoltaic installations built according to generic European specifications in the Northern Cape. Solar installations grew on the back of load shedding: “They were scattered across the length and the breadth of the country. We ran into headwinds related to corrosive environments that had not been factored into the original generic designs intended for the Northern Cape,” Clarke explains. It has taken time for stakeholders to replace generic specifications with site- and location-specific alternatives. This means pre-approving a quality plan before accepting a design, to ensure that the corrosion control needed for each installation is correctly specified to meet the service life requirements. For example, a solar installation on the West Coast requires a different thought process and specification to an identical facility in Kakamas in the Northern Cape.“We began working very hard as an Association to interface with key players to ensure that this was done – and that a thorough environmental assessment was completed to ensure that the specifications for corrosion control and the selection of the materials were correct,” Clarke advises.Although this initially applied to large solar farms, it soon extended to far smaller installations on the roofs of commercial buildings such as shopping malls. “We have been advising commercial property groups to not only correctly determine the corrosion control specifications for individual solar installations, but also to assess the baseline corrosion condition of the roof and the roof sheeting – on top of which PV panel installations will be installed. These roofs are predominantly galvanized or duplex-coated galvanized substrates. As such, the roofs need to have a service life equal to – or exceeding – that of the renewable energy installation, to ensure acceptable projected return-on-investment and sustainability targets,” he explains.
Bridging the gap
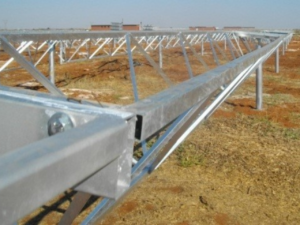