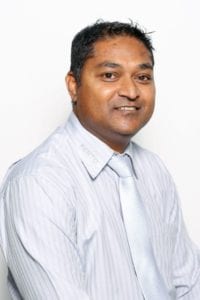
Strini Perumal, specialist: Water and Wastewater, Festo SA
Festo’s modular automation solution is being called the next evolutionary step in managing water and wastewater treatment works. Based on the development of Industry 4.0, the new technology is likely to become the new standard for water purification within the next decade. Industry 4.0 is a relatively new concept in South Africa. It refers to the fourth industrial revolution, where automation and data-exchange technologies, including machine-to-machine communication and the internet of things, lead to smart facilities that operate optimally, lowering end-user costs while also being resource efficient.
Festo’s response to this new trend has been enabled by the water treatment system known as skids. By pairing highly flexible, intelligent skids with Festo’s modular automation, plant systems can be controlled based on the “Lego principle” – a movement away from monolithic control towards a system of autonomously operating modules. This allows original equipment manufacturers (OEMs) to roll out plants faster while being more adaptable and endlessly expandable.
In addition to this, Festo also offers vendors independent, didactic training courses so that the people
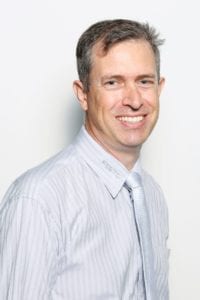
Hugo van Niekerk, business manager: Training and Consulting, Festo Didactic
behind the plants are capacitated to get the most from the new technology.
Lego principle
Strini Perumal, industry segment specialist: Water, Festo SA, explains how the system works, “Our response to Industry 4.0 is to introduce cybernetics and information technology into the monitoring and control processes in the water treatment industry, where different segments of a water treatment works (WTW) or wastewater treatment works (WWTW) are operated independently, allowing for modular automation.”
In essence, modular automation means that each process in a plant is designated as a module and operates on its own but is, at the same time, controlled from a central point via a Scada system. Each module within the plant thus forms an independent unit, which a machine manufacturer can then use to create repeatable plant configurations – a system that ultimately lowers end-user costs. “Through the implementation of the Lego principle, OEMs and machine manufacturers behind these plants can achieve the results they need and duplicate successful configuration quickly – saving time and money for their clients,” says Perumal.
“Like the Lego toy, these modules are relatively standard, meaning that pieces can be added or removed to build up or change a system as needed,” he adds.
Whether a plant is located in a rural setting or a factory environment, different processes can be selected and combined for different purposes. Some of these processes include gravity-fed filtration, ion-exchange, ultrafiltration systems, reverse osmosis systems and pump stations.
“Each one of these modular plants would have programmable logic controllers (PLCs), valves and actuators, valve terminals, pressure sensors, temperature sensors and the like. Instead of running them all through the main control room, they operate through decentralised control,” explains Perumal. “We monitor this from a central control room,” he adds.
Remote I/Os and PLCs installed in decentralised control cabinets process the electrical signals while valve terminals activate the actuators pneumatically. The process control system communicates with the control Cabinets by means of Fieldbus.
Compare this to the approach that preceded modular automation – what Festo terms the “monolithic approach”. This is the standard plant set-up of today and it offers far less flexibility. The monolithic approach offers little ability to make capacity adjustments, requiring laborious engineering processes, allowing for few upgrade options, and requiring high investment costs and long planning timelines.
Modular and intelligent
The plants of the future will consist of modules that incorporate all the automation functions it requires to carry out its own process. However, process-related modules need a small, adaptable and autonomous automation system.
By implementing decentralised, intelligent solutions in the individual modules, there is no need to reprogram and reconfigure the application software. The modules can be integrated with minimal effort into the overall automation solution for the production process. Also, less commissioning time is required, making modular automation a truly “plug-and-play” solution.
Several automated modules can be added to the plant without the need to extend the automation technology of the overall plant. It is important to be able to expand or modify plants easily without having to go immediately to large-scale plants
.Numbering up
“At Festo, we call this process ‘numbering up’, instead of scaling up, because the number of modules increases,” explains Perumal. “Coming back to the actual products that make this system possible, these include our valve terminals and the CPX platform. This is basically the central modular automation system, not only for pneumatics but also for electronics. It has IP 65/67 ratings with different variants but is also available with different controllers, with remote iOS or a number of sensors and pressure monitoring on a modular basis,” explains Perumal.
“Looking at the product itself, our CPX/MPA valve terminals, process valves, DFPD actuators and modulating valves – with smart positioning DPFI and CMSX – work together to provide a complete solution to the automation side of WTWs and WWTWs,” he adds.
Variants of skids
While, for example, pump skids, with their low level of complexity, require only a few valve slices in the pneumatic section of a CPX/MPA, filter module skids need analogue inputs and outputs for pressure monitoring. More complex modules such as a CIP skid, which comprises plant sections and containers for cleaning agents and the mixing of cleaning solutions, require further automation modules on the CPX/MPA such as analogue inputs for temperature measurement or a controller for the proportional technology.
These skids must operate autonomously and be extremely reliable. They communicate continuously with a master controller, which manages the overall system. Another advantage of the skids is that the costs for laying cables and wiring are comparatively low.
Advantages for engineering
These are not the only advantages of modular automation. For a complete process industry plant, using modules makes the engineering process faster and more cost-efficient, as there is no need to modify the entire automation concept by expanding the complete plant, but only to connect the relevant automation modules to the management system. This ensures seamless communication between the various levels of the automation pyramid.
For OEMs, the modular concept also means that it is possible to produce low volumes of uniform modules or even to produce skids for stock. As a result, they can enjoy economies of scale both in production and assembly, and reduce their costs. At the same time, the manufacturers’ ability to deliver is enhanced, allowing their end users to reach their markets more quickly with the right production quantities of new products.
Client cost savings
Cost savings associated with an Industry 4.0 system can be translated directly to customers. “Having these plug-and-play systems means the OEMs can keep skids in stock, thereby reducing costs, and can deliver to end users within faster response times. End users see these benefits and, by managing this together with didactic training courses, they gain a better understanding of intelligent monitoring systems. These systems allow users to pick up problems before they happen, lowering downtimes and keeping plants productive,” explains Perumal.
Services and training
“With regard to our services, we provide commissioning services, PLC programming, plant audits, energy tests, repairs and services, and complete customer solutions. This speaks to the total asset life cycle, from supplying to setting up stockholding. Over and above that, there’s the educational leg of the company that stands close to the industrial leg,” says Perumal.
Festo’s didactic component makes up about 15% of the company’s overall turnover – a significant portion compared to other industrial facilities that run training as a side concern.
“Our various technical training courses include topics such as pneumatics, water treatment and the water cycle,” adds Hugo van Niekerk, business manager: Training and Consulting, Festo Didactic. “We deliver our training services to the highest standards, with our portfolio combining training courses with tailor-made knowledge checks, e-learning, courseware and hands-on learning systems. We’re particularly proud of our training needs analysis; the process behind this offering is that we approach clients, determine the type of technical skills needed on their sites – assessing personnel skills gaps – and then we customise a solution. This limits time away from work and facilitates higher productivity,” Van Niekerk explains.
“Additionally, Festo is at the forefront of Industry 4.0. We’ll be rolling out courses for an Industry 4.0 qualification towards the end of next year, with the training equipment necessary to provide the courses coming into the country towards the end of this year,” he adds.
Conclusion
Festo has been involved in the water industry since 1996, and has developed its products and solutions to the point of being a leader in the field of WTW and WWTW automation. Focusing on improving efficiency for OEMs in sub-Saharan Africa, Festo’s modular automation system has enormous potential to preserve water resources, reduce project implementation timelines and reduce implementation costs in the developing, water-stressed region.
Through its response to Industry 4.0, Festo provides the right technology to enhance efficiency and productivity, supported by the development of skills, driving the business objectives of purification works.