For over three decades, Pexmart has led the way as a manufacturer, OEM supplier and turnkey installer of HDPE, LDPE and PVC plastic pipe systems in South Africa, and across Africa.
Expertise in detailing, costing, construction and project management, delivery and installation meet the exacting specifications of the agricultural, building, commercial, industrial, mining and municipal sectors. Leading through technology and a winning team approach, Pexmart continues to build on its reputation as a multifaceted specialist providing tailored solutions for the local and international markets. Irrespective of the project scale, the focus is on efficient and cost-effective execution in the fields of manufacturing, installation and maintenance. Growth is being sustained by a dual-pronged focus on public and private sector clients. Forming part of its expansion strategy, Pexmart concluded the acquisition of Spiral HDPE Pipe’s operations in 2018. This was followed in 2019 by the acquisition of Marley Pipe Systems’ HDPE and FLEX plant in Rosslyn, Gauteng. A member of theSouthern African Plastic Pipe Manufacturers Association (SAPPMA), Pexmart adheres to and fully supports SABS and SAPPMA’s Quality Assurance Programme. Products are manufactured to meet high- and low-pressure ratings. Alongside pipe systems, these include the PEX-FLEX range of flexible hoses specially developed for a wide range of applications, including domestic, firefighting, irrigation, industrial and mining. “HDPE solid wall pipe has been used in potable water, sewer and mining for many decades and is rapidly growing as the preferred material for pipe lining and relining, slurry applications and for use in dolomitic areas,” explains Andre Janse van Rensburg, CEO, Pexmart. “HDPE is also increasingly the preferred choice for municipal water and wastewater projects.” We can manufacture pipe sizes ranging from 16 mm to 1 000 mm (HDPE) and 300 mm to 3 500 mm for spiral structured wall pipe that can be welded.
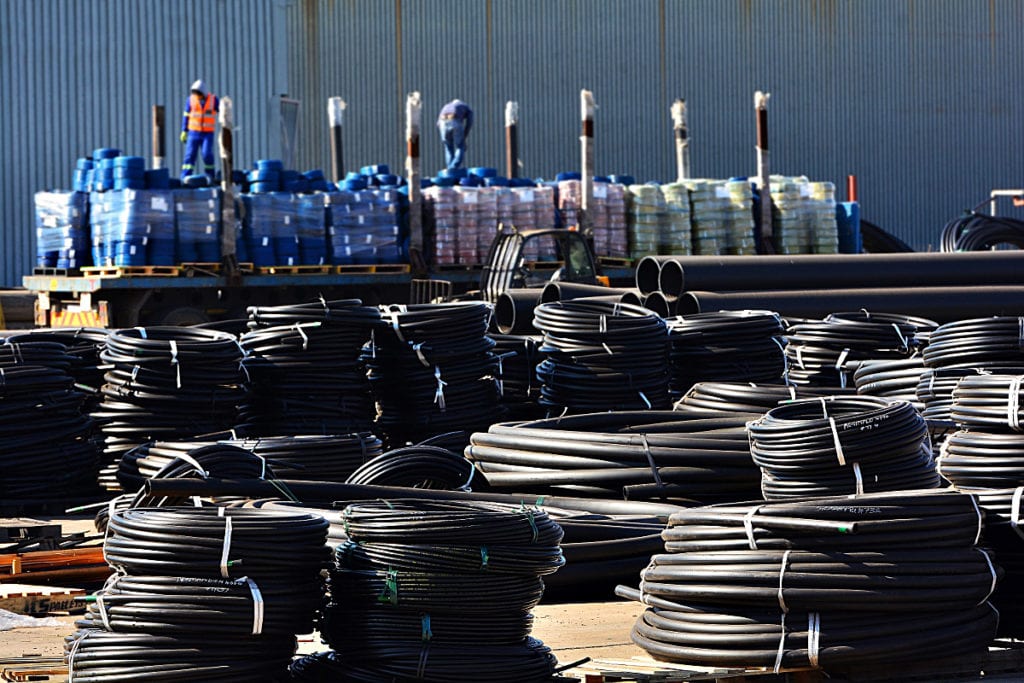
Spiral HDPE pipe
The key advantage of the spiral range is that the corrugated design provides superior ring stiffness and rigidity while using less material in the manufacturing process compared to sold wall pipes. Providing a more cost-effective solution, they are well suited to applications like culvert stormwater management and gravity trunk sewer mains. Other custom fabricated spiral HDPEproducts include manifolds, manholes, tees and reducing fittings.
Mining and municipal
The ability to fabricate to demanding production timelines and specifications is underscored by the fact that Pexmart has ongoing supply and installation contracts in place within the mining sector. These include a five-year contract with Debswana Diamond Company, plus contracts with Royal Bafokeng Resources, and Anglo American Platinum. Within the municipal market, Pexmart has provided specific solutions for various municipalities and metros over the years, an example being the City of Tshwane’s Water & Sanitation Department, plus various rural development initiatives. Other key public sector clients include Eskom and Gautrain. “What sets Pexmart apart is our commitment to our staff. We strive to attract and retain experienced personnel to facilitate balanced growth and promote a culture of continuous improvement. As a result, we have a strong core team of loyal, highly skilled employees who have a ‘can do’ attitude and are focused on achieving successful outcomes for our customers,” says Janse van Rensburg.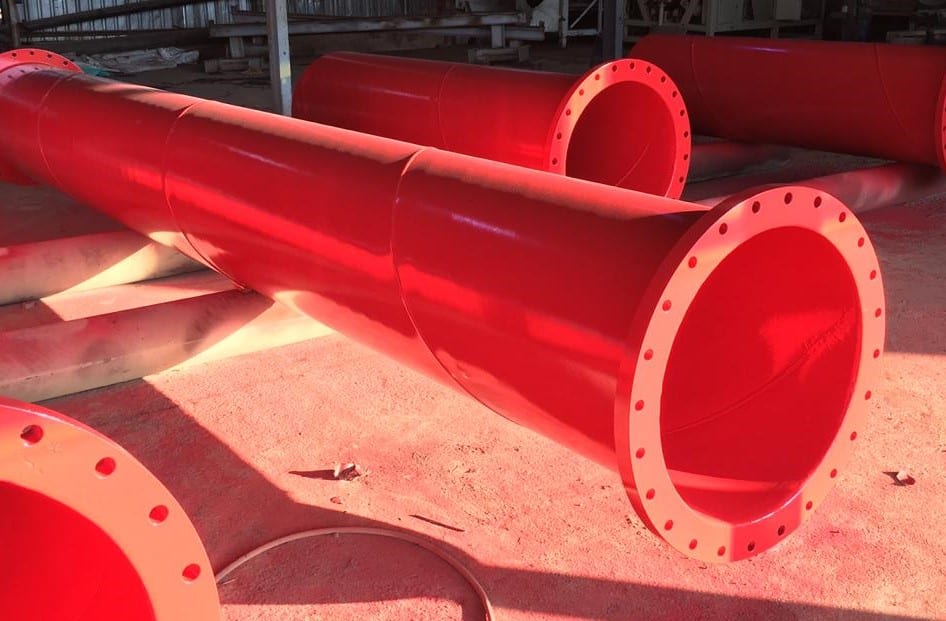
Lined pipe systems
Alongside its solid wall offerings, Pexmart develops custom HDPE lining systems for the carbon steel pipe sector. It’s a proven fact that HDPE liners provide new or older steel pipes with greater strength and protection from erosion and corrosion in more aggressive environments – a key consideration in extending asset life. The interior walls of the HDPE liner are also very smooth, resulting in superior fluid flow due to a reduction in resistance and friction. Applications include the fluid transfer of acid water, crude oil, slurry, wet gas, raffinate and effluent. “Our lined pipe systems have successfully passed all ASTM F1545 requirements,” says Marina van der Walt, sales and marketing manager, Pexmart, adding that, prior to installation, HDPE lined fittings are pressure tested at 1.5 times more than theclient’s service pressure threshold, to ensure exacting compliance.
“In addition to reducing friction, our liners lower operating pressures, provide a substantial cost saving on flanges and energy bills, in addition to extending the longer-term replacement of carbon steel pipeline systems,” she continues. “Our liner systems also reduce risks associated with leaks and environmental impacts.”
Liners are custom extruded to the exact internal diameter of the steel pipe. After the liner is installed, HDPE sealing stubs are welded to the ends of the liner and then covered with blowing flanges. On-site pipeline lengths ranging from 100 m to 1 000 m can also be lined in situ by Pexmart’s installation team, depending on the pipeline route and terrain contours.HDPE continuous butt-welding
The most important event during the continuous lining process is the thermal butt-fusion method employed. Thermal butt-fusion provides an economical and fast method of delivering a complete, long continuous length of HDPE pipe. The fused joints are as strong as the pipe itself, providing a continuous leak-proof system. Pexmart’s expert technicians use high-tech welding machines for enhanced efficiency, productivity and safety. Their general mantra is: “For every metre of steel pipe welded, there’s a metre of HDPE liner butt-welded.” The welding quality and internal seam line-up in pipeline welding are crucial to avoid defects during the HDPE lining process. For this reason, Pexmart ensures that that correct internal line-up pipe clamp is used for welding preparation. This avoids edge misalignment and provides full alignment to the weld seam during the entire welding process.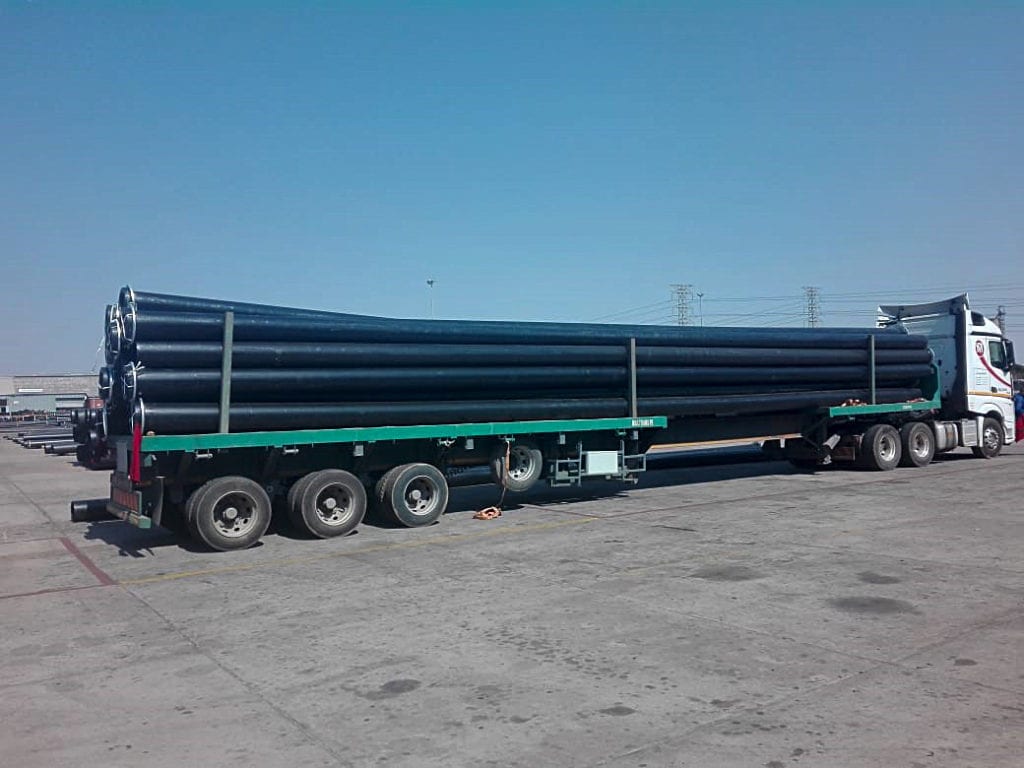
355 mm x 18 m PN 12.5 PE 100 HDPE pipe
Pipeline pre-commissioning and commissioning
“After a pipeline is constructed, and before it is put into service, key activities are required in order to ensure the pipeline meets the requirements of its owner or operators,” says Van der Walt. Pipeline pre-commissioning is used for bolt-up cleaning and commissioning of the pipeline and carrying out inspections using torque converters with the correct torque settings, CCTV camera inspection and pressure testing (hydro or pneumatic).Optic fibre duct
In addition to the fluid transfer market, Pexmart designs and produces corrugated pipe for the electrical and telecommunications sector: 110 mm diameter pipes are manufactured in 6 m and 50 m lengths and supplied with seal and coupler. Additionally, micro ductingoptions can be produced to meet specific project requirements. Designed for slots and micro-trenches, a key feature of the PEXMICRO duct range is their robust construction, making them highly resistant to crushing. They are also UV resistant. Inner ducts/subducts (with 32 mm and 40 mm outer diameter) provide a means of mechanical protection for fibre-optic cable and are installed in outer ducts or direct-burial application. The fibre-optic ducting series comprises the 8/5, 12/10, 14/10 (with 1-way, 2-way, 4-way, 7-way enclosures). Various colour options are available on request. The standard lengths supplied are 500 m, 1 000 m and 2 000 m.
Turnkey integrity
As a recognised leader, Pexmart meets the challenges and demands of the pipeline industry by providing the best products and systems available, as part of their turnkey approach to projects. Company specialists provide advice on regulations and compliance, design and installation, backing this up with input from respected consulting engineering experts in pipeline integrity and management. In this way, Pexmart delivers the right solution. “We maintain our leading-edge approach by continually gaining new insights and knowledge utilising the latest technology available, supported by our ongoing research and development programmes,” Janse van Rensburg concludes.