Warehouses need sufficient staging that matches their receiving and dispatching requirements, as well as the picking system involved, says Martin Bailey.
Put simply, if you can pick faster, you’ll need less staging. Putting in automation may not necessarily be the answer. You don’t want to end up with wonderful technology, but not have enough staging. How do you solve the problem of insufficient staging? One way is to make sure there is always a truck parked in your dispatch door. You drop your trailer and pre-load the trucks. There are operations with no staging at all. Stock is picked from rolltainers and placed straight into the back of the trucks – usually at night – and it all works like a dream. Anything is possible if you have your act together. There are examples where 10 or so trucks park, get washed out and at six o’clock in the evening they start picking. The shift arrives and staff pick in reverse drop sequence by truck. They take the 10 trucks away and park another 10 and pick into those, loading about 40 trucks in total. They close the doors and then, during the day, the same doors are used for receiving. The other option is to direct load. At the Walmart warehouse I went to, they have one door per store and they throw stuff straight into the back of the trucks. Trucks are parked overnight at the store and they bring an empty one back. At one of the doors, they’d put goods straight into the back of the truck without pallets. It’s a very store-unfriendly, warehouse-friendly process. A conveyor would load the back of a truck, meaning fewer human touches. Every time you touch things, you mess it up. Still, staging can be a real mess. You can put in these highly automated systems for sortation and accuracy but still rely on an outbound process where you have to manually audit every order. The error rate, then, is about three times as high as in the pick system.
Many South African operations are a lot smaller than Walmart, particularly in some of the outlying regions. This means they usually have to have a mix of technologies and that can also create additional complexity.
Loading optimally with the route Loading needs to be linked to your staging and it’s important to integrate it with transport. It’s no use picking if you don’t integrate it with the trucks. Get the right truck, with the right unit load, and perform the right checking – or hopefully, no checking at all. Choose properly designed trucks that have been well thought out. For example, pickers should be able to walk inside the truck, from the front to the back, without having to get out when unloading. Glass windows can be installed behind the seats so that drivers can see where they’re going more easily. The trucks you receive should really have proper access doors, too. Avoid barn-type doors, which require an unobstructed swing clearance to open and close. Instead, a roll-up door can be easily accessed from the side, which offers improved load access. In this case, shutters bail up above the door aperture, eliminating the need for internal roof mounted rails.
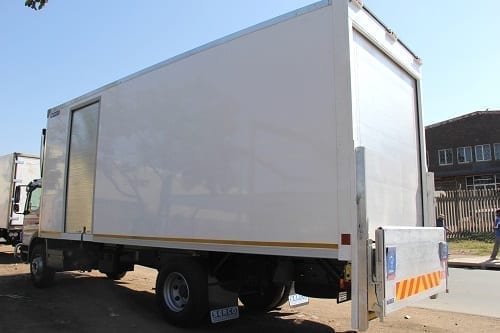
Trucks that can be loaded and unloaded from the side assist staging greatly.