WEC Projects’ NEWgenerator system is a promising alternative to dangerous pit and chemical toilets, particularly in areas where water is scarce. It addresses sanitation, access to water, and energy independence. Kirsten Kelly interviews Wayne Taljaard, managing director of WEC Projects, about the system’s commercialisation and lessons learnt from pilot projects.
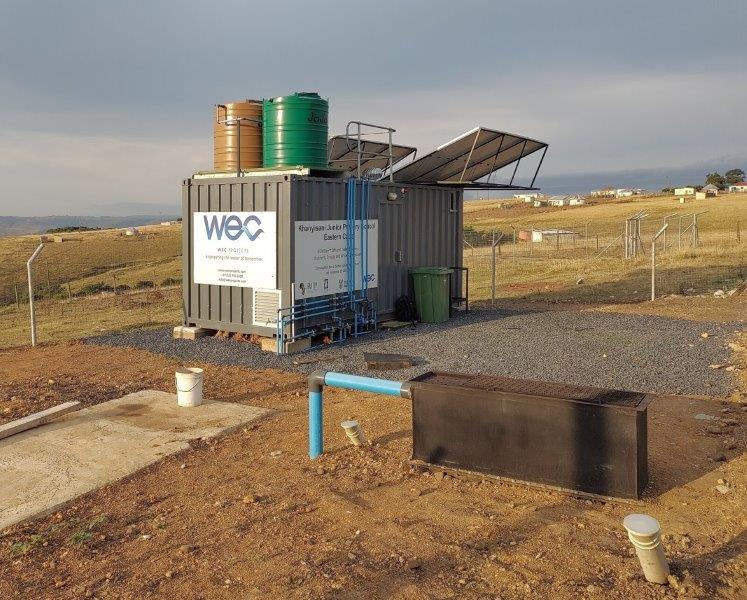
wash basins, the excess, nutrient-rich water was used to grow vegetables for the community, which was appreciated. For the time being, a janitor at Slovoville is being paid to keep the toilets clean, and toilet paper and cleaning aids are provided for; however, this is not a sustainable model and communities will have to take responsibility for supplying these necessities going forward.
“One of the challenges in prototyping the NEWgenerator system was adopting a mindset change. As a leading EPC contractor, WEC Projects specialises in the provision of engineered solutions in the water and wastewater treatment industry. We had to adjust our approach from a company that typically builds large-scale, complex water treatment plants to building tiny, simple water treatment plants. For instance, a NEWgenerator system (designed for 100 people) will process roughly 1 250 ℓ/day of wastewater. One of our treatment plants will do that in
just a few hours. Sourcing equipment such as, for example, smaller-sized pumps for sewage has been difficult; one needs to consider cost, flow rates and maintenance,” states Taljaard.
Simplifying technology and reducing costs
Taljaard adds that people managing the NEWgenerator system are not trained water professionals and have no supervision. “They can be a janitor or a handyman that may not have an education or even be literate. He or she will not use a human-machine interface (HMI) but willtypically communicate a problem over the phone and the team from WEC Projects must respond remotely. These plants must therefore be operationally simple to run but also have the functionality in the backend for remote monitoring.”
Sanitation is often needed in rural areas with no grid structure or water source. “This is where the NEWgenerator system shines, as it does not require a full sewer network or power supply. A unique feature of the NEWgenerator is that it can run independently off the power grid, using solar power to operate or it can be hooked up to a generator. This makes it particularly suitable for use in South Africa, where the country’s unreliable power grid – prone to loadshedding and unscheduled outages – has had an adverse impact on existing infrastructure and equipment. Presently, even developed urban areas are often without power or access to water for prolonged periods. Furthermore, up to 99% of water can be recycled for reuse in the system. The NEWgenerator system can treat the sewage from toilets and then recycle the treated wastewater back to the toilet for reuse, ensuring a consistent water supply,” says Gunter Rencken, technical director, WEC Projects.
The NEWgenerator system incorporates an anaerobic bioreactor to treat biological matter and breakdown solids, ultrafiltration to remove solids, sequential nutrient capture tanks, and chlorine disinfection. For larger systems, biogas produced can be captured and used for applications such as cooking and heating.Engineering and commercialisation
WEC Projects has invested a great deal of time, money and expertise in engineering development and commecialisation of the NEWgenerator. A lot of this work has also been funded and supported through the SASTEP initiative of the Water Research Commission (WRC). SASTEP is a platform that fast-tracks the adoption of innovative and emerging sanitation technologies in South Africa through fostering local manufacturing and commercialisation. With more than 2 700 informal settlements in South Africa and approximately 13% of its population living there, the WRC believes that a lot of funding can come from corporates who can allocate their CSI towards providing better sanitation solutions (and thereby providing dignity) to needy communities.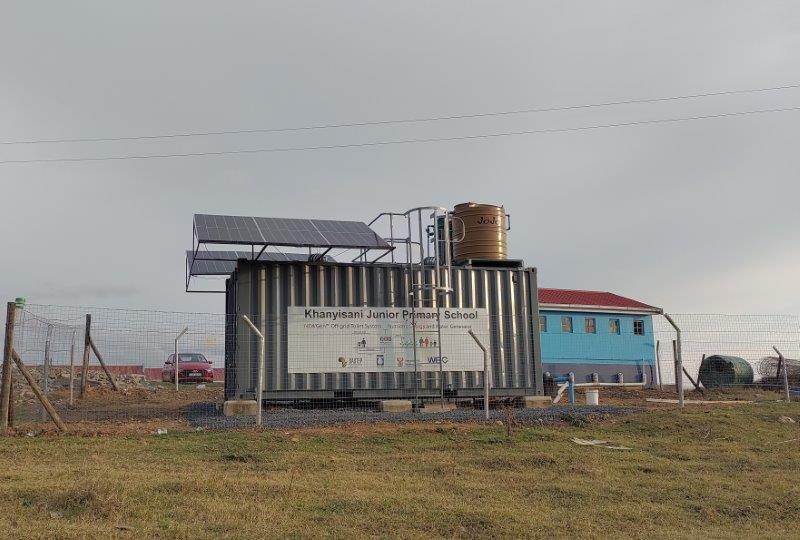
sanitation is needed. Often, there is no grid system, no water supply, no roads to transport the system, and a lack of machinery like excavators to dig holes for septic tanks. A complete paradigm shift is needed when addressing sanitation and absolutely everyone involved needs to be on the same page. The NEWgenerator system has produced good results and we believe it is the future for sanitation,” concludes Taljaard.
NEWgenerator at an Eastern Cape Primary School
WEC Projects recently connected the Khanyisani Primary School’s toilet block to a water and waste treatment and recycling system (NEWgenerator 100 system). The school in Lubunde, near Bizana in the Eastern Cape, lacks consistent water supply. NEWgenerator 100 is capable of handling waste for up to 100 users, and was customised to include waste from four unisex urinals, which is redirected back to theplant to supplement the liquid content of the wastewater for treatment and recycling. The treated water, which is not suitable for consumption, is fed back to flush the toilets, resulting in a significant reduction in water consumption by the school, which relies mainly on rainwater for drinking water. Monitored and controlled both locally and remotely via an interface connected to a programmable logicontroller, the NEWgenerator system is maintained and operated by a trained school staff member with the support of WEC. Samples of the recycled water are taken monthly for analysis by an accredited laboratory to ensure that the treated water meets ISO 30500 discharge standards. WEC will continue to operate the system with the Water Research Commission until April 2024.