An industry pioneer since 1924, Hall Longmore’s commitment to research and development continues to refine its class leadership in the steel pipe sector. IMIESA speaks to Kenny van Rooyen, managing director, and Callum Storar, contract sales manager, about the key role of steel in service delivery.
Worldwide, steel remains the mainstream choice for bulk water conveyance, just as it did some 150 years ago, which underscores the performance benefits of this material to handle sustained high pressure rating requirements and variables like hydraulic shocks. The introduction of advanced welding techniques in the 1920s presented a major breakthrough for steel pipeline integrity, further entrenching their place as the standard for water boards globally. Over time, the coating systems employed to combat corrosion and extend their lifespan have also improved significantly. The general benchmark in the modern-day steel pipe manufacturing sector is to provide a 40- to 50-year design life once installed and subject to the fluids being transferred, such as water, wastewater, oil or gas. However, in Hall Longmore’s case, a number of their systems in the bulk water and mining sector have lasted for close to 100 years. Examples can still be seen in operation on some West Rand mines in Johannesburg. Vital catalysts “Pipelines are often the unsung heroes in the infrastructure supply chain. However, they are essential catalysts for socio-economic growth, and the foundation for all current and future town and city master plans in terms of projected water demand – and we’re proud of our role as a manufacturer in engineering enduring infrastructure solutions,” says Van Rooyen. “Steel pipes are futureproof, locally sourced and cost competitive. Plus, they also help to minimise non-revenue technical water losses due to their robust composition. They are also climate-change resilient in the sense that steel pipes tend to withstand extreme weather, as was the case during the severe floods that hit Durban and surrounds in 2022. Once commissioned, it’s virtually impossible to pull steel pipe sections that have been welded together apart,” Van Rooyen continues. “From our perspective, steel is the answer. However, to make a sound business case, it’s important for municipal and water engineers to clearly understand the place and the designed performance characteristics for all alternative pipe materials available on the market, whether it’s GRP, plastic or concrete. Asset owners need to factor in the life-cycle cost and obtain the best possible return on investment for any product, technology or system employed. New contractors entering the market also need to be well informed.” Examples of areas where steel pipe tends to outperform other materials include their ability to cope well with live and dead loads when installed under roads, in dolomitic conditions where subsidence is a risk factor, and in hilly terrain where there’s a greater risk of water hammer. Widest possible choice Meeting the requirements of the bulk supply reticulation market, Hall Longmore manufactures medium-pressure pipes designed to operate within the 16 to 40 bar range, which makes them highly scalable in terms of current and future water demand coupled with network upgrades. “What makes Hall Longmore unique in South Africa is that we produce pipe sections in the broadest possible spectrum in terms of diameters and wall thickness options,” explains Storar. Manufacturing falls into two key categories, namely electric resistance welded (ERW) steel pipe and helical (commonly, but incorrectly, referred to as spiral) welded steel pipe, using the submerged arc-welding process (SAW). Hall Longmore’s standard OD range for ERW is from 219 mm (8”) to 610 mm (24”) and for SAW from 508 mm (20”) to 2 540 mm (100”). However, the nature of the helical process allows for bespoke diameters compatible to clients’ existing infrastructure. “This manufacturing flexibility enables us to supply a complete town or city network, from the initial bulk infrastructure to the progressive phasing in of the distribution infrastructure to meet ongoing residential and industrial expansion,” says Storar. Outside the water market, Hall Longmore manufactures what are referred to as ‘oil country tubular goods’ (OCTG) pipes for the local and global petroleum and gas market. OCTG pipes must meet, and in some cases exceed, the requirements of the American Petroleum Institute (API) standards, considered among the strictest in the world for any sector. For these installations, there’s zero margin tolerated for ruptures, leakages or environmental disasters. “Clearly, this means that Hall Longmore’s quality control (QC) has to be world-class,” says Storar. To further refine its QC processes, Hall Longmore recently invested in the latest automated radiographic testing (RT) technology. As per international standards, steel pipe manufacturers are mandated to employ RT technology for non-destructive testing on submerged arc welds. The key difference now is that Hall Longmore has switched from analogue to digital X-ray techniques, which are far more precise. CoatingsSelecting the right pipe diameter and wall thickness is essential for optimum network performance, as is the selection of the right corrosion protection method. Cathodic protection (CP) is common and it’s recommended that any proposed new installation be reviewed by a CP specialist.
As Storar points out, the internal and/or external coating system specified should always be determined following a detailed investigation by the client of the in-situ conditions. Factors to consider include the resistivity of the soil, as well as overhead powerlines and railway lines that emit AC or DC currents that may need to be countered cathodically. “Hall Longmore is an industry leader in the technology and application of protective coatings and linings to steel pipes,” Storar explains, adding that the applications are tailored to suit the needs of specialist corrosion engineers. Hall Longmore has the widest range of accepted pipeline coating and lining systems in the South African context. These include polymer-modified bitumen (PMB), fusion-bonded medium-density polyethylene (MDPE), three-layer polyethylene (3LPE) and rigid polyethylene (RPu) for exterior protection to underground pipelines subjected to highly corrosive conditions, and various liquid epoxy as well as cement mortar/concrete internally linings. The latter is a preferred lining medium for smaller-diameter (less than 610 mm) potable water services due to its ability to be reinstated at the joints without man access.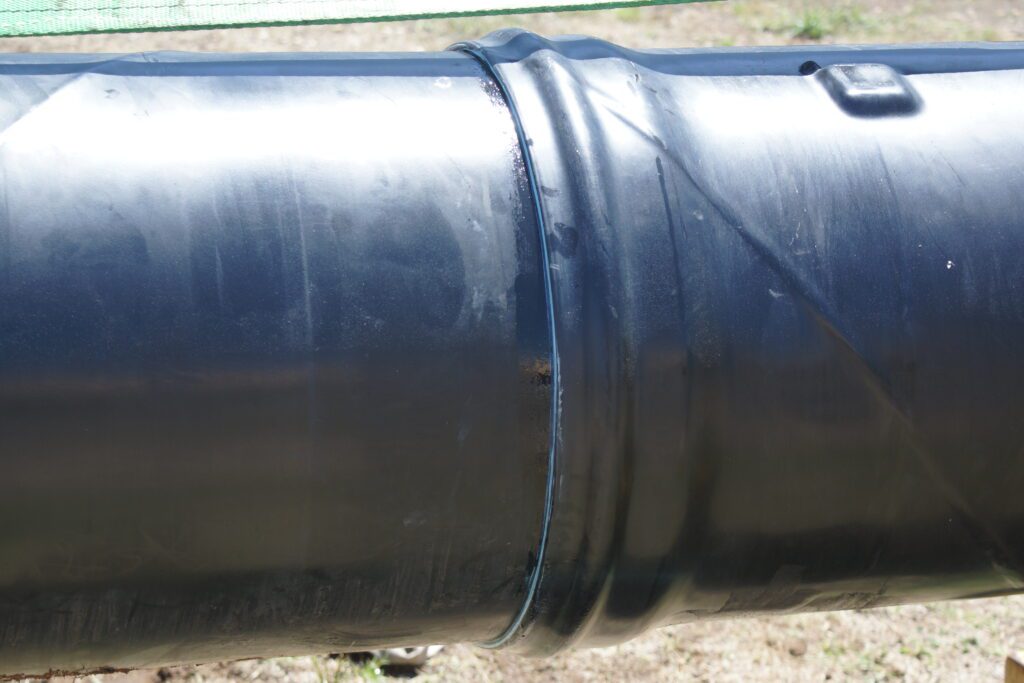
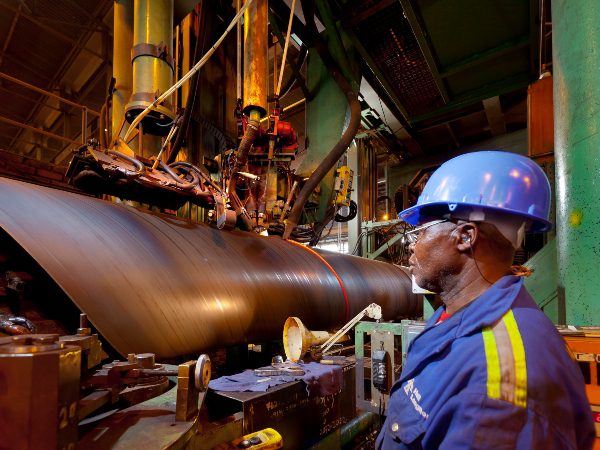
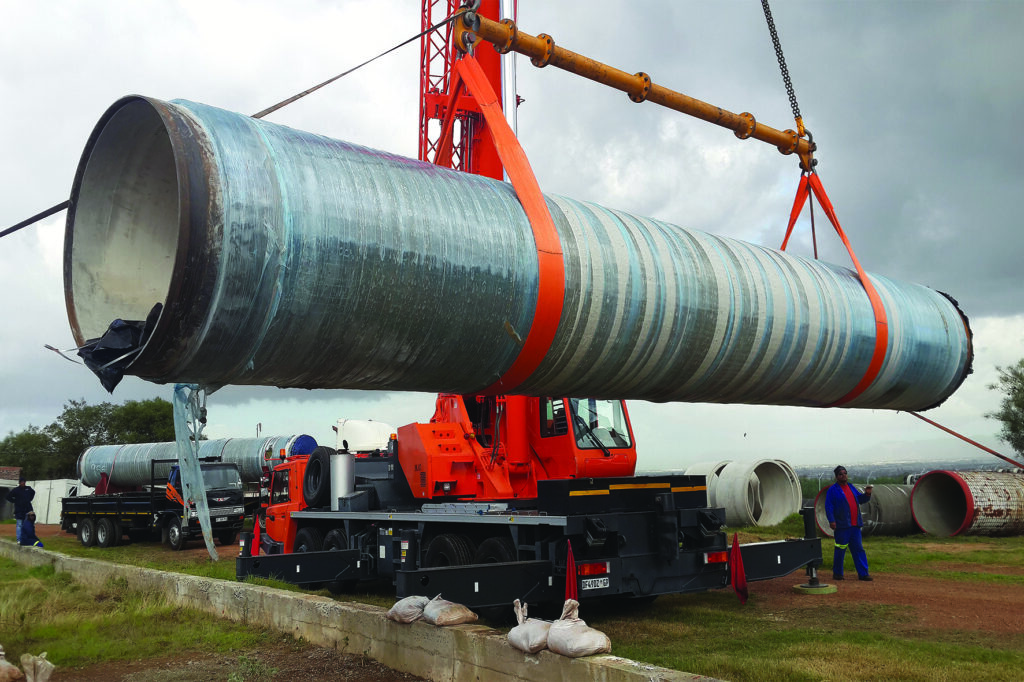