A spectacular vision is gradually becoming reality in Cadarache in the south of France. Modelled on the sun, the International Thermonuclear Experimental Reactor (ITER) fusion system uses nuclear fusion to generate energy in order to secure humanity’s supply of electricity. One of the biggest challenges is the high temperature inside the reactor. Technology by Sauer Compressors is a key factor in cooling the reactor: the manufacturer has supplied the world’s largest system for helium recovery.
The ITER fusion reactor is an international consortium project involving the European Union, the United States, Russia, China, Japan, South Korea and India. The reactor is scheduled to be put into operation in 2020, with the aim of harnessing nuclear fusion – the sun’s source of energy – under terrestrial conditions as well. The hydrogen isotopes deuterium and tritium melt and form a plasma when exposed to immense heat. This process releases large quantities of energy. Researchers hope this will provide an infinite source of energy, one that is entirely emission-free and safe. Proof of concept has been demonstrated. However, up until now heating the plasma to the ignition temperature of around 100 million °C has required a greater input of energy than could be recovered from subsequent fusion. The ITER test system has a tokamak-type fusion reactor. At 840 m3 its capacity is far greater than that of other systems of its kind. The reactor is designed to generate ten times the energy needed to ignite the plasma. These immense temperatures prevent the enclosure of fusion plasma in physical vessels. Instead, the system uses gigantic magnetic fields to confine the suspended fuel in thermal insulation and to keep it away from the boundary walls.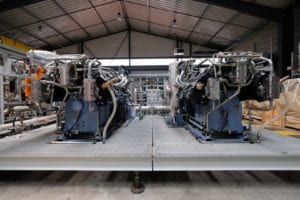
Sauer Compressors built the WP6305 BasSealHe-B-type helium compressor as a bespoke solution for the ITER application. © Sauer Compressors
Minimising helium consumption
A large volume of highly pressurised helium and an input temperature of 4.5 K are used to cool the superconductive magnetic coils that generate the required magnetic field. However, due to its particular diffusibility the inert gas is a demanding coolant. Helium possesses a very small atomic radius and can pass through even the tiniest openings and pores in metals and screw connections. Since the inert gas is very expensive, loss due to evaporation or leakage must be kept as low as possible. The planners behind the ITER fusion reactor therefore requested a system to recover the gas that evaporated during the cooling process. An additional system for compressing leakages in the helium loop was to be installed as well.Sauer Compressors was the world’s only provider with the ability to meet the project’s demanding requirements. Both systems were manufactured and tested by the Sauer experts in Kiel, Germany. The merging of the two happened at the assembly hall of French company Girodin-Sauer SAS: There, both systems were combined and assembled to form a single unit, consisting of five helium compressors on a four-part base frame measuring 8 x 8 meters – the largest assembly of its kind. The entirely gas-tight recovery system with stainless steel tubing was then dispatched to the customer Air Liquide. Installation on the ITER fusion reactor began in summer 2017.