For over 36 years, Werner Pumps has been designing, manufacturing, supplying and maintaining specialist high-pressure jetting equipment, offering locally built units at competitive prices.
“We initially imported secondhand load bodies from Switzerland. After a restriction was placed on the importation of used vehicles to protect the local vehicle manufacturing industry, we then decided to import new vehicles,” explains
Sebastian Werner, MD, Werner Pumps.
With fluctuations in the Rand against major currencies and extended delivery times for imported units, the company decided to recognise the technical expertise and knowledge residing in South Africa, and they are now dedicated to local manufacturing. Their goal is to ensure all components and load bodies are made entirely in South Africa, bolstering economic growth and fostering job creation.
“Our manufactured products take the best from both worlds. We maintain the European quality standards but make adjustments to increase the robustness needed for a product that operates in Africa. It is also important that the products are easy to maintain as well as simple and efficient to operate,” adds Werner.
Werner Pumps was one of the first in the industry to obtain an
ISO9001 Certification, in October 2016. They are accredited body builders with most well-known brands.
Amanzi Recycling Unit One such example is Werner Pumps’ African-built
Amanzi Recycling Unit that repurposes the water captured when cleaning a sewer or stormwater line through an onboard filtration process. This allows for a more economical and water-conscious pumping process – creating a huge environmental advantage.
“Unlike conventional jetting and vacuuming equipment, the
Amanzi Recycler’s jetting tank has an additional recycling component. It therefore only needs to be filled with fresh water just once for the entire day’s operation. By vacuuming and reusing the same water throughout a shift, the system saves up to 165 000 ℓ of clean water during a typical shift, saving millions of litres of water a year,” states
George Jolly, Werner Pumps sales manager.
Drain cleaning, for example, requires a large quantity of high-pressure water. Standard vacuum jetting trucks that only have a jetting and suction component have jetting tanks that must be regularly refilled throughout the day.
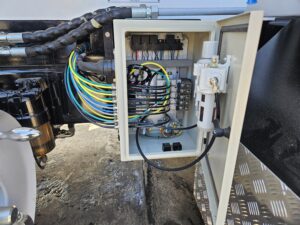
With the Amanzi Recycling Unit, the water recycling system enhances operational efficiencies by eliminating the need for the truck to repeatedly travel between the job site and a water source, meaning that significant savings in fuel, water and overall maintenance costs are achieved. The Werner Amanzi Recycling Unit also provides powerful and efficient vacuum and jetting for industrial sump cleaning, slurry management and drainage system maintenance.
Jolly explains that traditional jetting equipment requires high quality water to avoid accelerated wear of any components. But the Amanzi Recycling Unit has a specialised filtration system built within the tank super structure that separates the solids from the liquids and re-uses the same dirty water vacuumed for its jetting function.
The hydraulic operation of the vacuum and high-pressure pumps also contributes to reduced maintenance requirements, consequently reducing downtime and associated costs. The truck operates hydraulically off a split shaft unit connected to the truck’s drive shaft instead of a V-belt drive. This design ensures that the pump can be operated at low revolutions per minute, resulting in reduced fuel consumption and efficient energy use. Furthermore, the vacuum pump and high-pressure pump are above the chassis and not low to the ground, allowing the vehicle to drive in more areas.
“We have supplied several recycling trucks to contractors working in municipalities and the mining industry. They all appreciate the cost and water savings the truck offers. Furthermore, trucks can be manufactured to different sizes to suit specific client requirements, and the vacuum and jetting pumps can be customised to meet varying demands,” adds Jolly.
Improvements to the Amanzi Recycler
The original imported unit used a 270-degree boom, but Werner pumps has created a 360-degree boom, meaning that cleaning operations are not confined, and can take place in front of and behind the truck.
The trucks can be operated wirelessly, enhancing safety for operators, with a touch screen digital control panel enabling them to customise operations. The operator can work the machine from 100 metres away. This is included as standard feature with no additional charge.
Unlike the imported unit, the entire tank of the Amanzi Recycling Unit is made from stainless steel, reducing corrosion and rust damage. Hydraulic cylinders (all manufactured inhouse) are also used as a locking mechanism on the dish-end of the tank.
Werner Pumps has also designed the unit for 12-metre-deep manholes, with superior suction capabilities. The vacuum pump is fitted inside of the tank, making the entire process quieter.
“Furthermore, the tanks are designed to tip at 45 degrees to facilitate the discharge of waste. There is also a blow function where the vacuum flow can change direction into the tank, the tank is then pressurised and the waste is then force discharged out of the tank, which is far speedier option that discharging waste by tipping the tank. This also makes any clean-up process simpler and more efficient without the risk of spillage,” adds Jolly.
Maintenance 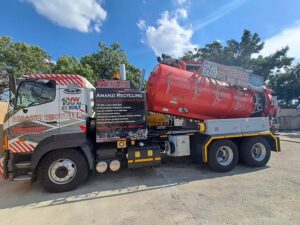
Werner Pumps have a good understanding of the performance of their equipment and are constantly looking at other improvements. This is largely due to insights from their own their rental fleet as well as the aftersales service and support to customers.
“Our customers can take a maintenance plan option. Our equipment should be serviced every 350 hours. A logbook is filled out by our customers and stamped by us once serviced. We also capture all work done on our equipment for future reference,” states Werner.
He adds that Werner Pumps has a service fleet of vehicles that can be sent out to customers in the field when there are electrical or mechanical faults. “Our technicians know our equipment inside and out as they’ve helped to put these trucks together at our factory. They do their best to diagnose and fix problems onsite, and if they can’t resolve the issue, they will assist the customer to get the truck back to our premises.”
“We do not outsource our electrical components, they are manufactured inhouse. Therefore, if there is a fault, we are the best company to fix it and it also means that we can get equipment up and running with minimal downtime,” he continues.
The decision to create a service and repair fleet is based on the company’s constant drive to solve customer’s challenges, remove frustrations and provide a one-stop shop. “We’re always asking our customers what they want and need, and then we try to deliver that. It’s one of the reasons we manufacture our equipment locally – so we can customise it to customers’ specific requirements,” says Werner.
However, all equipment is manufactured to make maintenance as easy as possible. When a company purchases any new equipment, Werner Pumps oftens train the operators to service the equipment themselves.
Werner Pumps have recently added another unit to their rental fleet. Initially, the rental fleet was used to provide a buying customer with equipment while their order was being built, but some of Werner Pumps’ customers rent equipment for a duration of a contract. According to Werner, their rentals, often produce sales once the equipment is seen in action.
“Most times, our own trained operators and assistants will drive and utilise the equipment for the duration of that contracts and their services will be included in the rental agreement. They are fully trained with regards to health and safety protocols. We also do site surveys, scope of work, risk assessments and event route plans. Health and safety is a huge priority and we design all of our equipment accordingly.”
“We believe that the reason we have repeat customers is the fact that we give our customers what they need to support their businesses,” he concludes.