As we observe #WorldEarthDay on 22 April 2024, Alison Groves, Director: Discipline Lead: Built Ecology, WSP in Africa and John Rammutla, Principal Associate: Highways, WSP in Africa, examine the theme “Planet vs Plastics” – and the role of circular economy thinking in managing plastic waste towards a NetZero future.
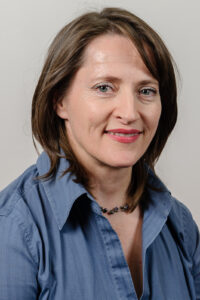
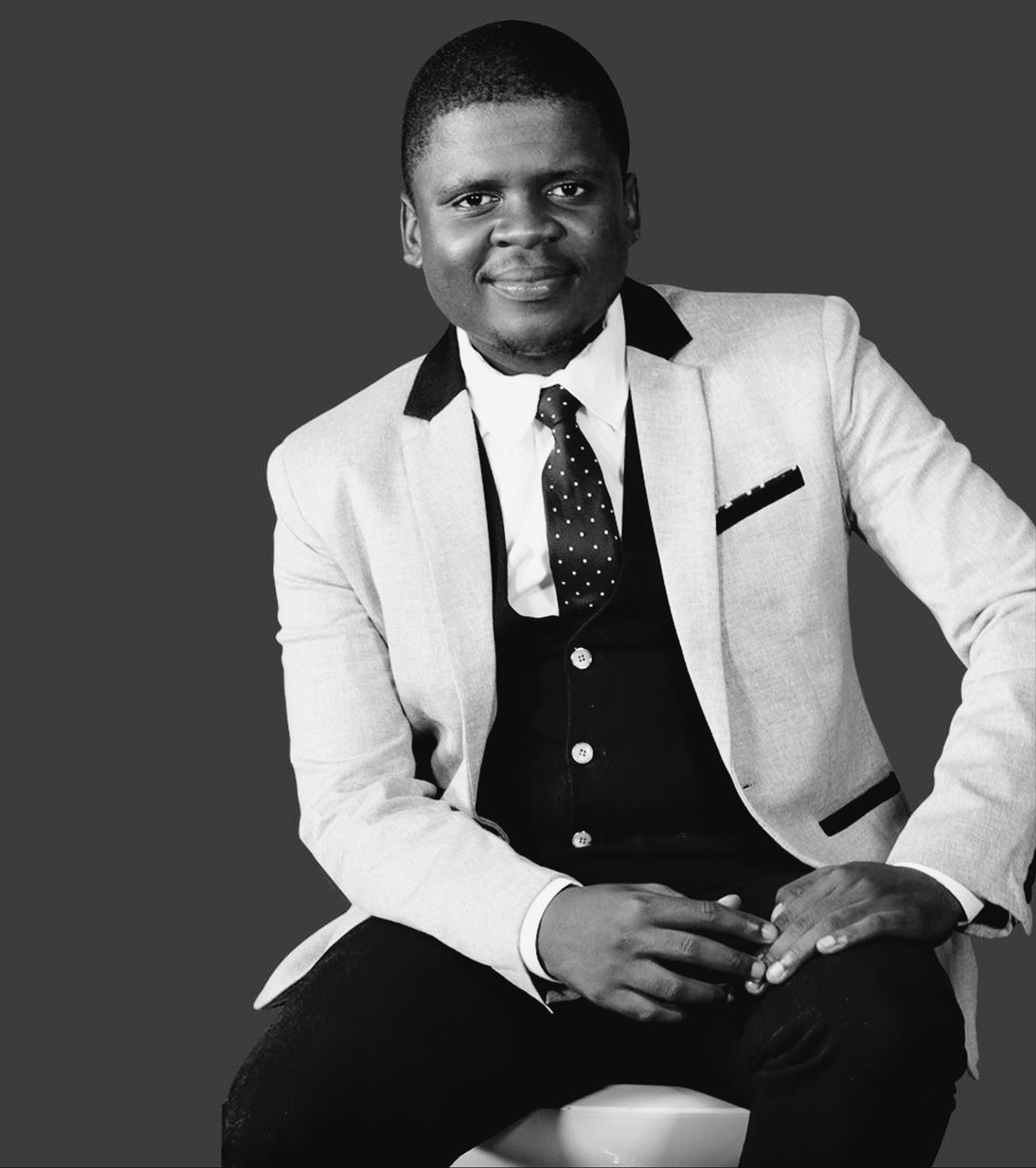
Currently, the asphalt used for the surfacing of roads locally comprises 20% to 25% recycled materials. But we can do more, Rammutla says. “Innovative materials can replace traditional carbon intense materials. Asphalt can often be replaced with recycled plastics or rubber from recycled tyres.”
Groves says replacing carbon-intensive construction materials in buildings with low carbon alternatives can also play a key role in reducing the construction industry’s overall carbon emissions and waste contributions. Steel can be replaced with fibre-reinforced plastic or polymers, or even carbon fibre and graphene, under the right circumstances. But not all plastic is equally easy to recycle and converting it for reuse in a more sustainable form isn’t an all-encompassing solution. Plastic to energy There is another way of dealing with plastic: burning it. In Scandinavia, waste-to-energy (WtE) plants incinerate high-energy residual waste, including nonrecyclable plastic along with other high-energy wastes such as timber and wood products. The heat is used to generate electricity and to warm water for local district heating systems, reducing the need to burn virgin fossil fuel for power and preventing a wide range of plastics from going to landfill. They do not end up in the environment, and the volume of waste is vastly reduced. “The exhaust from these plants is well treated so most of what exits the chimney is water vapour,” Rammutla explains. “The residual slag is pretty nasty stuff though, and the waste from the scrubbing also contains high concentrations of hazardous substances.” Unpleasant though these residues are, they are at least relatively small in volume, and there is some value in concentrating them so that they can be disposed of appropriately in specialised landfill. “New technologies are also putting some of these wastes to use,” Rammutla continues, “for example, in new types of concrete where the toxic chemicals can be fixed and rendered harmless.” Could WtE be considered as part of the solution to meet South Africa’s energy requirements as it moves away from coal-fired power stations? According to the latest available statistics, South Africa generates approximately 122 million tonnes of waste per year, of which only 10% is recycled or recovered for other uses. This leaves at least 90% of the country’s waste entering landfills or worse – being dumped illegally. “We certainly seem to be producing enough waste to burn,” Groves says. “Though there are probably more cost-effective ways to deal with our energy and our waste challenges at this stage, WtE is an initiative worth monitoring for potential local applications in the future. Should we explore it, it would be wise to prioritise low-grade, contaminated plastic that can’t be recycled into more useful products. This would help to clean up our landscape and prevent these kinds of waste ending up, ultimately, in the environment. WtE is one way to give some value to plastic and ensure that it is collected and removed.” “Supporting our clients in reducing their waste and emissions remains a primary objective of our work. We believe that employing our Future Ready® approach and circular economy thinking throughout our project delivery process has the potential to make a significant contribution to decarbonisation of projects in the construction sectors,” Groves concludes. WSP in Africa is hiring! To find out more about available opportunities, check out the Careers page on our website or look out for updates on our LinkedIn page, @WSPinAfrica.